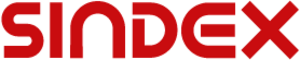
Sindex, Bern
Treffpunkt der Schweizer Technologiebranche
2. bis 4. September
www.sindex.ch
Das Schleifen ist bei der Fertigung hochwertiger Produkte oft einer der letzten, wenn nicht der letzte Bearbeitungsschritt. Da eine fehlerhafte Schleifbearbeitung zu hohen finanziellen Verlusten führen kann, werden Schleifvorgänge meist von erfahrenden Maschinenbedienern durchgeführt.
Die Schleifparameter werden in vielen Fällen entweder durch die Erfahrung der Maschinenbediener oder im Trial-and-Error-Verfahren ermittelt und entsprechen oft nicht den optimalen Bearbeitungsparametern. Hinzu kommt die Auswahl der Schleifscheiben, der Abrichtwerkzeuge und der geeigneten Abricht – und Schleifparameter, die auch wesentlich zu einem optimalen Schleifergebnis beitragen. Maschinenbediener ohne ausreichende Erfahrung auf dem Gebiet der Schleiftechnologie sind hier im Regelfall überfordert und halten an Schleifscheiben, Schleifparametern, Abrichtwerkzeugen und Abrichtmethoden fest, die «schon immer» zur Herstellung ähnlicher Werkstücke verwendet oder von den Werkzeugherstellern angeboten wurden. Auch die Beurteilung von Schleiffehlern auf den Werkstücken stellt für die meisten Maschinenbediener eine Herausforderung dar.
Am KSF wurde ein Expertensystem für Schleifprozesse (Grinding-Expert) entwickelt, das optimale Unterstützung zur Konzeption und Durchführung von effizienten Schleifprozessen durch die Auswahl geeigneter Abricht- und Schleifwerkzeuge und Abricht- und Schleifparameter bietet. Weiterhin ist ein Troubleshooting-Modul zur Fehlerbehebung bei fehlerhaften Schleifprozessen integriert. In dieser Veröffentlichung werden die einzelnen Module des Expertensystems für Schleifprozesse beschrieben.
Zielsetzung
Das Schleifen ist eine Schlüsseltechnologie und eines der wichtigsten Fertigungsverfahren für die Bearbeitung von Bauteilen mit hohen Anforderungen an die Mass- und Formgenauigkeit und die Oberflächenqualität. Des Weiteren kann ein sehr breites Werkstückspektrum durch Schleifen bearbeitet werden. Die stetig steigenden Qualitätsanforderungen, die allgemeine technische Fortentwicklung und gleichzeitig der Druck auf die Produktkosten im internationalen Wettbewerb führen zu einer erhöhten Bedeutung des Schleifprozesses in der Fertigung und einer höheren Priorität der Schleifprozessoptimierung [1]. Das Schleifen wird nicht zu Unrecht als eines der komplexesten Fertigungsverfahren beschrieben, da es zahlreiche Prozesseingangsparameter und Prozesskenngrössen besitzt, die das zu erwartende Prozessergebnis massgeblich bestimmen.
Das notwendige fertigungstechnische Fachwissen zur optimalen Auswahl der entsprechenden Prozesseingangsparameter ist beim Bedienpersonal oft nicht in der notwendigen Tiefe vorhanden. Diese Problemstellung wird durch den Mangel an Fachkräften für Fertigung von Spezialkomponenten und -instrumenten noch verschärft. Der stark erhöhte Aufwand bei der Anpassung und Optimierung der Fertigung sowie drohende Fehlproduktion/Ausschuss bei hochwertigen und teuren Produkten bergen erhebliche Kostenrisiken.
Um auf Anhieb optimale Ergebnisse zu erhalten, wurde das Expertensystem für Schleifprozesse entwickelt. Es besteht aus einer Kombination von Datenbanken (Materialdaten, Maschinendaten, Schleif- und Abrichtwerkzeugdaten sowie Parameter zur Ermittlung von Vorschlagdaten) und einem formelbasierten Regelwerk und stellt sicher, dass effiziente Schleifprozesse mit optimalen Ergebnissen durchgeführt werden können. Nach der Eingabe der bekannten Parameter (wie Werkstückmaterial, Soll-Oberflächengüte …) können über das Expertensystem geeignete Schleifscheiben, Abrichtparameter (inkl. Abrichtwerkzeuge) und Schleifparameter ermittelt werden. Als weiterer Schritt wird die Optimierung per KI implementiert.
