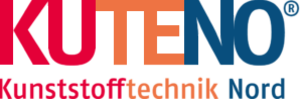
KUTENO, Rheda-Wiedenbrück
Kunststofftechnik Nord
14. bis 16. Mai
www.kuteno.de
Bilder: AIM3D GmbH
Die Verwendung von Granulaten beim 3D-Drucken mit Kunststoffen erweist sich vor allem bei Bauteilen mit Fasern als wettbewerbsfähig. Generell unterscheidet man zwischen faserverstärkt (GF) und fasergefüllt (wenn es nur kurze Fasern sind).
Zwei Werkstoffe sind aufgrund der Verbreitung in der kunststoffverarbeitenden Industrie besonders interessant: PPS GF40 (Polyphenylensulfid) und PA6 GF30 (Polyamid). Sie verbinden herausragende mechanische Eigenschaften mit Medien- und Temperaturbeständigkeit. Die ExAM 255 greift dabei, als sogenannter Pellet-Drucker, auf handelsübliche Granulate zurück, wie sie auch in der Spritzgiesstechnik verwandt werden. Dies ergibt eine sehr wettbewerbsfähige Preisstellung des 3D-Drucks nach dem Composite Extrusion Modeling (CEM-Verfahren) verglichen mit konventionellen Fertigungsstrategien. Der Preisvorteil im Materialeinstand für ein verarbeitetes Bauteil bewegt sich je nach Werkstoffgruppe zwischen 80 und 96 Prozent. Solche Bauteile weisen meist eine höhere Dichte mit hohen Zugfestigkeiten auf. Für den Verarbeiter ergibt sich zudem ein hohes Mass an Flexibilität, da das Material nicht modifiziert werden muss. Identisches, zertifiziertes Material bedeutet, gleiche bis vergleichbare Eigenschaften, wie Wärmeleitfähigkeit, Medienresistenz, Dämpfung, mechanische Eigenschaften, Schrumpf oder Dichte. Ergänzend ist eine Langfaserverstärkung mit bis zu 3 mm Faserlänge möglich, bei einem Füllgrad von bis zu 60 Prozent. Am Materialschliff von PA6 GF30 zeigt sich eine weitere Charakteristik der ExAM 255-Anlage: Sie bietet hohe Folgetreue der Faserorientierung mit den Extrusionsbahnen (Druck der Füllung/Infill +45º/-45º). Die Bahnsteuerung kann während des Druckens zur Festigkeitsoptimierung des Bauteils genutzt werden. Die Wirtschaftlichkeit ergibt sich nicht zuletzt aus den günstigen Maschinenstundensätzen und der hohen Energieeffizienz der 3D-Druckanlage. Die Summe der Charakteristika einer ExAM 255 bietet enorme Vorteile im 3D-Druck, da Polyamid-Anwendungen sehr verbreitet sind und sich hier erstmals ein preisadäquates 3D-Verfahren anbietet.
Hohe Präzision im 3D-Druck
Entscheidend für Verarbeiter ist die Genauigkeit eines 3D-Druckers. Die ExAM 255 erreicht Genauigkeiten von bis zu 25µm, natürlich in Abhängigkeit von der Aufbaugeschwindigkeit. Aus der Konstruktion ergibt sich das Mass der Präzision am Bauteil: Im Bauraum der ExAM 255 arbeiten zwei Granulat-Extruder, die über separate Feedstocks mit Material versorgt werden. Der Bauraum selbst misst 255x255x255 mm3 und ist passiv beheizbar bis 60 ºC. Die Baurate (mit einer 0,4 mm Düse) gibt AIM3D mit bis zu 40 cm3/h, abhängig vom gewählten Material, an.
