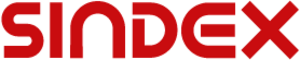
Sindex, Bern
Treffpunkt der Schweizer Technologiebranche
2. bis 4. September
www.sindex.ch
Bilder: ALMiG Kompressoren GmbH
Die Ziegler GmbH fertigt hochpräzise Komponenten für die Flugzeug- und Automobilindustrie. Druckluft ist dabei in allen Maschinen im Einsatz. Weil deren Anzahl mit den Jahren zunahm, stiessen die bisherigen vier Schraubenkompressoren an ihre Grenzen. ALMiG ersetzte diese durch drei direktgetriebene Schraubenkompressoren der Baureihen V-Drive und Variable XP. Mit ihrer Energiespar-Drehzahlregelung passen sie sich an permanente Lastwechsel an und vermeiden kostenintensive Leerlaufzeiten. Ziegler kann bis zu 40’000 kWh im Jahr einsparen – und erhielt aufgrund der hohen Energieeffizienz Fördergelder vom Bund.
Klaus Welte sagt: «Bei uns kommt es auf höchste Präzision an» und zeigt auf einen Behälter, in dem sich blitzblanke und komplex geformte Bauteile befinden. Er ist Teamleiter für den Bereich Präzisionsentgraten und Teileendbearbeitung bei der Ziegler GmbH in D-88697 Bermatingen am Bodensee. «Mit etwa 160 Mitarbeitern fertigen wir hier Bauteile in geringen Stückzahlen», beschreibt er. Die Durchschnittsmengen liegen zwischen 50 und 70 Teilen. Diese können nur wenige Millimeter dünn oder auch mehrere Kilogramm schwer sein, beispielsweise Fahrwerkskomponenten. Zum Einsatz kommen sie in der Automobil- und Flugzeugindustrie – in Branchen, in denen es um die Personenbeförderung geht, und damit können sie auch sicherheitsrelevante Funktionen übernehmen. Zu den Hauptkunden des Familienbetriebs zählen insbesondere Zulieferer der grossen Hersteller. Die Ziegler-Gruppe hat im knapp 4 km entfernten D-88677 Markdorf noch einen zweiten Standort, der unter anderem Ersatzteile und Zubehör für Drehmaschinen fertigt.
«Sicher spüren wir die Auswirkungen der Covid-19-Pandemie», sagt Klaus Welte und zeigt in die Halle: Der Maschinenpark ist nur zum Teil in Betrieb. «Auch wenn wir das Ende der Krise noch nicht absehen können, Sorgen mache ich mir keine. Wir stehen gut da, und wir haben schon in der Vergangenheit immer nur dann investiert, wenn wir es uns das auch leisten konnten.»
Ohne Druckluft geht nichts
Zu diesen Investitionen gehören auch drei neue Druckluftkompressoren von ALMiG. «Wir haben in den vergangenen zehn bis 15 Jahren unser Personal nahezu verdoppelt. Kontinuierlich ist auch der Maschinenpark gewachsen», erläutert der Teamleiter. Damit stieg natürlich auch der Bedarf an Druckluft, denn ohne dieses teure Medium läuft keine Anlage – ob nun Werkzeuge automatisch gewechselt oder Zylinder bewegt werden müssen. Im Einsatz waren bis dahin vier in die Jahre gekommene Schraubenkompressoren. Alle Anlagen stammten von ALMiG. «Wir konnten über die Jahre sehr gute Erfahrungen mit diesen Maschinen sammeln, insbesondere bei der Verfügbarkeit», berichtet Klaus Welte. Langsam aber sicher stiessen sie jedoch immer mehr an ihre Leistungsgrenzen.
«Druckluft ist bei uns ein sehr hohes Gut, allerdings auch ein enormer Kostenfaktor», sagt Teamleiter Klaus Welte. «Wir wollten sowohl den steigenden Bedarf an Druckluft decken können, als auch dauerhaft unsere Energiekosten senken.» Dass die Verantwortlichen weiterhin auf Kompressoren aus dem schwäbischen Köngen setzen, war keine Frage. Sehr hoch schätzt der Teamleiter die Beratung von ALMiG-Gebietsverkaufsleiter Volker Gräschke, der das Unternehmen am Bodensee seit Jahren betreut. «Um die passende Lösung zu finden, führten wir eine Druckluftanalyse durch», berichtet Volker Gräschke. «Auf dieser Grundlage lieferten wir direktgetriebene, drehzahlgeregelte Schraubenkompressoren – zwei der Baureihe V-Drive 75 sowie eine kleinere Variable XP 22.» Weil diese Anlagen energetisch besonders gut arbeiten, konnte Ziegler mit Unterstützung des ALMiG-Experten Fördergelder beim Bundesamt für Wirtschaft und Ausfuhrkontrolle (BAFA) beantragen. Ein weiterer triftiger Grund für die Fertiger vom Bodensee, in die neuen Anlagen zu investieren. «Um diese Fördergelder zu erhalten, erfüllen unsere Kompressoren alle erforderlichen Voraussetzungen», beschreibt Volker Gräschke.
