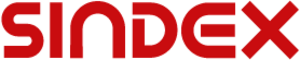
Sindex, Bern
Treffpunkt der Schweizer Technologiebranche
2. bis 4. September
www.sindex.ch
Bild: Moyo Studio, Getty Images, iStock
Die Herausforderung bei der Planung einer Klebung ist, aus dem Angebot der verschiedenen Klebstofftechnologien mit der grossen Anzahl an angebotenen Klebstoffen den «Richtigen» zu finden. Für eine erfolgreiche Klebung muss der Gesamtprozess von der Bauteilkonstruktion bis hin zu einer eventuellen Nacharbeit betrachtet werden, auch unter Einbeziehung kommerzieller Gesichtspunkte.
Das Kleben als modernes Fügeverfahren ist aus vielen Industriebereichen und auch aus dem Handwerk nicht mehr wegzudenken. Die Anwendungen reichen von der Mikroelektronik mit Klebstoffmengen im Bereich von wenigen Milligramm über medizinische Anwendungen, die uns beispielsweise in der Zahnmedizin alltäglich begegnen, bis hin zu Anwendungen in der Energietechnik, wo bei der Verklebung der Rotorblätter für Windkraftanlagen mehrere Hundert Kilogramm Klebstoff pro Teil benötigt werden.
Da die Qualität von Klebungen, was im Übrigen unter anderem auch für Schweissverbindungen gilt, nicht vollständig zerstörungsfrei geprüft werden kann, sondern einer zerstörenden Prüfung bedarf, verbietet sich eine 100 Prozent Kontrolle von allein. Stattdessen sollte im Sinne der DIN 2304-1 [1], beziehungsweise der neuen, diese Norm ersetzenden DIN EN ISO 21368 [2] schon bei der Planung auf ein sinnvolles Zusammenspiel von organisatorischen Massnahmen und fertigungsbegleitenden Prüfungen zur Sicherstellung einer qualitätsgerechten Ausführung der Klebung hingearbeitet werden. Weiterführende Hinweise zur Umsetzung der aus der DIN 2304-1 resultierenden Anforderung finden sich in [3].
Erstellung der Anforderungsprofile
So vielfältig wie die Anwendungen der Klebtechnik sind auch die Anforderungen, die an die geklebten Bauteile und somit an die Klebung und den Klebstoff gestellt werden. Somit ist es nicht verwunderlich, dass der Weg zu einer erfolgreichen Klebung (Bild 1) mit der Erstellung des Anforderungsprofils als Zusammenstellung der unmittelbaren, überprüfbaren Anforderungen beginnt. Erfahrungen aus der Praxis zeigen, dass am Ende der Erstellung des Anforderungsprofis häufig die Aussage «Der Klebstoff muss viel mehr können, als wir angenommen haben» gemacht wird. Deshalb empfiehlt es sich, sowohl bei den Anforderungen an das geklebte Bauteil als auch an den Klebstoff zwischen notwendigen und wünschenswerten Eigenschaften zu unterschieden. Dies vermeidet, den Aufwand zu hochzutreiben oder keine praktikable Lösung zu finden – denn einen Klebstoff, der passend für jeden Anwendungsfall ist, gibt es nicht.
Es bietet sich an, zunächst mit den Anforderungen an das geklebte Teil und hier insbesondere an die Klebung zu starten. Dabei werden die externen, aus der vorgesehenen Anwendung des Bauteils unter Berücksichtigung der Lebensdauererwartung resultierenden Anforderungen ermittelt. Hierbei geht es zunächst darum, die bei der bestimmungsgemässen Anwendung zu erwartenden mechanischen Lasten zu ermitteln. Auch die aus den klimatischen Bedingungen, also dem Temperatureinsatzbereich (minimale und maximale Temperatur sowie dem zeitlichen Verlauf auftretender Temperaturwechsel), der jeweiligen relativen Luftfeuchtigkeit, einer eventuellen Strahlungsbelastung (UV-Licht) sowie dem eventuellen Kontakt zu Wasser, Betriebsstoffen oder Chemikalien, resultierenden Belastungen müssen genauso wie die zu fertigende Stückzahl und die angestrebten Taktzeiten berücksichtigt werden. Zusätzlich können weitere Eigenschaften wie zum Beispiel Brandschutz, lebensmittelrechtliche Zulassung, elektrische oder thermische Isolierung beziehungsweise Leitfähigkeit, sowie eine akustische Entkopplung gefordert sein und müssen berücksichtigt werden. Natürlich sind auch regulatorische Anforderungen wie zum Beispiel die der verschiedenen Chemikalienverbotslisten und gegebenenfalls auch die aus dem vorgesehenen Übergang zu einer Kreislaufwirtschaft resultierenden Forderungen wie Langlebigkeit, Reparierbarkeit oder Verträglichkeit mit Recyclingprozessen zu berücksichtigen.
