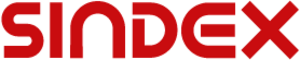
Sindex, Bern
Treffpunkt der Schweizer Technologiebranche
2. bis 4. September
www.sindex.ch
Bilder: TU Darmstadt
Die Prozessüberwachung mit indirekter Sensorik in Kraftnebenflüssen gepaart mit der Datenfusion zusätzlicher Prozessgrössen stellt eine ernst zu nehmende Alternative zu Überwachungsansätzen mit Sensorik im direkten Kraftfluss dar. Indirekte Sensorik vereint Robustheit mit geringem Integrationsaufwand. Die Datenfusion mit Machine-Learning-Algorithmen erzielt zudem gleichbleibende Aussagekraft und schafft die Möglichkeit von Qualitätssicherungsmassnahmen.
KMU der Umformtechnik sind in der Regel durch eine hohe Produktivität sowie komplexe, mehrstufige Prozessketten gekennzeichnet. Mehrstufige Umformprozesse ermöglichen die Herstellung von Bauteilen auf kurzen Prozessrouten und stellen oftmals den wirtschaftlich bedeutendsten Teil der Wertschöpfungskette dar. Obwohl die Digitalisierung eine Steigerung der Gesamtproduktivität verspricht, werden die Potenziale der Digitalisierung in KMU bisher kaum ausgeschöpft [1]. Dieser Beitrag beschreibt zwei Varianten der Sensorintegration sowie die Sen-sordatenfusion in Machine-Learning(ML)-Modellen zur Prozessüberwachung von mehrstufigen Werkzeugen anhand eines dreistufigen Scherschneidwerkzeugs. ML als Teilgebiet der künstlichen Intelligenz bietet die Möglichkeit, grosse zur Verfügung stehende Datenmengen aus inhomogenen Datenquellen zu fusionieren, um Rückschlüsse auf den überwachten Prozess zu generieren [2].
In mehrstufigen Prozessen, die durch eine Vielzahl an Stell- und Störgrössen gekennzeichnet sind, ist die Anforderung an das Fachpersonal hinsichtlich Inbetriebnahme, Prozessführung und Wartung hoch [3]. Die Störgrössen können die Produktqualität negativ beeinflussen und treten in unterschiedlichen Intensitäten sowie zu verschiedenen Zeitpunkten auf. Diese Komplexität führt dazu, dass eine Zustandsüberwachung durch das Fachpersonal während der Prozessführung nicht mehr handhabbar ist. Um Prozessfehler in laufenden mehrstufigen Werkzeugen zu identifizieren sowie zu lokalisieren, ist es notwendig, die Produktionsprozesse sensorisch auszustatten.
Aktuell basieren Überwachungsansätze im industriellen Umfeld auf der Verwendung von Überlastsensorik in Pressen und der Definition von Grenzwerten sowie dem Vergleich mit ausgewählten Referenzzuständen [4, 5]. Die Erfassung und damit verbunden die Identifikation relevanter Prozessgrössen sind stark von dem technischen Fachwissen des Personals abhängig [6]. Zudem ist die Integration von Sensorik aufwendig und führt meist zu einer auf den Prozess angepassten Individuallösung, die bereits bei der Werkzeugauslegung zu berücksichtigen ist. Zusätzlich sind Fragen zur Sensorpositionierung, Messmethode sowie Messkette zu beantworten [7]. Aus industrieller Sicht besteht der Wunsch, leicht integrierbare Sensorik zu qualifizieren, um einen niederschwelligen Einstieg in die digitalisierte Prozessüberwachung zu erhalten.
Versuchsaufbau und -durchführung
Im Fokus dieses Beitrags steht die Sensordatenfusion in ML-Modellen auf Basis von Daten aus nachträglich leicht integrierbarer Sensorik im Kraftnebenfluss für die Überwachung eines dreistufigen Scherschneidprozesses. Demgegenüber stehen die Resultate, die durch eine direkte Sensorpositionierung im Kraftfluss erzielt werden. Die Datenerfassung, -vorbereitung, -transformation und Modellbildung orientieren sich an dem am PtU entwickelten Knowledge-Discovery-in-Timeseries-for Engineering-Applications-Modell (KDT-EA). Bild 1 stellt das KDT-EA-Modell für produktionstechnische ML-Anwendungen dar [8].