Das Expertensystem
Das Schleifprozess-Expertensystem ist ein webbasiertes System, das in einer Kombination von Django, Python und Ajax und einer MySQL-Datenbank besteht. Per Web-Anwendung werden die Anfragen über HTTP-Requests an das Django Framework gesendet, dort erfolgt die Verarbeitung bezüglich Regelwerk und auf den Eingabedaten der User-basierten Abfragen einer MySQL-Datenbank. Die entsprechend ermittelten Daten werden gegebenfalls in Django weiterverarbeitet und anschliessend per HRRP-Response in der Web-Anwendung angezeigt. Das Startfenster des Expertensystems besteht aus drei Bereichen: Schleifscheiben-Auswahl, Abrichten und Schleifen. Die Schleifscheibenauswahl verbirgt sich hinter dem entsprechenden Button. Abrichten, das heisst Auswahl des Abrichtverfahrens und die Bestimmung prozessspezifischer Abrichtparameter werden über «Abrichten» aufgerufen und hinter dem Button «Schleifen» werden nach der Auswahl des gewünschten Schleifprozesses prozessbasierte Vorschläge geliefert, vorhandene Prozesse bewertet und in einem Troubleshooting-Modul auch Hilfestellung zu Schleifproblemen angeboten. Im Folgenden werden die einzelnen Operationen detaillierter beschrieben.
Schleifscheibenauswahl
Nach der Eingabe/Auswahl der Parameter für den Schleifscheibentyp (Schleifprozess, Abtragsrate, Material und Härte, zu erzielende Werkstückrauheit und KSS) erfolgt ein Vorschlag für prozessgeeignete Schleifscheiben (Korn, Körnung, Härte, Gefüge und Porosität (Bild 1).
Im gezeigten Beispiel wurde eine konventionelle Schleifscheibe mit keramischer Bindung, als Schleifprozess das Aussenrund Längsschleifen mit Abtragsrate Normalschleifen, als Material Stahl 100Cr6 beziehungsweise 1.3505 mit einer Härte von 57 bis 60 HRc bei einer gewünschten Zielrauheit von Ra zwischen 0,1 und 0,2 beziehungsweise Rz zwischen 0,6 und 1,25 und als KSS-Emulsion mit bis zu 2,5 Prozent Mineralölanteil ausgewählt.
Das System schlägt folgende Schleifwerkzeuge für die genannten Parameter vor: Als Schleifmittel kommen unterschiedliche Korundsorten und sogar eine Mischung verschiedener Sorten in Frage, nämlich: Edelkorund weiss (EKw), Spezialkorund, Edelkorund rosa (EKr), EKw/EKrubin, Sinterkorund/EKw, Sinterkorund, EKr, Sinterkorund / Einkristallkorund (EKk), Sinterkorund/EkK/EKw und Kornmischungen davon. Der Anwender kann die Auswahl anhand der Darstellung der Härte und Sprödigkeit konventioneller Schleifmittel, die in der Mitte der Abbildung zu finden ist, an seinen Prozess anpassen. Als Körnung wird 150 bis 280# vorgeschlagen (da die erreichbare Oberflächenrauheit und Profilhaltigkeit der Schleifscheibe neben der Körnung auch von weiteren Einflussgrössen, wie Schleif- und Abrichtparametern abhängt), die Härte I bis J und das Gefüge 7 bis 8 empfohlen. Als Vorschlag für eine künstliche Porosität wird als Porenbildner A1 mit einem Anteil von 1,5 Prozent und einer Grösse von 0,5 mm angezeigt.
Vorschläge für superabrasive Schleifscheiben (D und B) sind ebenfalls im System hinterlegt.
Abrichten
Im Bereich Abrichten werden zunächst Empfehlungen für keramisch gebundene konventionelle und superharte (das heisst Diamant (D) und cBN (B)) Schleifscheiben (zukünftig auch Abrichten und Schärfen für kunstharz- und metallgebundene D- und B-Schleifscheiben) bezüglich stehender und rotierender Abrichter gegeben. Nach deren Auswahl (Abrichtertyp kann auch selbst ausgewählt werden) erfolgt die Eingabe der Abrichtparameter, Schleifscheibenspezifikation und Prozessbedingungen (Abtragsrate, Schleifscheibengeschwindigkeit und einiger abrichterspezifischer Eingaben). Aus diesen ermittelt das System geeignete Abrichtparameter (Bild 2).