Diese externen Vorgaben stammen in der Regel vom Kunden oder sind Anforderungen, die sich aus den Erwartungen an das zu fertigende Bauteil ableiten. Daneben gilt es auch, die sich aus den räumlichen Gegebenheiten der Fertigungsumgebung und der vorhandenen Infrastruktur sowie sonstigen internen technischen oder kommerziellen Vorgaben ergebenden Anforderungen zu berücksichtigen. Auch der Umwelt- und Arbeitsschutz müssen beachtet werden.
Im nächsten Schritt gilt es, das Anforderungsprofil an das Bauteil in ein Anforderungsprofil an den Klebstoff unter anderem als Grundlage für die Klebstoffauswahl zu übersetzen. Spätestens hier müssen die anzuwendenden Prüfmethoden und die zu erreichenden Werte realistisch spezifiziert werden. Soweit möglich, sollte hierbei auf etablierte, genormte Verfahren zurückgegriffen werden, um die Zusammenarbeit mit Klebstoffanbietern zu vereinfachen. Die auf der Internetseite des Industrieverbands Klebstoffe e.V. verfügbare Normenliste [4] bietet eine wertvolle Hilfe bei der Identifikation geeigneter Prüfmethoden. Es hat sich bewährt, alle relevanten internen oder externen Stakeholder in die Erstellung der Anforderungsprofile einzubeziehen (Bild 2) und jede Information, beziehungsweise deren Änderungen sorgfältig zu dokumentieren. Wird nicht über ausreichende klebtechnische Expertise verfügt, sollte die Unterstützung durch einen klebtechnischen Berater in Betracht gezogen werden.
Sicherheitseinstufung
Auch wenn die nachfolgende, auf den erstellten Anforderungsprofilen aufbauende Sicherheitseinstufung gemäss [1] und [2] genau genommen allein die Auswirkungen eines Versagens der Kraftübertragungsfunktion der Klebung berücksichtigt, ist es sinnvoll, auch weitere, darüberhinausgehende Anforderungen mit einzubeziehen. Das primäre Ziel der Sicherheitseinstufung ist, sich der Auswirkungen einer Nichterfüllung der Anforderungen bewusst zu werden und auf dieser Grundlage den zur Fehlerprophylaxe notwendigen Umfang an Massnahmen zur Sicherstellung einer fachgerechten Umsetzung festzulegen. Hierzu geben [1] und [2] wertvolle Hinweise.
Die nächsten Schritte
Die nächsten, in Bild 1 übereinander dargestellten Schritte auf dem Weg zu einer erfolgreichen Klebung, Klebstoffauswahl, Auswahl der Fügeteilwerkstoffe und deren Oberflächenbehandlung, klebgerechten Konstruktion sowie Fertigungsplanung erfolgen eng verzahnt. So hat der Werkstoff der Fügeteile Auswirkungen auf die klebgerechte Konstruktion und die Klebstoffauswahl, an deren Ergebnis wiederum das Verfahren der Oberflächenbehandlung angepasst werden muss. Sofern auf bestehende klebtechnische Anlagentechnik zurückgegriffen werden soll, hat dies einen direkten Einfluss auf die Klebstoffauswahl. Andernfalls kann die Fertigungsplanung im Anschluss an die anderen Schritte erfolgen. Jedoch dürfen die Randbedingungen wie das zur Verfügung stehende Raumangebot sowie kommerzielle Gesichtspunkte wie die Investitions- und laufenden Betriebs- beziehungsweise Personalkosten nicht ausser Acht gelassen werden.
