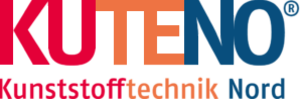
KUTENO, Rheda-Wiedenbrück
Kunststofftechnik Nord
14. bis 16. Mai
www.kuteno.de
Bilder: Clariant
Der füllmedienfreie Massedrucksensor IMPACT IE/PL’c‘ von Gefran für Hochtemperaturanwendungen ist robust und schaltet bei Überdruck die überwachte Anlage selbsttätig ab. Damit erfüllt er die Extrudernorm EN 1114-1 und ist ideal geeignet für die Überdruckabsicherung von Kunststoffextrudern nach Performance Level ’c‘. Diese Vorteile weiss auch Clariant Masterbatches zu schätzen und schrieb den Sensor daher in das Lastenheft für Doppelschneckenextruder zur Herstellung von Farb- und Additivkonzentraten für die Kunststoffindustrie.
Produkte aus Kunststoff bestimmen unseren Alltag – ob funktionelle Industriekomponenten, Verpackungslösungen, ansprechende Designobjekte, Haushaltsgeräte, Textilien oder buntes Spielzeug. Für die unendliche Farbvielfalt und die gewünschten Produkteigenschaften sorgen Farb- und Additivkonzentrate, die dem Grundkunststoff beigemischt werden. Ein weltweit führender Hersteller dieser Konzentrate ist Clariant Masterbatches, eine von sieben Geschäftseinheiten der Clariant International AG mit Sitz in der Schweiz.
Zu den Produkten der Geschäftseinheit zählen Masterbatches für Polyolefin-Polymere, technische High-Performance-Kunststoffe und die Medizinindustrie sowie Mehrzweck-Farbkonzentrate. Die Produkte sind in hunderten von Standardfarben sowie als massgeschneiderte Formulierungen und als Farb-/Additiv-Masterbatches erhältlich.
Zur Produktion der Farb- und Additivkonzentrate setzt Clariant gleichläufige, parallele und dichtkämmende, also ineinandergreifende Doppelschneckenextruder ein. Allein in den beiden deutschen Masterbatch-Werken sind 50 dieser Anlagen im Einsatz. Alle Extruder sind zur Überprüfung des Schmelzedrucks mit Massedrucksensoren am Extruderkopf ausgerüstet. Das ist wichtig, denn Extruder pressen den flüssigen Kunststoff mit hohem Druck und hoher Temperatur durch die Düse am Kopfende. Dabei bauen die Doppelschneckenextruder, die bei Clariant im Einsatz sind einen Druck von bis zu 200 bar auf. Andere Extruder kommen auf Drücke von 1000 bar. Ist der Extruderkopf blockiert, entsteht ein Überdruck. Bleibt dieser unbemerkt, kann es zur Beschädigung von Maschinenteilen und Herausspritzen von heissem Kunststoff kommen. «Um unserem Team diese Gefahr anschaulich zu demonstrieren, haben wir einmal den Sensor eines Laborextruders überbrückt und gleichzeitig den Kopf verstopft – mit bleibendem Eindruck», erinnert sich Thilo Kind, Leiter Prozesstechnologie bei Clariant Masterbatches.
Überdruckabsicherung und Schutz vor Zerstörung
Die Aufgabe des Massedrucksensors besteht also darin, den Extruder bei Erreichen eines kritischen Drucks abzuschalten. Früher nutzte Clariant Massedruckmessumformer mit dem Füllmedium NaK oder Quecksilber. Doch diese füllmedienhaltigen Druckfühler mit ihren vergleichsweise dünnen Messmembranen können leicht zerstört werden – und zwar unbemerkt. So kann beispielsweise die beim Erkalten schrumpfende Kunststoffmasse die Sensormembran zerreissen. Problematisch dabei: werden die Massedrucksensoren auf diese Weise zerstört, kann es geschehen, dass der zuletzt gemessen Druckwert ohne Fehlermeldung eingefroren wird. Passiert dies während des Betriebs und baut sich dadurch unbemerkt ein Überdruck auf, kann dies zu einem Aufplatzen am Extruderkopf führen.
Auch eine unvorsichtige, unvorschriftsmässige Reinigung der Sensoren beschädigt die vergleichsweise dünne Messmembran schnell und verhindert damit den sicheren Schutz vor Überdruck. Nur erfahrene, gut trainierte Mitarbeiter schaffen es, den Sensorkopf zu reinigen, ohne seine Funktion dabei zu beeinträchtigen.
Um die Gefahr einer Explosion auszuschliessen, wurde die EU-Sicherheitsrichtlinie 2014 dahingehend geändert, dass statt einem herkömmlichen wahlweise zwei redundante Sensoren oder ein selbstüberwachender Sensor eingesetzt werden müssen.