Im Beispiel wurde für den stehenden Abrichter (links) eine Abrichtfliese ausgewählt, als Schleifmittel Korund + Edelkorund, die Abtragsrate Normalschleifen, ein Schleifscheibendurchmesser von 400 mm, eine Schleifscheibenkörnung von 120#, eine Umfangsgeschwindigkeit von 30 m/s und eine Wirkbreite des Abrichters von 0,8 mm. Die gewählten Parameter führen zu einem Vorschlag von einem Abrichtüberdeckungsgrad zwischen 2,5 und 4 (als Startpunkt wurde Ud = 3,3 vorgeschlagen), einer Abrichtzustellung von 8 µm und einer axialen Abrichtvorschubgeschwindigkeit von 312 mm/min. Im Beispiel der Formrolle (rechts) bei zusätzlichen Inputparametern von 30 mm Schleifscheibenbreite und 100 mm Rollendurchmesser werden als Geschwindigkeitsverhältnis +0,5, ein Abrichtüberdeckungsgrad von 3,3, eine Abrichtzustellung von 8 µm, eine axiale Vorschubgeschwindigkeit von 312 mm/min bei einer Drehzahl der Rolle von 2865 min-1 vorgeschlagen.
Die Auswahl der Abrichtart ist abhängig von den Schleifscheibentypen. So werden für Korund + Edelkorund, Sinterkorund und Siliciumcarbid-Schleifscheiben, stehende und rotierende Abrichter vorgeschlagen, bei Diamant und cBN nur rotierende Abrichter empfohlen (für stehende Abrichter nicht geeignet).
Der unter den Abrichtempfehlungsparametern dargestellte Balken gibt den Status der Wirkrautiefe der Schleifscheibe bei den empfohlenen Abrichtparametern, beziehungsweise ob die Scheibe eher stumpf oder schleiffreudig abgerichtet wird, an. Somit wird auch die Schulung interessierter Mitarbeiter ermöglicht (Zusammenhänge zwischen Eingangsparametern, vorgeschlagenen Abrichtparameter und etwaigen Wirkrautiefen der Schleifscheibe können sehr einfach ermittelt werden).
Wird mit der Maus auf die neben den Parametern dargestellten Fragezeichen gezeigt, werden Erläuterungen zu den entsprechenden Parametern angezeigt.
Schleifen
Der Bereich Schleifen gliedert sich nach der Auswahl des betreffenden Schleifprozesses in vier Auswahloptionen (Bild 3). Aktuell werden die Prozesse Aussenrund-, Innenrund-, Flach- und Spitzenlosschleifen abgedeckt, in naher Zukunft werden auch das Koordinaten- und das Werkzeugschleifen hinzukommen.
Über die erste Option «Prozessparameter/Vorschlag» kann, nach Eingabe der Prozessparameter, wie Abtragsrate, Schleifscheibenbreite, Schleifscheibendurchmesser und Werkstückabmessungen eine Empfehlung für die Schleifparameter angezeigt werden (Bild 4).
Im Beispiel wurde für ein Aussenrundlängsschleifprozess weicher Stahl und als Schleifmittel Korund + Edelkorund bei einer Abtragsrate Normalschleifen gewählt. Der gewählte Schleifscheibendurchmesser beträgt 400 mm und die breite 30 mm, die Schleifscheibenkörnung 150#, die Umfangsgeschwindigkeit 30 m/s (das Programm empfiehlt die höchste Schnittgeschwindigkeit, die die Maschine ermöglicht und für die die Scheibe zugelassen ist, auszuwählen) und der Werkstückdurchmesser wurde mit 50 mm angegeben. Bei diesen Eingangsparametern werden als Schleifempfehlung ein Geschwindigkeitsverhältnis von 70, ein Schleifüberdeckungsgrad von 3,5, eine Zustellung von 12 µm, eine Werkstückdrehzahl von 164 min-1 und eine axiale Vorschubgeschwindigkeit von 1406 mm/min vorgeschlagen. Der Anwender benötigt in der Regel nur die Zustellung, die Werkstückdrehzahl und die axiale Vorschubgeschwindigkeit, um die Schleifmaschine zu programmieren beziehungsweise manuell zu bedienen. Weiterhin werden Informationen über die bei diesen Parametern zu erwartende Abtragsrate (hier 5,15 mm3/mm.s) und die Breite der Schrupp- und Ausfunkzone der Schleifscheibe (hier 8,57 beziehungsweise 21,43 mm) angezeigt.