Klebgerechte Konstruktion
Wie bei allen Fügeverfahren muss die Bauteilkonstruktion dem jeweiligen Prozess angepasst werden, also klebgerecht sein. So sollte neben der Bereitstellung einer ausreichend grossen Klebfläche das Auftreten von Schäl- oder Spaltbelastungen vermieden und die Kräfte möglichst flächig durch Zug, Druck, Scherung oder Torsion übertragen werden (Bild 3). Eine einfache Methode, die Verbundfestigkeit zu erhöhen, besteht darin, die zur Verfügung stehende Klebfläche zu vergrössern. Bild 4 zeigt dies an dem einfachen Beispiel der Klebung eines Deckels auf einen zylindrischen Körper. Beispiele, wie durch konstruktive Massnahmen ungünstige Schäl- oder Spaltbelastungen durch eine klebgerechte Konstruktion vermieden werden können, finden sich auch in [5].
Vielfach hat das Kleben das Image einer nicht gegebenen Wiederlösbarkeit und steht somit scheinbar in einem Widerspruch zu den Anforderungen hinsichtlich einer Reparierbarkeit oder Recyclingfähigkeit der miteinander verklebten Bauteile. Das dies nur ein scheinbarer Widerspruch ist, zeigen die in der DIN/TS 54405 [6] aufgeführten Verfahren, die geeignet sind, Klebungen zum Beispiel für anstehende Reparaturen wieder zu lösen. Hierbei muss das Bauteil so konstruiert werden, dass die zum Lösen der Klebung angewendeten Bedingungen eingesetzt werden können, bei bestimmungsgemässer Verwendung des Teils jedoch nicht auftreten.
Ein einfaches Beispiel zeigt Bild 5. Der im Heisssiegelverfahren mit dem Becher verbundene Aluminiumdeckel bietet gegenüber den bei Transport und Lagerung einwirkenden Belastungen eine ausreichende Festigkeit. Mit Hilfe der am Deckel vorgesehenen Anfasslasche kann die Klebung auf Schälung belastet und der Deckel vom Becher gelöst werden. Ein weiteres Beispiel ist die Reparatur einer durch Steinschlag beschädigten, in das Fahrzeug eingeklebten Windschutzscheibe.
Um zu verhindern, dass die im Fahrbetrieb auftretende Verformungen der Fahrzeugkarosserie über den Klebstoff auf die Windschutzscheibe einwirkt und zu einer Rissbildung führt, werden elastische Polyurethanklebstoffe in dicker Schicht eingesetzt. Der Klebflansch ist so konstruiert, dass die Klebung für den Fall einer Reparatur zugänglich ist und mit einem speziell geformten Messer oder einem Draht getrennt werden kann. Nach Ausbau der defekten Scheibe werden grobe, auf der Karosserie verbleibende Klebstoffreste entfernt und der verbliebene Klebstoff mit einem Primer aktiviert, sodass die neue Scheibe unter Verwendung eines Polyurethanklebstoffs eingesetzt werden kann.
Auswahl der Fügeteilwerkstoffe und der Oberflächenbehandlung
Auch wenn die Entscheidung über die Fügeteilwerkstoffe aufgrund der vielfältigen Anforderungen an das Bauteil nur sehr bedingt durch klebtechnische Belange beeinflusst werden kann, sollte vorhandener Spielraum genutzt werden, um den Klebprozess nicht unnötig zu erschweren und dadurch bedingte Mehrkosten zu vermeiden. So erfordern preisgünstige polyolefinische Werkstoffe wie zum Beispiel Polyethylen, Polypropylen oder EPDM aufgrund ihrer geringen freien Oberflächenenergie und daraus resultierenden schlechten Benetzbarkeit entweder spezielle Klebstoffe oder den zusätzlichen Prozessschritt einer Oberflächenaktivierung zum Beispiel mittels Plasmatechnologien.
Bei der Auswahl der für den Formgebungsprozess erforderlichen Trennmittel ist zu beachten, dass diese vor dem Kleben von der Klebfläche durch einen entsprechenden Reinigungsschritt entfernt werden müssen. Silikonhaltige Trennmittel sind nicht vollständig entfernbar und können zu Haftungsverlusten bis hin zu einem vorzeitigen Versagen der Klebung führen.
Entsprechendes gilt für metallische Werkstoffe und die dort verwendeten Korrosionsschutz-, Schneid- und Ziehöle sowie -fette. Zwar zeigen viele heisshärtende Klebstoffe und auch die Gruppe der MMA-Klebstoffe eine gewisse Toleranz gegenüber diesen Ölen, jedoch bedarf dies einer Überprüfung der Kompatibilität des jeweiligen verwendeten Öls mit dem Klebstoff.