Clariant Masterbatch entschied sich für selbstüberwachende Sensoren und schrieb den füllmedienfreien IMPACT-Massedruckmessumformer von Gefran in sein Lastenheft für Extruderlieferanten. «Zwei redundante Sensoren pro Extruder bedeutet, die doppelte Menge an Sensoren anzuschaffen. Abgesehen davon bestünde dann immer noch das Risiko der Zerstörung. Da ist der robuste, langlebige IMPACT die bessere Wahl. Zu diesem Sensor gibt es aktuell keine wirkliche Alternative auf dem Markt», erklärt Thilo Kind. Daher ist seit 2014 jeder neue Doppelschneckenextruder von Clariant Masterbatches mit einem Massedruckmessumformer vom Typ IMPACT (Innovative Melt Pressure Accurate Transductor) aus der Serie IE/PL’c‘ von Sensormate ausgerüstet. Maschinen, deren herkömmliche füllmedienhaltige Sensoren defekt sind, werden mit den diesen füllmedienfreien Schmelzedrucksensor nachgerüstet. Denn dieser erkennt einen Defekt eigenständig und schaltet den Extruder sicher ab beziehungsweise verhindert das Anfahren. Darüber hinaus liefern die Massedrucksensoren wichtige Informationen zur Einstellung der Maschinenlinie: so wird über den Druck die Geometrie und damit die Qualität des Granulats gesteuert. Der Druck im Extruderkopf muss also jederzeit in einem bestimmten Druckbereich liegen, damit das Granulat mit der korrekten (qualitätsentscheidenden) Geometrie aus dem Extruderkopf kommt. Die eingesetzten Sensoren dienen damit auch der Sicherung der Produktqualität.
Füllmedienfreier Massedrucksensor für Hochtemperaturanwendungen
Die Massedrucksensoren der IMPACT-Serie nutzen den piezoelektrischen Effekt und eignen sich für Hochtemperaturanwendungen (350 °C). Ihr wichtigstes Merkmal ist das Fehlen einer Übertragungsflüssigkeit. Der Druck des Messstoffs wird über eine Membrane grosser Dicke direkt an das Sensorelement aus Silizium übertragen. Die Umwandlung der Belastung erfolgt durch eine mikro-bearbeitete Struktur aus Silizium (MEMS). Das Sensorelement benötigt nur eine minimale Durchbiegung von 11 bis 14 µm. Entsprechend robust kann die Mechanik gewählt werden: Die Druckübertragung übernimmt ein Stössel mit 5 mm Länge. Die messstoffberührte Membran aus Edelstahl besitzt je nach Druckbereich eine Stärke von bis zu 1,5 mm und ist somit bis zu 15 Mal dicker als die Membranen herkömmlicher Schmelzedrucksensoren. Dieser starken Membran können auch anhaftende erkaltende Kunststoffe nichts anhaben. Damit ist der Sensor besonders langlebig. Zudem zeichnet er sich durch eine kurze Ansprechzeit aus.
Hohe Membrandicke ist entscheidender Vorteil der Sensortechnik
Der Vorteil der robusten Membran, die mit einem speziellen Verschleissschutz beschichtet ist, zeigt sich auch bei der Reinigung der Extruder vor jeder Charge. Da von den Konzentraten jeweils nur vergleichsweise geringe Mengen – zirka 100 bis 1000 kg pro Charge – produziert werden, müssen die Extruder entsprechend häufig gesäubert werden. Ein Problem für die dünne Membran füllmedienhaltiger Sensoren, die nicht nur durch anhaftende, erkaltende Kunststoffschmelze, sondern auch durch eine zu raue Behandlung schnell reisst. «Bei uns sind nur noch vereinzelt Extruder mit füllmedienhaltigen Massedrucksensoren im Einsatz. Und zwar nur noch dort, wo die Mitarbeiter sehr gut geschult sind und bei der Reinigung entsprechend pfleglich mit den Sensoren umgehen», erklärt Thilo Kind. Die IMPACT-Sensoren sind dank ihrer Stahlmembran nicht so empfindlich und verzeihen auch mal einen gröberen Reinigungsvorgang.
Clariant verwendet je nach Extrudersteuerung verschieden Sensorausführungen: zur Nachrüstung älterer Maschinen kommt üblicherweise eine IMPACT-Variante zum Einsatz, die sich über einen Magnetstift kalibrieren lässt. In neuen Maschinen ist dagegen die Version verbaut, bei der ein elektrischer Impuls über den Stecker zur Nullstellung genutzt wird. «Wir können auch ältere Maschinen mit einem elektrisch kalibrierbaren Massedrucksensor ausrüsten. Das erfordert lediglich die Anpassung der Steuerung, was unkompliziert und schnell erledigt ist», erläutert Thilo Kind.
INFOS | KONTAKT
Sensormate AG
Steigweg 8
CH-8355 Aadorf
T +41 (0)52 523 25 00
www.gefran.ch
office@gefran.ch
Internationale Fachmesse für optische Technologien, Komponenten und Systeme
14. bis 16. Mai
www.optatec-messe.de
Internationale Ausstellung und Konferenz für Spulentwicklung, Isolierung und Elektrofertigung
14. bis 16. Mai
www.coilwindingexpo.com
Fachmesse für Industrieautomation
15. und 16. Mai
www.automation-heilbronn.com