Kompressoren der neuesten Generation
Die leistungsstarken Schraubenkompressoren V-Drive 75 und die Variable XP 22 gehören zur neuesten Generation. Das Besondere ist ihre optimierte Energiespar-Drehzahlregelung. Damit erreichen die Anlagen einen sehr guten Wirkungsgrad über den gesamten Drehzahlbereich. Die Drucklufterzeugung lässt sich genau an den tatsächlichen Bedarf anpassen. Durch die Vermeidung von Leerlaufzeiten sowie permanenten Lastwechseln – und der damit verbundenen höheren Verdichtung – wird Ziegler erheblich Strom sparen können – laut Berechnungen bis zu 40’000 kWh im Jahr. Im Vergleich mit Kompressoren, die im Last-Leerlauf geregelt werden, sparen die ALMiG-Geräte schon allein dadurch rund 30 Prozent Energie. Die V-Drive 75 lassen sich bei acht bar zwischen 3,06 und 13,0 m3/min regeln, die Variable XP 22 zwischen 0,85 und 3,7 m3/min. Bei beiden Typen ist der Betriebsdruck von 5 bis13 bar stufenlos einstellbar. «Jeweils einer der beiden V-Drive-Kompressoren übernimmt die Last, die vorher die vier alten Maschinen gemeinsam getragen haben», erklärt Klaus Welte.
Der Bedarf an Druckluft ist in Bermatingen ganz unterschiedlich. «Wir arbeiten hier in der Regel fünf Tage in der Woche in zwei Schichten», beschreibt Klaus Welte. «Vor der Pandemie lag der Tagesbedarf bei etwa 9 m3/min. Eine V-Drive-Anlage läuft aktuell nur zu etwa 50 bis 60 Prozent. Die Druckluftstation ist zurzeit auf 7,8 bar eingestellt und wird in 0,1 bar Schritten reduziert, bis wir am Optimum sind. Denn ein bar macht etwa sieben Prozent Energiekosten aus», sagt Volker Gräschke. Um die Leckagen möglichst gering zu halten, werden Druckluftverluste im Verteilernetz und in den Maschinen permanent kontrolliert und beseitigt. Um das Regelverhalten der Kompressoren weiter zu verbessern, hat ALMiG einen Druckluftbehälter mit einem Volumen von 3000 l installiert. Vorher standen nur 1750 l zur Verfügung.
Sicher gesteuert
Die Steuerung ALMiG Air Control HE (Highend) regelt die Kompressoren verbrauchsabhängig im Verbund – die übergeordnete Steuerung wird ebenfalls durch das BAFA gefördert. Ziegler kann mit dieser Steuerung die Energievorteile der Drehzahlregelung voll nutzen, weil die Station nur so viel Druckluft erzeugt, wie tatsächlich verbraucht wird, und automatisch die beste Kombination aus den verfügbaren Kompressoren wählt. Der Druck bleibt konstant. «Steigt der Verbrauch Richtung Maximalliefermenge der Variable XP 22, schaltet sich eine V-Drive 75 zu und die kleine Anlage nach einer einstellbaren Wartezeit ab. Dabei wird eine Drehzahlreserve beibehalten. So können keine Druckschwankungen durch Zu- und Wegschalten der Kompressoren entstehen, und die Station läuft im wirtschaftlichen Bereich», erklärt Volker Gräschke. In der Hauptlastphase, also in der Hauptproduktionszeit, läuft eine V-Drive 75.
Die zweite V-Drive 75 ist im Standby-Modus. Um eine gleichmässige Auslastung sicherzustellen, erfolgt diese im Grundlastwechsel. In der Schwachlastphase, wenn weniger produziert wird, läuft nur die Variable XP 22.
Die Station passt sich automatisch an das Verbrauchsprofil an. Da sich die Maschinen immer im optimalen Drehzahlbereich befinden, sind sowohl der Energiebedarf als auch die Geräuschemission geringer. Zudem werden die Maschinenbauteile weniger belastet, was sich positiv auf die Lebensdauer der Kompressoren auswirkt. Ein weiterer positiver Nebeneffekt: Durch die Steuerung laufen alle Maschinen etwa 4000 B/h pro Jahr. Das entspricht dem Serviceintervall. Somit können alle Kompressoren an einem Termin gewartet werden, das senkt die laufenden Kosten weiter.