Auch ist es schwierig, weichmacherhaltige Kunststoffe wie Weich-PVC dauerhaft zu verkleben, denn die migrationsfähigen Weichmacher können in die Klebschicht wandern und dadurch zu einem vorzeitigen Festigkeitsverlust führen.
Klebstoffauswahl
Aus dem für den Klebstoff erstellten Anforderungsprofil zeichnen sich aufgrund ihrer Eigenschaften zunächst meist ein bis drei geeignete Klebstofftechnologien ab. Vor dem Hintergrund des konkreten Anwendungsfalls werden diese unter Berücksichtigung der jeweiligen spezifischen Vor- und Nachteile zwischen den beteiligten Stakeholdern diskutiert. Dabei kann es dazu kommen, dass eine zunächst als praktikabel angesehene Technologie wieder verworfen werden muss.
Im nächsten Schritt werden gezielt Anbieter von Klebstoffen der ausgewählten Technologien angesprochen und das Anforderungsprofil erläutert. Die seitens der Klebstoffanbieter vorgeschlagen Produkte werden dann anhand der jeweiligen technischen Datenblätter verglichen. Dabei ist zu beachten, dass sich die von den Herstellern zu ihren Klebstoffen in den technischen Datenblättern gemachten Angaben zum Teil recht deutlich unterscheiden. Das betrifft nicht nur den Umfang der Daten, sondern auch die Methoden, nach denen diese ermittelt wurden. Häufig wird die verwendete Methode lediglich durch eine Nummer einer als intern bezeichneten Methode benannt, sodass die Prüfbedingungen nicht oder nur bedingt ersichtlich sind. So ist ein direkter Vergleich nicht ohne weiteres möglich und erfordert ein entsprechendes klebtechnisches Fachwissen. Trotzdem werden in einer ersten Vorauswahl potenziell erfolgversprechende Klebstoffe für erste Versuche ausgewählt.
Nachweisführung durch Prüfung der ausgewählten Klebstoffe
Ziel der Nachweisführung ist es, zu zeigen, dass die Beanspruchbarkeit der Klebung über seine gesamte Produktlebensdauer grösser ist als die real auftretenden Belastungen. Dies betrifft nicht nur die durch die DIN 2304-1 [1] beziehungsweise deren Nachfolger der DIN EN ISO 21368 [2] genannte Funktion der Lastübertragung, sondern alle im Anforderungsprofil identifizierten Belastungen. Für ein erstes Screening empfiehlt es sich, aus den bei der Erstellung des Anforderungsprofils festgelegten Prüfmethoden zunächst die auszuwählen, die kurzfristig Ergebnisse liefern. Dadurch lässt sich die Anzahl der zeitaufwendigen Prüfungen reduzieren.
Da zu diesem Zeitpunkt meist noch keine serienfallenden Fügeteile vorliegen, muss die Prüfungen zunächst an Prüfkörpern aus einem den späteren Serienteilen möglichst ähnlichen Werkstoff durchgeführt werden. Da die für die Ausbildung der Adhäsion ablaufenden Prozesse an der Oberfläche stattfinden, kommt dieser eine besondere Bedeutung zu. Auch wenn die Prüfergebnisse dann nur bedingt auf Serienteile übertragen werden können, sollten zu diesem Zeitpunkt verschiedene Verfahren zur Oberflächenbehandlung mit einbezogen werden. Gleiches gilt für erste Zeitraffertests zur Ermittlung des Langzeitverhaltens der Klebung. Hierbei wird die Auswirkung der mit dem Anforderungsprofil identifizierten Belastungen auf eine Klebung simuliert. Ziel ist es, mit möglichst kurzen Prüfzeiten Hinweise auf die Langzeitbeständigkeit einer Klebung unter Realbedingungen zu erhalten. Hierzu werden reale Bauteile oder standardisierte Prüfkörper nach dem Durchlaufen von Zeitraffertests geprüft, bei denen die unter realen Gebrauchsbedingungen über die erwartete Lebensdauer verteilt einwirkenden Belastungen verschärft und zeitlich komprimiert ablaufen. Das Ergebnis wird dann mit den ohne Auslagerung erzielten beziehungsweise den im Anforderungsprofil festgelegten Werten verglichen und bewertet. Bei der Festlegung der Auslagerungsbedingungen wird unter anderem die Tatsache genutzt, dass die