Die neben den Parametern angezeigten [i] und [?]-Buttons geben Hinweise zu der Höhe der betroffenen Parameter an beziehungsweise erklären diese.
Die Option «Prozessbeurteilung» führt zu Hinweisen bezüglich der Parameter eines über den Bediener eingegebenen (bestehenden) Prozess (Bild 5 oben) und gegebenenfalls Hinweise zu ungeeigneten Schleifparametern (unten). Wichtige Hinweise werden mit einem roten x gekennzeichnet.
Im Beispiel führten für einen Aussenrundlängsschleifprozess die Eingangsparameter Schleifscheibe mit Ø 400 mm, 30 mm Breite, 150# Schleifscheibenkörnung, Umfangsgeschwindigkeit von 30 m/s, einem Werkstückdurchmesser von 30, einer Werkstückdrehzahl von 95 min-1, eine axiale Vorschubgeschwindigkeit von 500 mm/min und eine Zustellung von 5 µm zu folgender Beurteilung. Das Geschwindigkeitsverhältnis wird mit 120 berechnet und bewertet. In diesem Falle wäre es als Parameter für Feinstschleifen anzusehen, bei dem gegebenenfalls Schleifbrand auftreten kann. Der berechnete Schleifüberdeckungsgrad 5,7 wäre für das Feinschleifen bei guter Oberflächengüte aber langer Prozesszeit geeignet, auch die Zustellung von 5 µm entspricht einem Parameter für das Feinschleifen. Wiederum werden das Zeitspanvolumen (1,24 mm3/mm.s) und die Schrupp- und Ausfunkzone berechnet (5,26 beziehungsweise 24,74 mm).
Schleifstrategie
Über den Menüpunkt «Schleifstrategie» lassen sich jeweils Vorschläge für eine mehrstufige Prozessführung anzeigen. Der Prozess wird in mehreren Stufen, bestehend aus Abrichten, Schruppen, Schlichten und gegebenenfalls Feinschlichten und Ausfunken (je nach geforderter Rauheit, Formgenauigkeit und Prozessstabilität) untergliedert. Nach der ersten Schleif-Prozessstufe wird in jeder weiteren Stufe jeweils unter anderem der Radialvorschub beziehungsweise das Zeitspanungsvolumen und die Werkstückdrehzahl reduziert, bis das Endmass erreicht ist. Durch dieses Vorgehen können vorgegebene Mass- und Formgenauigkeiten sowie Oberflächenqualitäten erreicht werden.
Im Beispiel (Bild 6) wurde für einen Aussenrund-Einstechprozess der Werkstoff Stahl (die Werkstückhärte beeinflusst nur die Auswahl der Schleifscheibenspezifikation und nicht die Prozessparameter), eine cBN-Schleifscheibe mit keramischer Bindung, Ø 400 mm und 30 mm Scheibenbreite mit B107-Körnung (das System wandelt automatisch die Körnung in Mesh) ausgewählt. Die Umfangsgeschwindigkeit der Schleifscheibe wurde mit 50 m/s (es wird empfohlen die maximal mögliche Schnittgeschwindigkeit auszuwählen) und der Werkstückdurchmesser mit 50 mm festgelegt. Es wurden sowohl für die Rauheit, als auch für die Formgenauigkeit und Stabilität mittlere Anforderungen definiert.
