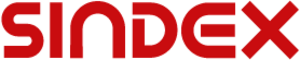
Sindex, Bern
Treffpunkt der Schweizer Technologiebranche
2. bis 4. September
www.sindex.ch
Bild: Klaus Vollrath
Die Kinematik klassischer mechanischer Systeme besteht oft aus Grundelementen wie Stäben, Hebeln, Keilen, Rädern, Drehgelenken usw. Der Konstrukteur kann heute auf standardisierte Baukästen zugreifen, mit deren Hilfe viele Einsatzfälle gelöst werden können. Bei höchsten Präzisionsanforderungen werden jedoch bewegliche Verbindungen wie Dreh- oder Gleitlager zu Schwachpunkten.
Präzision und Lebensdauer werden durch Lagerspiel, Reibung, Verschleiss oder Stick-slip beeinträchtigt. Als Alternative gibt es die sogenannten monolithischen Konstruktionen, deren Verbindungen aus elastisch verformbaren dünnen Stegen bestehen. Bei ihrer Herstellung bietet das Mikro-Wasserstrahlschneiden gewisse Vorteile.
«Monolithische Kinematiken kommen vor allem dort zum Einsatz, wo kleine Bewegungen mit höchster Präzision ausgeführt werden müssen», erläutert Walter Maurer, Inhaber der Waterjet AG. Einsatzbereiche sind beispielsweise die Robotik, die Luft- und Raumfahrt, terrestrische Systeme für die Astronomie sowie Konstruktionen für die Medizintechnik, die Elektronenmikroskopie oder die Uhrenindustrie. Hinzu kommen Kraftübersetzer zum Beispiel für Waagen, Sensoren für Bewegung und Beschleunigung im Maschinenbau sowie Positioniersysteme für Ultrapräzisionsmechaniken in zahlreichen Einsatzgebieten von der Labortechnik bis zur Ausrichtung von Kommunikationsantennen in der Satellitentechnik. Bei diesen monolithischen Kinematiken kommt es nicht zu den typischen Lagerproblemen wie abrupten Sprüngen im Kraft-Wegverlauf, Spiel, Hysteresen bei Richtungsumkehr oder Eigenschaftsänderungen durch Verschleiss. Bei üblichen Dreh- oder Gleitlagern lassen sich diese Phänomene dagegen selbst bei sorgfältigster Ausführung nie wirklich auf Null reduzieren. Zudem sind sie anfällig gegen Korrosion oder dem Eindringen von Staub oder Schmutzpartikeln. Dies erweist sich beim Einsatz unter extremen Bedingungen wie der Luft- und Raumfahrt, im Vakuum oder in kryogener Umgebung oft als erhebliches Handicap.
Aufbau monolithischer Kinematiken
«Wie ihre Bezeichnung schon andeutet, werden monolithische Kinematiken grundsätzlich aus dem vollen Grundmaterial eines einzigen Blechs oder Blocks herausgearbeitet», ergänzt Walter Maurer. Die Verbindung der einzelnen mechanischen Komponenten untereinander erfolgt ausschliesslich über schmale und damit flexible Stege. Diese ermöglichen Biegebewegungen in genau einer Achse, während sie gegenüber Kräften in der anderen Achse eine hohe Quersteifigkeit aufweisen. Diese Stege ermöglichen die gleichen Funktionen wie Drehachsen beziehungsweise Drehgelenke bei «klassischen» mechanischen Konstruktionen. Durch geschickte Anordnung und Dimensionierung können zudem Charakteristiken wie Übersetzungsverhältnisse oder Steifigkeiten definiert werden. Mit solchen Mechaniken sind Bewegungsauflösungen im Bereich von Nanometern bis Mikrometern bei Hublängen bis zu mehr als einem Zentimeter (beziehungsweise ±15° bei rotativen Bewegungen) erreichbar. An den Verbindungen gibt es weder Reibung noch Spiel und damit auch keinerlei Abrieb. Zudem sind diese Konstruktionen ausserordentlich robust und weitestgehend driftstabil.
Herstellverfahren
«Für die Herstellung solcher Bauteile gibt es verschiedene Verfahren mit jeweils spezifischen Vor- und Nachteilen», weiss Walter Maurer. Häufig komme das Elektroerodieren mit Draht zum Einsatz. Dabei erfolgt die Materialabtragung durch Überschlag von Funken in einem Dielektrikum. Damit lassen sich präzise Konturen mit vertikalen Schnittflanken erzielen. Darstellbar sind minimale Stegbreiten bis zu etwa 25 bis 30 µm. Dank des Einsatzes dünner Drähte mit Durchmessern bis herab zu 20 µm erreichen moderne Erodiermaschinen zudem auch sehr enge Schnittspalte. Nachteil sind hohe Bearbeitungszeiten und entsprechende Kosten, da die erforderliche Feinstbearbeitung zahlreiche sukzessive Durchläufe bedingt.
Hauptproblem ist beim Drahterodieren die Oberflächenschädigung des Materials durch die Funkenbildung, die zu einem partiellen Aufschmelzen des Werkstoffs mit nachfolgender schneller Abschreckung führt. Dadurch bildet sich zum Beispiel auf Stählen eine spröde «weisse Schicht» von einigen µm Dicke. Im Oberflächenbereich der oft nur 30 µm dicken Stege verringern diese beidseitigen Schichten den Restquerschnitt «gesunden Materials» erheblich. Hier können mikroskopische Schäden bei dynamischer Beanspruchung zu Dauerbrüchen führen. Zusätzlicher Nachteil der Drahterosion ist die Beschränkung auf elektrisch gut leitende Werkstoffe.
