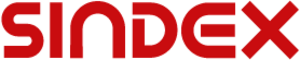
Sindex, Bern
Treffpunkt der Schweizer Technologiebranche
2. bis 4. September
www.sindex.ch
Bei vielen Fertigungsverfahren geraten die Werkstücke in Schwingung. Diese Bauteilschwingungen schädigen die Werkstückoberfläche und erhöhen den Werkzeugverschleiss. Das Fraunhofer-Institut für Produktionstechnologie IPT hat erstmals gemeinsam mit Partnern einen Digitalen Zwilling zur Vorhersage von Bauteilschwingungen bei der Fräsbearbeitung erstellt. Damit können bereits während der Prozessplanung die Prozessparameter optimiert und schädigende Schwingungen vermieden werden.
Bei der Fräsbearbeitung entstehen durch den charakteristischen unterbrochenen Schnitt sowohl am Bauteil als auch am Werkzeug Schwingungen. Diese führen häufig dazu, dass die Oberfläche des Werkstücks beschädigt wird. In der Folge müssen die Bauteile zeit- und kostenintensiv nachbearbeitet werden. Ebenfalls unwirtschaftlich ist der hohe Werkzeugverschleiss, den die Prozessschwingungen verursachen. Dünnwandige Werkstücke, wie sie in der Luftfahrt oder auch im Leichtbau zum Einsatz kommen, haben ein besonders komplexes Schwingungsverhalten, das stark von Werkzeugposition und Zerspankraft abhängt.Gängige Simulationen zur Materialzerspanung bilden zwar einzelne Zwischenzustände des Werkstücks während der Zerspanung ab. Um diese Modelle zur Analyse der dynamischen Schwingungseigenschaften nutzen zu können, müssen sie aber mit unverhältnismässig hohem Aufwand manuell bearbeitet werden.
Kontinuierliche Anpassung der Spindeldrehzahl reduziert Bauteilschwingungen
Ein Team des Fraunhofer IPT entwickelte im kürzlich abgeschlossenen Forschungsprojekt «PhysiX-CAM» erstmals einen Digitalen Zwilling – eine virtuelle, datenbasierte Repräsentation des Bauteils und der Fertigungsum-gebung – zur Vorhersage des Schwingungsverhaltens von Bauteilen am Beispiel einer Blade Integrated Disk (Blisk), einer komplexen Turbomaschinenkomponente mit zahlreichen Einzelschaufeln.
Ziel des Forschungsprojekts war es, die Prozessparameter des Fräsprozesses so einzustellen, dass schädigende Schwingungen vermieden werden. Das Forschungsteam nutzte den Digitalen Zwilling, um neue Prozessstrategien für die Fräsbearbeitung abzuleiten, bei denen die Spindeldrehzahl während der Fertigung kontinuierlich und abhängig von der Werkzeugposition angepasst wird. Vor der Entwicklung dieses neuen Verfahrens war es erforderlich, die geeigneten Drehzahlen und weitere Prozessparameter aufwändig manuell zu ermitteln. Mit der «PhysiX-CAM»-Methode lassen sich die Parameter nun systematisch schon vor der eigentlichen Fertigung auslegen.
Erweiterung der Multi-Dexel-Modellierung zur Simulation der Bauteilschwingungen
Im ersten Projektabschnitt untersuchten die Forscherinnen und Forscher mehrere Ansätze zur Simulation der veränderlichen Werkstückgeometrie. Mit der Multi-Dexel-Modellierung, einer Methode zur geometrischen Modellierung und physikalischen Simulation, fand das Team eine Lösung, die eine hohe Genauigkeit bei vergleichsweise geringem Rechenaufwand bietet. Damit ist die Methode gut geeignet, um Modelle von Zwischengeometrien des Werkstücks, sogenannter In-Process-Workpieces (IPW), zu erzeugen.
Eine Schwäche hat die Multi-Dexel-Modellierung allerdings, denn mit ihr lassen sich nur Oberflächen und keine kompletten dreidimensionalen Körper modellieren. Im nächsten Projektabschnitt galt es aber, die veränderlichen, dynamischen Werkstückeigenschaften im Verlauf der Fräsbearbeitung auf der Basis der IPWs in Finite-Elemente-Simulationen (FE) zu bestimmen. Für FE-Simulationen werden jedoch genau solche dreidimensionalen Volumenkörpermodelle benötigt. Die Forscherinnen und Forscher erweiterten deshalb die Multi-Dexel-Modellierung und programmierten neue Funktionalitäten (Bild 1).