Zunächst erfolgt die Auslegung der beiden Messketten im Versuchsaufbau (Bild 2). Einerseits lassen sich die auftretenden Prozesskräfte innerhalb jeder Scherschneidstufe lokal durch direkt im Kraftfluss integrierte piezoelektrische Kraftmessringe erfassen.
Diese Integration der Sensorik im direkten Kraftfluss geht einher mit einer Herabsetzung der Steifigkeit des Werkzeugs und damit einer Veränderung des dynamischen Systemverhaltens. Zudem erfordert ein solcher Messaufbau eine frühzeitige Berücksichtigung in der Werkzeugkonstruktion. Die indirekte Krafterfassung erfolgt durch zwei piezoelektrische Kraftmessdübel, die jeweils zwischen den einzelnen Umformstufen positioniert sind. Zusätzlich wird die Beschleunigung in vertikaler Richtung mit einem mittig an der stösselseitigen Grundplatte installierten piezoelektrischen Beschleunigungssensor gemessen. Eine Fusion verschiedener Datenquellen sowie die Nutzung von Beschleunigungsdaten zur Prozessüberwachung bergen grosses Potenzial zur Fehler- und Ursachenidentifikation [9, 10].
Die verarbeiteten Rohsignale werden bei Versuchen auf einer Schnellläuferpresse mit 100 Hub/min erfasst. Die daraus resultierende Eingriffszeit der Werkzeuge von 150 ms setzt eine hohe Abtastrate (hier 50 kHz) und die Aufzeichnung von grossen Datenmengen voraus. Zur Reduktion der Datenmenge dient ein induktiver Näherungsschalter, der die Aufzeichnung nur in dem relevanten Teil des Gesamthubs ermöglicht.
Verschiedene Prozesszustände entstehen gewollt durch das Einbringen von künstlichen Verstimmungen in den einwandfreien Prozess. Als Verstimmungen werden die Verschleissarten Schneidkantenverrundung in abgestuften Intensitäten sowie abrasiver Verschleiss am Scherschneidstempel untersucht. Das Ausmass sowie der Ort der Verstimmungen werden variiert. Bild 3 zeigt charakteristische Zeitreihen von vorverarbeiteten Beschleunigungsund Kraftsignalen in Abhängigkeit der dazugehörigen Verstimmung. Ein scharfkantiger Schneidstempel ohne Verschleiss führt zu einem Kraftsignal, das ausschliesslich den charakteristischen Verlauf der Schneidphase darstellt. Zunächst ist ein Kraftanstieg nach dem Auftreffen des Schneidstempels auf dem Werkstück zu verzeichnen. Das Material wird erst elastisch, anschliessend plastisch verformt. Bei Überschreitung der Scherbruchgrenze kommt es zur Rissinitiierung bis zum Reissen des Materials beim Erreichen des Kraftmaximums.
Der Schnittschlag, die schlagartige Entspannung des Gesamtsystems, führt zu einem signifikanten Ausschlag des Beschleunigungssignals. Der Kraftverlauf bei abrasivem Verschleiss ist analog zur Schneidkantenverrundung charakterisiert durch Kraftüberhöhungen in der Ausstossphase bis zum Erreichen des unteren Totpunkts der Pressenkinematik und damit des Scherschneidstempels sowie erhöhter Rückzugkräfte in der Rückzugsphase. Eine Abgrenzung der beiden Fehlerbilder kann durch das Beschleunigungssignal erfolgen, das lediglich in der Rückzugsphase beim abrasiven Verschleiss deutliche Signalausschläge vorweist.
Datenauswertung und Ergebnisse
Nachdem die Versuchsdaten im Schritt der Datenerfassung aufgezeichnet worden sind, folgt im Schritt der Datenvorbereitung die Segmentierung der Rohsignale. Hierbei werden die Zeitsignale skaliert, die Offsets entfernt und für die weiteren Datenverarbeitungsschritte gespeichert. Im Schritt der Datentransformation erfolgt die Überführung der Sensordaten aus dem Zeitbereich in den Frequenzbereich. Durch die Bestimmung mathematischer Kennwerte wird die Datenmenge gegenüber dem zeitdiskreten Signal auf wenige Kennwerte reduziert.