Der Grinding-Expert schlägt für die gewählten Parameter eine Schleifstrategie mit 4-stufigem Schleifprozess (Schruppen, Schlichten, Feinschlichten und Ausfunken) vor (Bild 7). Für den Abrichtprozess wird ein Überdeckungsgrad Ud von 3 bis 5, eine Abrichtzustellung von 2 mal 0,003 bis 0,004 mm mit einem Geschwindigkeitsverhältnis für rotierende Abrichter von +0,6 bis +0,8 vorgeschlagen. Das geeignete Abrichtintervall muss durch Langzeituntersuchungen an der Maschine definiert werden. Bis zu einem verbleibenden Aufmass von 0,03 mm wird ein Schruppprozess mit einem Geschwindigkeitsverhältnis von 50 bis 60, die Werkstückumfangsgeschwindigkeit von 0,83 bis 1 m/s (Werkstückdrehzahl von 317 bis 382 min-1) und eine radiale Vorschubgeschwindigkeit von 1,3 bis 2,6 mm/min empfohlen. Bei diesen Parametern wäre ein spezifisches Zeitspanvolumen (Q’w) von 3,4 bis 6,8 mm3/mm.s und eine Prozesszeit von 5,1 bis 10,2 s zu veranschlagen. Der nachfolgende Schlichtprozess (bis zu einem Aufmass von 0,01 mm) wird mit einem Geschwindigkeitsverhältnis von 80 bis 100, der Werkstückumfangsgeschwindigkeit von 0,5 bis 0,63 m/s (Werkstückdrehzahl 191 bis 241 min-1) und einer radialen Vorschubgeschwindigkeit von 0,26 bis 0,97 mm/min bei einem Zeitspanvolumen von 0,68 bis 2,55 mm3/mm.s, was eine Prozesszeit von 1,2 bis 4,6 s verursacht, vorgeschlagen. Die Empfehlungen für den folgende Feinschlichtprozess (letzte 0,01 mm) wären: Geschwindigkeitsverhältnis 110 bis 130, Werkstückumfangsgeschwindigkeit 0,38 bis 0,45 m/s (Werkstückdrehzahl 145 bis 172 min-1) und radiale Vorschubgeschwindigkeit 0,04 bis 0,31 mm/min. Das Zeitspanvolumen entspricht mit diesen Parametern 0,1 bis 0,8 mm3/mm.s und die Prozesszeit beträgt 1,9 bis 15 s. Abschliessend wird ein Ausfunkprozess vorgeschlagen mit einem Geschwindigkeitsverhältnis von 110 bis 130, einer Werkstückumfangsgeschwindigkeit von 0,38 bis 0,45 m/s (Werkstückdrehzahl von 145 bis 172 min-1) bei maximal 15 Werkstückumdrehungen beziehungsweise einer Prozesszeit bis 5 s.
Troubleshooting
Über die Option «Troubleshooting» können die Ursachen für gegebene Schleiffehler (optisch und geometrisch) ermittelt werden. Für die Verfahren Aussenrundschleifen, Innenrundschleifen, Flach- und Spitzenlosschleifen sind Troubleshooting-Massnahmen integriert, die verfahrensspezifische Hinweise zur Beseitigung der wahrscheinlich vorliegenden Probleme geben und somit die Korrektur des spezifischen Schleifprozesses zur Erzielung optimaler Schleifergebnisse ermöglichen. Bild 8 zeigt das Troubleshootingmodul für das Aussenrundschleifen.
Fallbeispiele
Um das entwickelte Grinding-Expert-Programm zu validieren wurden mehrere Versuchsreihen bei unterschiedlichen Industriefirmen durchgeführt. Die Ergebnisse waren durchweg sehr positiv, so resultierten in allen Fällen optimierte Schleifprozesse, die sich durch eine verbesserte Genauigkeit bei höheren Abtragsraten, verringerter Rauheit und Schleifzeit auszeichnen. Nachfolgend werden exemplarisch zwei über den Grinding-Expert optimierte Aussenrundschleifprozesse dargestellt.
Fallbeispiel 1 – Optimierung eines Aussenrundschleifprozesses
Die Untersuchungen wurden auf eine Studer S40 Aussenrundlängsschleifmaschine durchgeführt. Es wurde eine B1A1 D450T25X5-B91 C175V Schleifscheibe eingesetzt, die mit einer galvanisch gebundenen Formrolle D501 (Ø 150 mm) abgerichtet wurde und ein HSS-Werkstück (65 HRc Ø 20x200 mm, Aufmass 0,55 mm) geschliffen. Als Kühlschmierstoff wurde eine 5-prozentige Emulsion eingesetzt.