«Von Haus aus sind unsere HE-Steuerungen mit einem Bilanzierungs-Monitoring-System ausgestattet und haben serienmässig einen Webserver», erläutert Volker Gräschke. Dieser ermöglicht es, alle relevanten Daten online auszulesen. Das Laufverhalten der vergangenen Betriebstage oder -wochen lässt sich ablesen und anhand der Daten feststellen, wie stark der Kompressor ausgelastet ist, und wann die Wartung ansteht. Zusätzlich werden die verbrauchte Luftmenge und der Energieverbrauch aufgezeichnet. «Wenn wir merken, dass sich das Betriebsverhalten erheblich verändert hat, können wir sofort reagieren», sagt Klaus Welte.
Neben der permanenten Verfügbarkeit der Druckluft ist Ziegler vor allem die Reinheit des Mediums wichtig – und dass sich kein Kondensat bilden kann. Die bestehende Druckluftaufbereitung aus Vorfilter, Kältetrockner und Feinstfilter von ALMiG wurde übernommen, denn diese war schon ausreichend dimensioniert und redundant ausgelegt. Nach der Aufbereitung wird die Druckluft über ein Sammelrohr mit grossem Querschnitt über den Druckluftbehälter an die Verbraucher geführt.
Mit geregelter Zu- und Abluft kein Wärmestau
Ziegler hatte vorher das Problem, dass die alten Kompressoren zum Teil in einer kleinen Fertiggarage untergebracht waren. Dies führte bei hohen Aussentemperaturen zu thermischen Problemen. Das sollte sich ändern.
Die Fertiggarage gibt es heute nicht mehr – schon allein aus Platzgründen. Dafür steht dort eine moderne Halle mit geregelter Zu- und Abluft, in der die neuen Maschinen untergebracht sind.
«Der Umbau war für alle Beteiligten eine Herausforderung, denn der Betrieb musste ohne Unterbrechung weiterlaufen», erinnert sich Volker Gräschke. Eine genaue Planung und viel Improvisation waren erforderlich. Die Arbeiten fanden meist an Samstagen statt. Zuerst wurde eine der beiden V-Drive-Anlagen und die Variable XP ausserhalb der Bauarbeiten installiert, diese hielten den Betrieb aufrecht. Stückweise wurden die alten Kompressoren und die Fertiggarage ab- und die neue Halle aufgebaut. «Wir haben die zweite V-Drive darin installiert, anschliessend sind wir mit der Variable XP umgezogen und haben die Druckluftaufbereitung mit dem neuen Behälter eingebaut. Als diese in Betrieb waren, zog dann auch die andere V-Drive um», beschreibt Klaus Welte. «Innerhalb eines halben Jahres haben wir den kompletten Umbau ohne Produktionsausfall hinbekommen.»
Hohe Verfügbarkeit sichergestellt
Seit Mai 2020 sind die Kompressoren nun im Einsatz. «Wir vermeiden kostenintensive Leerlaufzeiten und können ordentlich Kilowattstunden im Jahr einsparen», ist Klaus Welte zufrieden. «Vor allem profitieren wir von einer hohen Verfügbarkeit der Druckluft.» Die Schraubenkompressoren sind zudem wartungsfreundlich aufgebaut und benötigen nur alle 4000 Betriebsstunden einen Service: Alle Komponenten sind einfach zugänglich, die Schalldämmtüren können leicht abgenommen werden. Hierdurch verkürzen sich die Wartungs- und Stillstandzeiten deutlich. So bleiben auch die Servicekosten überschaubar.
«Jetzt muss nur die Wirtschaft wieder voll anlaufen. Wir stehen in den Startlöchern», sagt Teamleiter Klaus Welte. Er zeigt auf einen Mitarbeiter, der gerade dabei ist, unter dem Mikroskop mit einem Handschleifer ein komplex geformtes Bauteil zu bearbeiten. «Automatisiert wäre das entweder unmöglich oder bei den geringen Stückzahlen, die wir haben, sehr unwirtschaftlich», sagt er. «Die entstehenden feinen Späne werden mit der Druckluftpistole abgeblasen. Auch das ist eine typische Anwendung bei uns.»
INFOS | KONTAKT
Prematic AG
Märwilerstrasse 43
CH-9556 Affeltrangen
T +41 (0)71 918 60 60
www.prematic.ch
info@prematic.ch
Branchentreffpunkt für Medizintechnikunternehmen
9. und 10. September
www.medtech-expo.ch
Die Fachmesse für Industrieautomation
10. und 11. September
www.automation-wetzlar.de
Weltleitmesse für Fügen, Trennen, Beschichten
15. bis 19. September
www.schweissen-schneiden.com