Die berechneten Kennwerte, zum Beispiel die Wölbung, das Signal-Rausch-Verhältnis oder der Scheitelfaktor, werden mittels Varianzanalyse selektiert. So werden redundante Kennwerte identifiziert und Kennwerte, die stark mit den Prozesszuständen korrelieren, ausgewählt. Diese Kennwerte dienen als Eingangsgrösse für den gewählten K-Nearest-Neighbors-ML-Algorithmus. Die Modellbildung erfolgt über eine fünffache Kreuzvalidierung mit einer Unterteilung des Datensatzes in 80 Prozent Trainings- und 20 Prozent Testdaten.
Die Angabe der Prädiktionsgüte des Modells erfolgt anhand der vorhergesagten und der tatsächlich vorliegenden Prozesszustände. Für eine Vergleichbarkeit der beiden Überwachungsansätze werden zwei getrennte ML-Modelle mit Kennwerten aus den jeweiligen Sensoren trainiert.
Die Performanz der jeweiligen Modelle ist in Bild 4 und 5 in Konfusionsmatrizen dargestellt. Es zeigt sich, dass das ML-Modell der direkten Sensorik mit 100 Prozent korrekt vorhergesagten Prozesszuständen die höhere Genauigkeit gegenüber dem ML-Modell der indirekten Sensorik mit einer Genauigkeit von 99,2 Prozent, aufweist. Wird das ML-Modell der indirekten Sensorik gänzlich ohne Beschleunigungswerte trainiert, wird eine Vorhersagegenauigkeit von 96,5 Prozent erreicht.
Einzig die Detektion des Grads der Verrundung liefert bei dem ML-Modell mit indirekter Sensorik lediglich eine Genauigkeit von 97 Prozent. Dies kann auf den sehr feinen Unterschied im Kraftverlauf bei 0,25 und 0,5 mm Schneidkantenverrundung zurückgeführt werden.
Fazit und Ausblick
Die Nutzung direkter Sensorik führt zu einer Erhöhung des Prozessverständnisses, ist jedoch oftmals mit einem hohen Integrationsaufwand und damit einhergehend einer Herabsetzung der Werkzeugsteifigkeit verbunden. In diesem Beitrag konnte dargelegt werden, dass der Einsatz einfach nachrüstbarer Sensorik ebenso sehr gute Ergebnisse bei deutlich geringerem Integrationsaufwand liefert. Defekte Stufen sowie die vorliegenden Fehlerbilder wurden mit einer Genauigkeit von 99,2 Prozent erkannt. Die Verwendung der Prozessüberwachung mittels ML-Modell, der Kraftmessdübel und des Beschleunigungssensors bietet Vorteile aufgrund ihrer Vernetzung. Ein Abgleich dieser Prozessparameter mit den gewonnenen Sensordaten ermöglicht die Plausibilisierung der von der Sensorik erfassten Datengrundlage und lässt Rückschlüsse auf den einwandfreien Sensorzustand zu. Etwaige Fehlerzustände wie Signalrauschen und Wackelkontakte bis hin zum Gesamtausfall der Sensorik können auf diese Weise frühzeitig aufgezeigt werden. Somit resul-tieren in dem Einsatz von vernetzter Sensorik robustere Überwachungssysteme.
ZU DEN AUTOREN
Richard J. Werner, M.Sc., richard.werner@ptu.tu-darmstadt.de,
Andre Kokozinski, M.Sc., andre.kokozinski@ptu.tu-darmstadt.de und
Prof. Dr.-Ing. Dipl.-Wirtsch.-Ing. Peter Groche, groche@ptu.tu-darmstadt.de
TU Darmstadt
Otto-Berndt-Strasse 2
D-64287 Darmstadt
T +49 (0)6151 1601
www.tu-darmstadt.de
Branchentreffpunkt für Medizintechnikunternehmen
9. und 10. September
www.medtech-expo.ch
Die Fachmesse für Industrieautomation
10. und 11. September
www.automation-wetzlar.de
Weltleitmesse für Fügen, Trennen, Beschichten
15. bis 19. September
www.schweissen-schneiden.com