Bei der Investitionsentscheidung spielt die Flexibilität der druckbaren Werkstoffe eine zentrale Rolle. Die ExAM 255 deckt als Alleinstellungsmerkmal ein sehr breites Spektrum von Werkstoffen ab. In der Werkstoffgruppe Metalle stehen vor allem Stähle, Titan, Buntmetalle und Hartmetalle im Fokus. Bei den Kunststoffen können identische Kunststoffarten auf Granulatbasis gedruckt werden, wie man sie aus klassischen Verfahren kennt. Dazu treten dann noch keramische Anwendungen. Die Materialzuführung der ExAM 255 erfolgt über paarweise angeordnete Materialbehälter (Feedstock) oberhalb des Bauraums der ExAM 255. Diese Anordnung ermöglicht einen Mehrkomponenten-Druck von Polymeren, aber auch Kombinationen von Metall, Kunststoff oder Keramik. Die Optionen dieser Anlagentechnik ermöglichen darüber hinaus eine Verfahrenskombinationen mit hybriden Bauteilen, bei denen eine Komponente klassisch gefertigt wird und eine zweite Komponente gedruckt wird. Dies ergibt viele perfekte Lösungen für nahezu jede industrielle Anwendung.
Referenzen in Instituten und der Industrie
Neben zahlreichen Instituten, die die ExAM255 für das Rapid Prototyping und die Werkstoffforschung einsetzen, verwenden auch bekannte Industriekunden den Multimaterial-3D-Drucker ExAM 255. Darunter finden sich industrielle Anwender, wie Brose, Schunk, Schaeffler oder BASF. Bei diesen Anwendern stehen Klein- und mittlere Serien mittels 3D-Druck im Fokus. Die Akzeptanz bei den Verarbeitern ergibt sich strategisch aus der Verwendung von Serienmaterial. Dies verkürzt die Entwicklungszeiten enorm und die Bauteile orientieren sich optisch und von den Bauteileigenschaften nahe an der Serienfertigung. Auch alternative Bauteil-Konstruktionen mit bionischen Eigenschaften und Leichtbau-Strategien können auf der ExAM 255 erprobt werden. Ein wesentlicher Vorteil ist zudem die «One-Shot-Technik»: Ein Bauteil wird sukzessive aufgebaut ohne Montageaufwand, auch mit Funktionsintegration. Ein konventionelles Bauteil kann mittels einer additiven Fertigungsstrategie durch Reengineering konstruktiv und funktional optimiert werden. Der besondere Charme des CEM-Verfahrens sind materialhybride und verfahrenshybride 3D-Bauteilgeometrien für ein Höchstmass an Flexibilität und konstruktiver Freiheit. In Bezug auf Wirtschaftlichkeit, Flexibilität, Präzision und Aufbauraten bietet die ExAM 255 ideale Voraussetzungen, das Additive Manufacturing als Ergänzung konventioneller Fertigungsstrategien zu erschliessen.
INFOS | KONTAKT
AIM3D GmbH
Industriestrasse 12
D-18069 Rostock
T +49 (0)381 3676 609-0
www.aim3d.de
kontakt@aim3d.de
Fused Granulate Modeling-Verfahren (FGM)
Der Anbieter AIM3D GmbH, Rostock, bietet dazu patentierte 3D-Drucker in zwei Bauraumklassen an: ExAM 255 und ExAM 510. Diese Multimaterial-3D-Drucker arbeiten nach dem Fused Granulate Modeling-Prinzip (FGM).
Das Fused Granulate Modeling-Verfahren (FGM) basiert auf dem weit verbreiteten thermoplastischen Schmelzschichtverfahren (FDM/FFF) und gehört damit zu den additiven Fertigungsverfahren und zur Gruppe der Material Extrusion (MEX), Untergruppe Fused Granulate Fabrication (Pellet-MEX).
Der FGM-Extrusions-Druckkopf verarbeitet das Granulat dabei zu einem dünnen Schmelzfaden und trägt diesen auf dem Baufeld auf. Durch die automatische Generierung von Stützmaterial lassen sich auf diese Weise auch komplexere Formen umsetzen, um Sonderfertigungen oder Prototypenfertigung in der Spritzgiesstechnik nutzen zu können.
Die Besonderheit dieses Verfahrensansatzes ist das günstige Ausgangsmaterial: Im Gegensatz zu den gängigen Schmelzschichtverfahren, wie dem Fused Filament Fabrication (FFF), wird beim FGM kein aufwendig produziertes Filament, sondern handelsübliches, zertifiziertes thermoplastisches Spritzgiessgranulat aus der Serienfertigung verwendet.
Der Preisvorteil im Materialeinstand für ein verarbeitetes Bauteil bewegt sich je nach Werkstoffgruppe zwischen 80 und 96 Prozent.