bei der Klebstoffalterung ablaufenden Vorgänge durch eine Erhöhung der Temperatur beschleunigt werden, und deshalb die Prüftemperatur erhöht. Eine Faustformel besagt, dass eine Temperaturerhöhung um 10 K eine chemische Reaktion um den Faktor zwei bis vier beschleunigt. Dabei muss jedoch beachtet werden, dass das sinnvolle Ausmass der Beschleunigung begrenzt ist. Eine höhere Temperatur kann neben der Beschleunigung von Alterungsreaktionen auch den Ablauf von Reaktionen ermöglichen, die aufgrund ihrer Aktivierungsenergien unter normalen Betriebsbedingungen nicht stattfinden können. Bei der zeitlichen Komprimierung werden die Zeiträume, in denen das Bauteil unkritischen Bedingungen ausgesetzt ist, zugunsten von kritischen Bedingungen wie erhöhter Temperatur, Medieneinfluss oder mechanischer Belastung verkürzt. Der dadurch bedingte Wegfall von Erholungsphasen hat einen Einfluss und muss berücksichtigt werden. [7]
Für den Fall, dass sich hierbei nur ein oder kein Klebstoff als vielversprechend herausstellt, kann ein Neustart der Klebstoffauswahl durch erneute Kontaktaufnahme, auch zu weiteren Klebstoffanbietern, neue Möglichkeiten eröffnen. Es kann aber auch sein, dass die im Anforderungsprofil festgeschriebenen Kriterien, insbesondere solche, die nicht aus den Anforderungen an das Bauteil, sondern zum Beispiel aus dem angestrebten Fertigungsprozess resultieren, überdacht werden müssen. Im Idealfall zeigen sich jedoch zwei bis drei Klebstoffe als vielversprechend, die dann gemäss des erstellten Anforderungsprofils weiterführenden anwendungsorientierten Prüfungen auch am realen Bauteil unterzogen werden.
Fertigungsplanung – Festlegung des Klebeprozesses
Unabhängig davon, ob es sich um eine manuelle Kleinserienfertigung oder eine Grossserie handelt, müssen neben dem eigentlichen Klebprozess, das heisst der Oberflächenbehandlung der Fügeteile, der Klebstoffapplikation, dem Fügevorgang und der Klebstoffhärtung, auch die vor- und nachgelagerten Prozessschritte klebgerecht und unter Berücksichtigung der Eigenschaften des ausgewählten Klebstoffs ausgelegt werden. Gleiches gilt für eventuell erforderlich werdende Nacharbeit. Hierzu gehört die Festlegung der fertigungsbegleitenden Qualitätssicherungsmassnahmen mit dem Ziel, Abweichungen von den Fertigungsvorgaben und daraus resultierende Klebfehler frühzeitig, aber mindestens vor Auslieferung zu erkennen.
Aufgrund der Vielfalt der an geklebte Bauteile gestellten Anforderungen und den daraus ableitbaren organisatorischen und technischen Qualitätssicherungsmassnahmen (siehe hierzu [3]) würde es den Umfang dieses Artikels übersteigen, diese detailliert zu behandeln. Stattdessen sei auf den informellen Anhang der DIN EN ISO 21368 [2], die DIN SPEC 2305-1 [8] beziehungsweise deren kürzlich veröffentlichte Nachfolgeversion DIN/TS 2305-1, [9] verwiesen.
Validierung
Am Ende steht zusammen mit der Validierung des gesamten Klebprozesses die Bestätigung, dass die unter Serienbedingungen gefertigten Bauteile die an sie gestellten Anforderungen vollumfänglich erfüllen und die Dokumentation des Klebprozesses in einer Arbeitsanweisung. Hier werden die einzelnen Arbeitsschritte, die Vorgehensweise, wie bei eventuellen Abweichungen von festgelegten Vorgaben zu verfahren ist, und die zulässigen Nacharbeitsverfahren eindeutig und verständlich beschrieben.
ZUM AUTOR
Dr. Hartwig Lohse
Klebtechnik Dr. Hartwig Lohse e.K.
Hofberg 4
D-25597 Breitenberg
T +49 (0)4822 95180
www.hdyg.de
hl@hdyg.de
Branchentreffpunkt für Medizintechnikunternehmen
9. und 10. September
www.medtech-expo.ch
Die Fachmesse für Industrieautomation
10. und 11. September
www.automation-wetzlar.de
Weltleitmesse für Fügen, Trennen, Beschichten
15. bis 19. September
www.schweissen-schneiden.com