Seltener eingesetzte Verfahren sind die mechanische Bearbeitung durch Fräsen sowie das Laserschneiden. Fräsen macht jedoch nur bei solchen Geometrien Sinn, wo keine schmalen Spalten oder Schlitze im Material vorzusehen sind. Wegen der seitlichen Abdrängung der Fräswerkzeuge ist hierbei zudem die Gewährleistung wirklich senkrechter Schnittflanken umso schwieriger, je dicker das Material und je dünner die Fräswerkzeuge sind.
Mit dem Laserschneiden sind zwar kurze Bearbeitungszeiten möglich, jedoch lassen Präzision und Oberflächenqualität der Schnittflanken deutlich zu wünschen übrig. Auch verbietet sich der Lasereinsatz bei thermisch empfindlichen Werkstoffen wie zum Beispiel Glas- oder Carbonfaserverbunden.
Bearbeitung mit dem (Mikro)-Wasserstrahlschneidverfahren
«Eine bisher noch selten eingesetzte Alternative zu den genannten Verfahren ist das von uns entwickelte Mikro-Wasserstrahlschneiden», sagt. Walter Maurer. Sein wesentlicher Vorteil ist die völlige Schonung des Werkstoffs, da der Abtrag durch den Wasserstrahl ohne jede Erwärmung erfolgt. Dies ist ein wesentlicher Unterschied zum Drahterodieren, bei dem die Oberfläche durch die Funkenüberschläge geschädigt und aufgeraut wird.
Die Achsen der von Waterjet entwickelten Mikro-Wasserstrahlschneidmaschinen erreichen eine Positionsgenauigkeit von ±0,5 µm. Der Strahlkopf erzeugt einen haarfeinen Schneidstrahl mit Ø von nur 0,2 mm bei Durchmesserabweichungen bis herab zu lediglich ±1,5 µm. Damit sind nominelle Endgenauigkeiten bis zu ± 2 µm bei Schnittflächenrauheiten bis herab zu Ra 0,5 µm erreichbar. Die minimalen Schlitzbreiten liegen bei 0,2 mm. Bearbeitet werden können alle Werkstoffe von Kunststoffen über Stähle und Buntmetalle bis hin zu Hartmetallen und härtesten Keramiken. Die maximal bearbeitbare Materialdicke hängt von den Qualitätsanforderungen ab: Bei monolithischen Präzisionskinematiken aus gehärtetem Stahl liegt die Obergrenze bei etwa 5 mm, bei Aluminium, Buntmetallen und Titan je nach Anforderungen 8 bis 10 mm. Bei weicheren Materialien wie Kunststoffen und Kunststoff-Verbunden sind dagegen auch Wanddicken bis 12 mm und teils auch darüber kein Problem.
Schnittflächenqualität
«Beim Mikro-Wasserstrahlschneiden sind die Schnittflanken im Unterschied zum Laser- oder zum Fräsverfahren einwandfrei vertikal», verrät Walter Maurer. Dank raffinierter Auslegung der Geometrie von Düse und Fokussierrohr bleiben der Strahl und damit auch die von ihm transportierten Abrasivkörner über eine Strecke von mehr als 15 bis 20 mm äusserst eng fokussiert. Die Schnittflanken haben dadurch einen rechten Winkel zur Oberfläche. Weiterer «Trick» der von Waterjet konzipierten Strahlkopf-Geometrie ist eine bevorzugt randnahe Verteilung der mitgerissenen Abrasivpartikel im Strahl. Damit wird die kreisförmige Geometrie der Düse bei der Bearbeitung sehr exakt abgebildet. Bei entsprechend ausgelegter Vorschubgeschwindigkeit haben die «Bearbeitungs-Bahnen» sehr geringe Abstände, sodass die Oberfläche der Schnittkante entsprechend glatt ist. Bei besonders hohen Anforderungen können noch weitere Massnahmen wie die Verwendung besonders feiner Abrasivpulver ergriffen werden. Die jeweiligen Vor- und Nachteile der verschiedenen Technologien sind in der Tabelle aufgeführt. Nicht erfasst sind die Kosten, die zu sehr von den individuellen geometrischen Eigenschaften der Teile abhängen. Erwähnenswert ist in diesem Zusammenhang, dass höchste Genauigkeit und Oberflächengüte beim Drahterodieren nur durch bis zu sieben sukzessive Bearbeitungsgänge erreicht werden können, was die Kosten bei diesem per se bereits sehr zeitintensiven Bearbeitungsverfahren erheblich in die Höhe treibt. Beim Mikro-Wasserstrahlschneiden ist dagegen lediglich ein Durchgang erforderlich.
INFOS | KONTAKT
Waterjet AG
Mittelstrasse 8
CH-4912 Aarwangen
T +41 (0)62 919 42 82
www.waterjet.ch
info@waterjet.ch
Branchentreffpunkt für Medizintechnikunternehmen
9. und 10. September
www.medtech-expo.ch
Die Fachmesse für Industrieautomation
10. und 11. September
www.automation-wetzlar.de
Weltleitmesse für Fügen, Trennen, Beschichten
15. bis 19. September
www.schweissen-schneiden.com