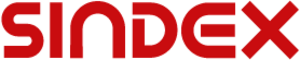
Sindex, Bern
Treffpunkt der Schweizer Technologiebranche
2. bis 4. September
www.sindex.ch
Bild: PushCorp Inc.
Oberflächen schleifen, polieren oder Kanten entgraten sind in nahezu allen Bereichen der Industrie personal- und kostenintensive Arbeitsschritte. Auch die Mitarbeiter sind einer hohen Belastung ausgesetzt. Sei es durch den Schleifstaub in der Luft, die für Gelenke und Muskeln unergonomische Arbeitshaltung oder durch die Vibration des Werkzeugs. Dem gegenüber stehen die Vorteile den Prozess zu automatisieren.
Durch die absolute Wiederholgenauigkeit der Robotik lässt sich eine konstante Qualität erreichen. In Zeiten des Fachkräftemangels wird Personal verfügbar, das an anderer Stelle wieder eingesetzt werden kann.
Viele Unternehmen stehen nicht vor der Frage, ob ein manueller Bearbeitungsschritt zu automatisieren ist, sondern wie er für ihre spezifischen Anforderungen gelöst wird. Dies sind Faktoren wie die Eingliederung in die bestehende Prozesskette, ein begrenzter Platzbedarf, zeitliche Vorgaben und natürlich die zu erwartende Qualität des Endproduktes. Bis auf die Qualität, die zwingend einen Versuch unter Realbedingungen erfordert, sind alle Fragen mit den Werkzeugen der virtuellen Fabrik zu beantworten.
Sichere Eingangsdaten mit 3D-Scanning
Gerade die Planung im Brownfield-Bereich erfordert eine exakte Aufnahme der Gegebenheiten vor Ort. Die bis dato gebräuchlichen Messwerkzeuge wie Lasermessgerät, Meterstab oder Massband bilden jedoch immer nur einen kleinen Teilbereich ab. Bei vorhandenen Plänen sind oft nicht alle Details, wie beispielsweise Rohrleitungen, die für die Planung erforderlich sind, enthalten. Es muss somit oft nachgemessen werden. Nachmessungen sind zusätzlicher Aufwand und kosten Zeit und Geld. Auch in Sachen Präzision ist hier noch viel Luft nach oben.
Mittels 3D-Laserscanning wird in nur einem Termin ein hochpräzises digitales Abbild der gesamten Umgebung erzeugt, das in allen gängigen 3D-Programmen integriert und weiterverarbeitet werden kann. Jedes noch so kleine Detail, das im Planungsprozess früher unbemerkt blieb und im späteren Verlauf zu Problemen führte, ist beim 3D-Scanning enthalten. Die anschliessende Weiterverarbeitung der Daten führt zum einen zu einem für alle Beteiligten frei zugänglichen «virtuellen Rundgang» (walk-through), bei dem jeder beliebige Punkt in der Anlage für die eigenen Zwecke ausgemessen werden kann.
Virtuelle Absicherung der Erreichbarkeit
Die Erreichbarkeit ist nicht im Zusammenhang zu sehen, ob der Prozess erreicht werden kann, sondern wie gut der Roboter den zu bearbeitenden Bereich erreicht. Es steht also die Auswahl des geeigneten Robotertyps und dessen Standort im Fokus. Die sogenannte Erreichbarkeitsstudie gibt nicht nur Antwort auf die Frage, welcher Robotertyp zum Einsatz kommt, sondern auch, ob er seine Aufgabe optimal erledigen kann. Zum anderen wird der Roboter auf seine Traglast präzise ausgelegt. Dabei wird der Massenschwerpunkt, der zu erwartenden Last sowie die am Roboter montierten Anbauten in die Berechnung einbezogen. Ein Roboter, der seine maximal zulässige Handhabungslast überschreitet, birgt grosse Gefahren für Mensch und Maschine.
Im Umkehrschluss wird ein überdimensionierter Roboter niemals die gleiche Genauigkeit und Geschwindigkeit, wie ein optimal ausgelegtes System erreichen. Ein Roboter, der korrekt auf die Aufgabenstellung abgestimmt ist, hat einen geringeren Wartungsaufwand und nur den für seine Aufgabe benötigten Platzbedarf. Er ist kostengünstiger, da nur tatsächlich benötigte Optionen enthalten sind und hat eine längere Betriebsdauer, was wiederum die Verfügbarkeit der Gesamtanlage erhöht.
Virtuelle Absicherung der Prozesszeit
Im nächsten Schritt werden die einzelnen Prozessschritte in einer Taktzeitstudie untersucht. Die Taktzeitstudie gibt nicht nur Aufschluss darüber, ob der Prozess in die Taktzeit hineinpasst, sondern auch, wie viel Reserve für Optimierungen noch zur Verfügung steht. Hierbei werden die einzelnen Arbeitsschritte der Roboter unter Zuhilfenahme von virtuellen Nachbauten der Robotercontroller exakt dargestellt. In solchen Robotersimulationen darf das Prozesswissen aus der Praxis natürlich nicht fehlen. Im Optimalfall führen die Taktzeitstudie Simulationsexpertinnen un -experten durch, die über Erfahrung in der automatisierten Oberflächenbearbeitung aus der Praxis verfügen.