Die Untersuchungsparameter, wie Werkstückstoff, Werkstückabmessung, Spezifikationen, Abmessungen Schleifscheibe und Abrichter, sowie der eingesetzte Kühlschmierstoff sind im Bild zu sehen. Vor der Optimierung wurde der Schleifprozess mit den in Tabelle 1 gezeigten Parametern durchgeführt. Die erzielte Oberflächenrauheit nach dem Schleifen Rz war 1,6 bis 2 µm.
Der Prozess wurde durch die Optimierung über den Grinding-Expert mit den in Tabelle 2 zusammengestellten Parametern verändert.Durch die Optimierung mithilfe des Grinding-Expert konnte die Prozesszeit über 70 Prozent reduziert werden. Gleichzeitig wurde eine feine und sehr gleichmässige Oberflächenrauheit erzielt, die auf Rz < 1,5 µm verbessert wurde.
Fallbeispiel 2 – Optimierung eines Aussenrundschleifprozesses
In Fallbeispiel 2 erfolgte die Optimierung auf einer Studer S21 Aussenrundschleifmaschinen mit einer D1A1 D400T15X5-D126 C75 B-Schleifscheibe, abgerichtet mit EKW 100/1 G6V und geschliffen mit Schleiföl. Die Untersuchungen wurden mit einem HM-Werkstück durchgeführt (Ø 17,5x50 mm, Aufmass 10 mm). Vor der Optimierung wurde der Prozess mit den in Tabelle 3 genannten Parametern durchgeführt. Mit diesen Ursprungsparametern wurde eine Oberflächenrauheit von Rz < 1 µm erreicht.
Auch dieser Prozess wurde über den Grinding-Expert verbessert. Die resultierenden Schleifparameter sind in Tabelle 4 zu finden. Durch die Optimierung mit dem Grinding-Expert wurde die Prozesszeit über 75 Prozent reduziert. Die Rauheit Rz war weiterhin kleiner als 1 µm.
Zusammenfassung
Der KSF-Grinding-Expert ermöglicht die optimale Auswahl von:
Somit lassen sich durch den Grinding-Expert:
Es ist erstmalig weltweit ein System verfügbar, das eine grosse industrielle Nachfrage bedient. Schleifende Bearbeitungsprozesse können zukünftig auch ohne tiefere Schleifkenntnisse werkstoffabhängig und effizient durchgeführt werden.
Ein zusätzliches Highlight ist das Troubleshooting-Modul, das eine sinnvolle Behebung von Schleiffehlern möglich macht.
Das System wurde erfolgreich in einigen industriellen Anwendungen evaluiert. Es konnten jeweils Prozessoptimierungen in Form von Verbesserung der Abtragsrate erreicht werden.
Die Oberflächenrauheit nach der Optimierung war mindestens gleich fein, wie vor der Optimierung, in einigen Fällen wurden trotz erhöhter Abtragsrate durch die Optimierung feinere Oberflächen erzielt.
Zugangsinformationen
Es besteht die Möglichkeit den Grinding-Expert zwei Wochen lang unverbindlich zu testen. Bei Gefallen ist eine Jahresgebühr von EUR 750 pro gleichzeitiger Nutzung durch einen User fällig. Weitere Infos unter www.grindingexpert.de.
Danksagung
Die Autoren danken der Firma Bärhausen GmbH & Co. KG und der Firma CNC-Technik Weiss GmbH für die fruchtbare Zusammenarbeit, die diese Arbeit erst ermöglichte.
Das Projekt wurde unterstützt vom Bundesministerium für Bildung und Forschung im Programm CoHMed Connected Health in Medical Mountains, Impulsprojekt 04 Digitalisierung in der Medizintechnik-Fertigung (DigiMed), Förderkennzeichen 13FH51041A.
Zu den Autoren
Prof. Dr.-Ing. Bahman Azarhoushang und
Dr.-Ing. Heike Kitzig-Frank,
Stellvertretende Institutsleiterin KSF
Hochschule Furtwangen
Jakob-Kienzle-Strasse 17
D-78054 Villingen-Schwenningen
T +49 (0)7720 307 4215
ksf.hs-furtwangen.de
www.grindingexpert.de
aza@hs-furtwangen.de
Branchentreffpunkt für Medizintechnikunternehmen
9. und 10. September
www.medtech-expo.ch
Die Fachmesse für Industrieautomation
10. und 11. September
www.automation-wetzlar.de
Weltleitmesse für Fügen, Trennen, Beschichten
15. bis 19. September
www.schweissen-schneiden.com