Charakteristika eines 3D-CEM-Extruders
Die gehärtete Düse eines CEM-Extruders aus Spezialstahl ermöglicht einen hohen Austrag von bis zu 250 cm3/h. Sie ist schnell wechselbar und wartungsfreundlich. Das ist wichtig bei sehr abrasiven Werkstoffen, wie beispielsweise mit Glasfaser verstärkten Polymeren, Metallen oder Keramik. Ein 3D-CEM-Drucker ermöglicht bei polymeren Granulaten, verglichen zu Filament-Druckern, Aufbauraten von 2 bis 20-fach höherer Geschwindigkeit (kg/h).
Prozesskette
Ausgangsmaterial (Feedstock) einer CEM-Fertigung sind Metall-/Keramikpulver plus thermoplastische Binderkomponenten vorgemischt als Polymer-Granulat im 3D-Drucker. Anschliessend erfolgt der Bauteilaufbauprozess im Drucker. Werden Metall/Keramik verarbeitet, entsteht ein sorgenannter «Green Part», welcher für die Sintereinheit entbindert werden muss um ein «Brown Part» zu werden. Finale Nachbearbeitung ist das Sintern um die Verbindung der Metallpartikel im Bauteil zu erzeugen und die Dichte zu erhöhen mit dem Ergebnis eines fertigen «Metal Part». In der Prozesskette muss natürlich der Volumenschrumpf ausbalanciert werden.
Materialvielfalt und Materialeigenschaften
Das Alleinstellungsmerkmal eines 3D-CEM-Druckers ist die Materialvielfalt mit der Verarbeitbarkeit von Polymeren, Metallen und Keramik auf einer universellen 3D-Druckanlage. Dies wird optional ergänzt durch eine Verfahrenskombination (hybride Bauteile) oder Materialkombinationen (Mehrkomponententechnik). Identisches, zertifiziertes Material anstelle von Filamenten bedeutet gleiche bis vergleichbare Eigenschaften zum Spritzguss, wie Wärmeleitfähigkeit, Medienresistent, Dämpfung, mechanische Eigenschaften, Schrumpf oder Dichte. Ergänzend ist die Verarbeitung von Langfaserverstärkten Materialien mit bis zu 3 mm Faserlänge möglich, bei einem Füllgrad von bis zu 60 Prozent. Dies bietet enorme Vorteile im 3D-Druck, da Polyamid-Anwendungen sehr verbreitet sind und sich hier ein preisadäquates 3D-Verfahren anbietet.
Ein 3D-CEM-Drucker erzielt daher neben hohen Dichten, auch hohe Zugfestigkeiten. Für ein Polyamid (PA6 GF30) werden beim klassischen Spritzgiessen Zugfestigkeiten von 110 bis 180 MPa erzielt. Ein 3D-CEM-Drucker, wie die ExAM 510 erreicht knapp 140 MPa. Jüngste Entwicklung ist das Voxelfill-Prinzip: Dabei werden Kammern des Bauteils zur Überwindung inhomogener Festigkeiten im 3D-Druck schachbrettartig selektiv gefüllt. Die homogeneren Zugfestigkeiten die somit erzielt werden sind daher einzigartig für einen 3D-Drucker.
Fazit
Das CEM-Verfahren eröffnet mit einem 3D-Multimaterialdrucker ein breites Anwendungsspektrum von der Kleinserie (AM) bis zu mittleren Serien von bis zu 100’000 Teilen/Jahr und die Ergänzung des Pulverspritzgiessens (PIM) oder des Spritzgiessens (SGT) durch vorlaufende Prototypen-Fertigung. Der Einsatz zertifizierter Granulate, Metall- und Keramikpulver bietet neben den Vorteilen bei den Stückkosten, eine ideale Strategie von Prototypen zum Einstieg in Serienfertigung. Time-to-Market heisst hier das Zauberwort.
Internationale Fachmesse für optische Technologien, Komponenten und Systeme
14. bis 16. Mai
www.optatec-messe.de
Internationale Ausstellung und Konferenz für Spulentwicklung, Isolierung und Elektrofertigung
14. bis 16. Mai
www.coilwindingexpo.com
Fachmesse für Industrieautomation
15. und 16. Mai
www.automation-heilbronn.com