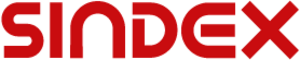
Sindex, Bern
Treffpunkt der Schweizer Technologiebranche
2. bis 4. September
www.sindex.ch
Die additive Fertigung insbesondere von metallischen Bauteilen bietet ein relevantes Potenzial für viele Wirtschaftszweige mit diversen Anwendungen in vielen Branchen. Um diese Potenziale für innovative Produkte nutzen zu können, müssen die Prozessketten und die Produktion vereinfacht und kostenseitig optimiert werden. Dabei ist insbesondere die Nachbearbeitung von additiv gefertigten Bauteilen oft komplex, kostenintensiv und zeit-aufwendig. Wie können die Nachbearbeitungsprozesse optimiert werden?
Heute hat die Nachbearbeitung im Schnitt mehr als 25 Prozent Kostenanteil in der gesamten Wertschöpfungskette der additiven Fertigung. Insbesondere bei dem meist verbreitesten additiven Fertigungsverfahrens, dem Laserstrahlschmelzen im Pulverbett, PBF-LB/M (>70 Prozent aller additiven Fertigungen metallischer Bauteile) stellt sich die notwendige Nachbearbeitung als aufwendig und schwierig und damit teuer dar, wenn nicht schon in der Entwicklungsphase die Nachbearbeitung berücksichtigt wird. Bild 1, verdeutlicht die «Kostenbeeinflussung – Kostenentstehung» in der Prozesskette additiver Fertigungsverfahren.
Nachbearbeitung
Die Nachbehandlungsprozesse beim PBF-LB/M (Bild 2) sind, die Bauteile vom Pulver zu befreien beziehungsweise zu reinigen, eine etwaige Wärmebehandlung zum Beispiel zur Spannungsreduktion, die Bauteile von der Bauplatte abtrennen (Drahterodieren oder Sägen), – ganz wichtig – die Supportstrukturen zu entfernen und anschliessend die Funktionsflächen meist spanend nachzubearbeiten.
Insbesondere notwendige Supportstrukturen sind sehr aufwendig, meist händisch und somit teuer zu entfernen. Deshalb, wie bereits oben erwähnt, sollten die Bauteile additiv fertigungsgerecht konstruiert werden, damit – wenn möglich – die Supportstrukturen reduziert oder sogar ganz unnötig werden.
In Bild 3 sind zwei auf Leichtgewicht und Festigkeit optimierte Hebel identischer Funktion dargestellt. Auf der linken Seite ist das theoretisch optimale Bauteil ohne additiv gerechte Konstruktionsausführung dargestellt. Würde das Bauteil so gedruckt, würden sehr viel Stützen notwendig sein und die Nachbearbeitung würde sogar noch deutlich teurer als 25 Prozent der gesamten Fertigungskosten. Werden die Konstruktionsrichtlinien für die additiven Fertigung (Design for Additive Manufacturing, DfAM) und eine verbesserte Ausrichtung beachtet, kann auf die Supportstrukturen nahezu ganz verzichtet werden. Die notwendigen Nachbearbeitungsschritte reduzieren sich auf das sehr vereinfachte Abtrennen des Bauteils von der Bauplattform, dem Sandstrahlen und Aufbohren der Montagebohrungen. Leider sind nicht alle Bauteile zur additiven Fertigung derart optimal gestaltet.
Müssen die Bauteile nach der additiven Fertigung aufwendig spanend zum Beispiel auf einem Bearbeitungszentrum bearbeitet werden, müssen die Bauteile gespannt werden. Ähnlich wie bei Gusskonstruktion bietet sich die Integration der Spannflächen im Bauteil selbst an (Bild 4 A) oder dass auf die Kontur des Bauteils angepasste Spannbacken gefertigt werden (Bild 4 B). Eine andere Möglichkeit besteht darin, die Bauplatte mit dem Werkstück in einem Nullpunkt-Spannsystem (Aufnahme und Spannung über Stifte, pneumatisch oder hydraulisch) aufzunehmen, um ohne Umspannfehler im Bearbeitungszentrum aufgenommen werden zu können (Bild 4 C bis E).