Simulation der veränderlichen, dynamischen Werkstückeigenschaften
Durch den kontinuierlichen Materialabtrag bei der Fräsbearbeitung ändert sich die Geometrie des Werkstücks fortlaufend. Da das Werkzeug die Blisk-Schaufeln während des Fräsens bahnweise umfährt, ändert sich zudem ständig der Kraftangriffspunkt am Bauteil. Um diese Dynamik zu erfassen, simulierten die Forscherinnen und Forscher den Fräsprozess anhand einer FE-Simulation.
Während der virtuellen Fertigung hielten die Forscherinnen und Forscher den Prozess an verschiedenen Werkzeugpositionen an, erhoben Daten und stellten Berechnungen an. Mit den Ergebnissen erzeugten sie Zwischengeometrien des Werkstücks und ermittelten das Eingriffsverhältnis von Werkzeug und Werkstück an den ausgewählten Punkten. Auf diese Weise entstand ein automatisierter Workflow, mit dem sich die veränderlichen, dynamischen Werkstückeigenschaften an den ausgewählten Werkzeugpositionen bestimmen liessen (Bild 2). Die Modellierung macht sichtbar, dass, je nach Kraftangriffspunkt, unterschiedliche Schwingformen angeregt werden. Zerspant das Fräswerkzeug beispielsweise an der Vorderkante der Schaufel, kann eine sogenannte Torsionsmode auftreten (Bild 2, links unten). Dies geschieht jedoch nicht, wenn sich das Werkzeug in der Mitte der Schaufelfläche (CL2 oder CL5) befindet. Ausserdem verändern sich durch den kontinuierlichen Materialabtrag die Resonanzfrequenzen, und mit fortschreitendem Umfahren des Werkzeugs von der Schaufelspitze zum Schaufelfuss reduziert sich die Steifigkeit, da die Auskraglänge der Schaufel an der Werkzeugposition abnimmt.
Die Prozessparameter zu den jeweiligen Werkzeugpositionen visualierten die Forscherinnen und Forscher in einem sogenannten Linear-Parameter-Varying-Modell, kurz LPV-Modell. Das LPV-Modell bietet eine übersichtliche und effiziente Darstellung der Werkstückdynamik, basierend auf den simulierten modalen Parametern. Zusätzlich ermöglicht das LPV-Modell auch Interpolationen zwischen den simulierten dynamischen Zuständen. Dank dieser Interpolationen konnte die benötigte Anzahl der virtuell gemessenen Werkzeugpositionen reduziert werden.
Um das dynamische Verhalten des Fräswerkzeugs abzubilden, das ebenfalls die Stabilität des Fräsprozesses beeinflusst, ermittelte das Projektteam diese Dynamiken anhand experimenteller Modalanalysen und überführte die Messdaten anschliessend in ein mathematisches Modell.
Kopplung der FE-Modalanalyse mit der Kraftberechnung
Neben der veränderlichen Dynamik ist die Zerspankraft eine entscheidende Grösse für die dynamische Prozessstabilität der Fräsbearbeitung. Deshalb ermittelte das Projektteam des Fraunhofer IPT auf Basis der Multi-Dexel-Modellierung das Eingriffsverhältnis von Werkzeug und Werkstück. Unter Berücksichtigung sogenannter spezifischer Schnittkraftkoeffizienten simulierten die Forscherinnen und Forscher die Zerspankraft für jede Werkzeugposition.
Die Berechnungen zur Werkstückdynamik und die Kraftberechnungen führte das Projektteam im nächsten Schritt zusammen und verrechnete die ermittelten Werte. Durch diese Kopplung entstand ein Vorhersagemodell für Schwingungen während des 5-Achs-Fräsprozesses. Dieses umfasst die Simulation der Zerspankraft und die Systemdynamik, bestehend aus der simulierten Werkstückdynamik und des experimentell ermittelten Werkzeugmodells. Darüber hinaus wird der Einfluss der Schwingungen auf die Zerspankraft durch eine Rückkopplung innerhalb des Modells – der sogenannte Regenerativeffekt – abgebildet.