In einem gemeinsamen von der Innosuisse geförderten Innovationsprojekt wurden unter Führung von Inspire zusammen mit den Firmen Gressel, AM Kyburz, der ZHAW und der ETHZ-Spannsysteme für eine automatisierte und wirtschaftliche verbesserte Nacharbeit in der additiven Fertigung entwickelt. Das Ergebnis waren zwei Konzepte für eine universelle und standardisierte Schnittstellen zwischen Spannsystem und AM-Bauteil, die sogenannte Bolzenspannlösung (Bild 5 A) und die so genannte Blechspannlösung (Bild 5 B).
Beim Bolzen-Spannsystem (Bolt-it Systeme) werden drei Bolzen am Werkstück additiv mit aufgebaut. Über die drei Bolzen kann das Werkstück in einer Spezialaufnahme gespannt und optimal nachbearbeitet werden. Die Bolzen verfügen über Sollbruchstellen und können einfach händisch abgebrochen werden (Bild 5 A von links nach rechts). Beim Blechspannsystem werden Kleinteile, wie zum Beispiel Gebissbrücken in der Dentaltechnik direkt auf dünne Bleche additiv auf-gebaut. In einer Spezialaufnahme können die Bleche in einem Be-arbeitungszentrum für die Nachbearbeitung aufgenommen werden (Bild 5 B von links nach rechts).
Eine weitere Herausforderung ist die Behandlung der additiv hergestellten Oberflächen. Die Oberflächenrauigkeit der im Laserschmelzverfahren hergestellten Bauteile ist selten besser als Ra = 10 µm. Meist ist sie schlechter, was für viele Anwendungen unzureichend ist und zu einer subtraktiven Nachbearbeitung führt.
Für geometrische Freiflächen werden standardmässig konventionelle Strahlverfahren (Sand, Glas, Korund …) mit guten Ergebnissen eingesetzt (Bild 6 A). Durch Fliehkraftschleifen konnte die Oberflächenrauheit additiv gefertigter medizinischer Instrumente auf bis zu Ra = 0,16 µm (Rz = 1,5 µm) nach 4 Stunden verbessert werden (Bild 6 B). Durch Elektropolieren an additiv gefertigten Implantaten in Titan (Bild 6C, DryLyte™ dry electropolishing) konnte die Oberflächenrauheit nach 20 Stunden auf Ra = 1 µm (nach 70 h auf Ra = 0,8 µm) gesteigert werden (Bild 6 C). Auch das neu entwickelte sogenannte Hirtisieren der Fa. Rena kommt auf ähnliche Er-gebnisse.
Fazit
Die Prozesse der Nachbearbeitung bei der additiven Fertigung sind heute mehr denn je im Fokus der Optimierung der gesamten Wertschöpfungskette der additiven Fertigung metallischer Bauteile. Es wurde gezeigt, dass schon im Konstruktionsstadium unter Verwendung der Regeln des «Design for Additive Manufacturing» unnötige Supportstrukturen und aufwendige Abtrennprozesse reduziert beziehungsweise eingespart werden können. Für die spanende Nachbearbeitung in Bearbeitungszentren komplexer additiv gefertigter Bauteile sind integrierte Lösungen zum optimalen Spannen der Werkstücke auch unter automatisierter und wirtschaftlicher Perspektive entwickelt worden. Des Weiteren wurde gezeigt, dass die Oberflächenrauheit insbesondere von Freiflächen mit Strahlen, Fliehkraftschleifen und Elektropolieren stark verbessert werden kann.
INFOS | KONTAKT
ZHAW School of Engineering
Zentrum für Produkt- und Prozessentwicklung
Lagerplatz 22
CH-8400 Winterthur
T +41 (0)58 934 76 93
www.zhaw.ch
info.zpp@zhaw.ch
Zu den Autoren
Andreas Kirchheim,
Stefan Czerner, stefan.czerner@zhaw.ch
Advanced Production Technologies, Additive Manufacturing
Zentrum für Prozess- und Produktentwicklung ZPP
Zürcher Hochschule für Angewandte Wissenschaften ZHAWZ
Branchentreffpunkt für Medizintechnikunternehmen
9. und 10. September
www.medtech-expo.ch
Die Fachmesse für Industrieautomation
10. und 11. September
www.automation-wetzlar.de
Weltleitmesse für Fügen, Trennen, Beschichten
15. bis 19. September
www.schweissen-schneiden.com