Ermittlung vorteilhafter Spindeldrehfrequenzen
Mit dem neuen Vorhersagemodell lassen sich Bauteilschwingungen während des Fräsprozesses für beliebige Werkzeugpositionen simulieren. Allerdings hängen die simulierten Schwingungen von den gewählten Spindeldrehfrequenzen ab, denn je nach Drehfrequenz verursacht das Werkzeug unterschiedliche Schwingungen und Instabilitäten. Um nun die vorteilhaftesten Frequenzen für jede Werkzeugposition zu ermitteln, koppelten die Forscherinnen und Forscher die Werte aus der Schwingungsvorhersage – hier spricht man von Root-Mean-Square-Werten (RMS) – mit verschiedenen Spindeldrehfrequenzen für jede Werkzeugposition und visualisierten dies in Stabilitätsdiagrammen (Bild 3). Die Analyse der Stabilitätsdiagramme zeigt, dass sich die vorhergesagten Schwingungsamplituden im Laufe des Fräsprozesses stark verändern, sich aber auch abhängig von der Werkzeugposition verhalten.
Ergebnisse der Schwingungssimulation im Praxistest bestätigt
Aus den gewonnenen Erkenntnissen leiteten die Forscherinnen und Forscher neue Prozessstrategien für die Fräsbearbeitung ab, bei denen die Spindeldrehzahl während der Fertigung kontinuierlich und abhängig von der Werkzeugposition angepasst wird, um die Bauteilschwingungen zu minimieren. In zahlreichen Zerspanuntersuchungen validierten sie schliesslich die neuen Prozessstrategien und erzielten eine hohe Übereinstimmung zwischen vorhergesagten und tatsächlich gemessenen Schwingungen (Bild 4). Anwendung des digitalen Zwillings auch zur Schwingungsvorhersage beim Drehen und bei der Nachbearbeitung additiv gefertigter Bauteile.
Die neue «PhysiX-CAM»-Technologie, also der digitale Zwilling zur Schwingungsvorhersage, soll nach den erfolgreichen Versuchen zukünftig auch auf andere Fertigungsverfahren wie das Drehen übertragen werden. Das Team des Fraunhofer IPT plant darüber hinaus, die Erfahrungen aus dem Forschungsprojekt auch für Verbesserungen bei der Nachbearbeitung additiv gefertigter Bauteile einzusetzen. Das Forschungsprojekt «PhysiX-CAM» wurde durch Mittel des Europäischen Fonds für regionale Entwicklung (EFRE) 2014-2020 gefördert.
Das Fraunhofer-Institut für Produktionstechnologie IPT erarbeitet Systemlösungen für die vernetzte, adaptive Produktion nachhaltiger und ressourcenschonender Produkte sowie der zugehörigen Dienstleistungen. Die Schwerpunkte liegen in den Bereichen Prozesstechnologie, Produktionsmaschinen, Produktionsqualität und Messtechnik sowie Technologiemanagement und reichen von den Grundlagen bis zur digitalen Transformation der Produktion. Wir entwickeln und optimieren neue und bestehende Methoden, Technologien und Prozesse für die Produktion der Zukunft. Dabei begreifen wir die Produktion nicht nur in ihren einzelnen Schritten, sondern in der Gesamtheit aller Prozesse und Verbindungen zwischen den Gliedern der Prozesskette. Auf diese Weise entwickeln wir im Auftrag unserer Kunden sowohl hoch spezialisierte Einzeltechnologien als auch vollständige Systemlösungen für die Produktion.
INFOS | KONTAKT
Fraunhofer-Institut für Produktionstechnologie IPT
Steinbachstrasse 17
D-52074 Aachen
T +49 (0)241 8904-0
www.ipt.fraunhofer.de
Branchentreffpunkt für Medizintechnikunternehmen
9. und 10. September
www.medtech-expo.ch
Die Fachmesse für Industrieautomation
10. und 11. September
www.automation-wetzlar.de
Weltleitmesse für Fügen, Trennen, Beschichten
15. bis 19. September
www.schweissen-schneiden.com