Auch die detaillierteste Simulation dient natürlich nicht dem Selbstzweck, sondern führt am Ende zu einer Umsetzung in einer realen Anlage. Selbstverständlich werden nicht nur die in der Simulation gewonnen Erkenntnisse in der Anlage wiederverwendet, sondern auch zum Beispiel die dort bereits erstellten Roboterprogramme. Durch die sogenannte Offline-Programmierung können diese in der realen Anlage direkt in Betrieb genommen werden und liefern schon nach kürzester Zeit die gewünschten Ergebnisse. Die Inbetriebnahme wird beschleunigt und somit Kosten gespart.
Sichere Bearbeitungstools und Kraftregelung
Mittlerweile gibt es auf dem Markt eine Vielzahl an Herstellern von Bearbeitungstools. Als Betreiber der Anlage profitiert man in erster Linie von hochwertigen Werkzeugen, die dauerhaftem industriellen Einsatz gewachsen sind. Grundsätzlich sollte auf eine entsprechende Leistungsreserve geachtet werden, da permanente Überbeanspruchung zwangsläufig zum Ausfall des Geräts führt.
Die Roboter-Servospindeln des US-amerikanischen Herstellers PushCorp liefern das höchste Leistungsgewicht und den höchsten Wirkungsgrad in der Industrie. Die flüssigkeitsgekühlten Motore schaffen dauerhaft eine Auslastung zu 100 Prozent. Vielseitige Montagemöglichkeiten sowie der Werkzeugwechsel über pneumatischen Aufsteckdorn oder manuelle Werkzeugaufnahme schaffen die nötige Flexibilität.
Die Tools eignen sich zur Single- oder Doppelmontage an der PushCorp-Kraftregelung. Die sensitive Kraftregelung sorgt für einen konstanten Anpressdruck unabhängig vom Roboterarm in jede Richtung. Dieser kann nur einseitig oder auch beidseitig erfolgen. Ebenfalls wählbar sind je nach Anforderung aktive oder passive Kraftregelungen. Bei der aktiven Kraftregelung wird der Anpressdruck einmal eingestellt und das Gerät regelt ihn in jeder beliebigen Position selbstständig. Diese Variante wird eingesetzt bei komplexen dreidimensionalen Konturen und überall dort, wo höchste Präzision gefordert ist. Bei der passiven Kraftregelung wird der Anpressdruck über externe Druckluft eingestellt. Für jede Position wird der Druck programmiert. Die passive Kraftregelung eignet sich besonders für vieleckige, flache Werkstücke und einfachere Anwendungen, wie beispielsweise Schweissnähte glätten. Der Vorteil liegt bei einem wesentlich einfacheren und damit kostengünstigeren Aufbau.
Prozesssicherer Mediumwechsel und -dosierung
Schleifblüten, Schleifscheiben und Polierschwämme sind Verbrauchsmaterialien, für die ein automatisches Wechselsystem nötig ist. Diese Komponenten sind für den prozesssicheren Betrieb des gesamten Systems ausschlaggebend. Wird die Schleifscheibe nicht, schief oder nicht exakt nach ihrem Lochbild aufgenommen hat dies extreme Auswirkungen auf das Werkstück, das im schlimmsten Fall unbrauchbar wird. ASIS stellt seit vielen Jahren Wechselstationen her, die vom Unternehmen selbst oder von verschiedenen Integratoren weltweit eingesetzt werden. Sensoren überprüfen die korrekte Aufnahme des Schleif- und Poliermediums, sodass das Gesamtsystem reibungslos arbeiten kann. Bei manchen Anwendungen, wie dem automatischen Finish ist zudem der Auftrag von Polier- und Schleifpasten notwendig. Auch hierfür existieren Produkte, die für den automatischen Betrieb ausgelegt sind. In mehreren Roboterzellen können bei ASIS die notwendigen Live-Versuche mit eigenen Werkstücken und eigenem Prozessmaterial gefahren werden. Grundsätzlich bleibt der Auftraggeber ungebunden und kann bestehenden Lieferanten weiterhin nutzen.
Optimierung und vorbeugende Wartung
Eines der aktuellsten Themen der digitalen Transformation ist das Sammeln und Auswerten von Daten in Produktionsanlagen. Die Daten schlummern meist ungenutzt auf den Steuerungen der Anlagen. Die ASIS GmbH bietet mit Surface-Analytics 4.0 eine Plattform, die alle relevanten Daten von der SPS in eine Datenbank überträgt und anschliessend übersichtlich in einer Web-Anwendung aufbereitet und visualisiert. Beginnend bei der Auswertung der Anlagenverfügbarkeit bis hin zur Rückverfolgung von fehlerhaften Bauteilen werden alle Informationen zentral in einer Oberfläche bereitgestellt. Die grafische Auswertung gibt zudem Aufschluss über Produktivität, Energieverbrauch und berechnet Vorhersagen über anstehende Wartungen.
Der zukunftssichere Kommunikationsstandard OPC UA wurde hier verwendet. Das System ist optional und kann für kleinere Projektumfänge eingespart werden, um diese wirtschaftlich darzustellen.
In der automatisierten Bearbeitung liegt ein enormes Potential. Durch den sich zuspitzenden Arbeitsmarkt wird sich der Trend zur Automatisierung weiterhin fortsetzen. Die präzise virtuelle Vorplanung vermeidet die Risiken der Umstellung. Praxiserprobte Gesamtsysteme und ein verlässlicher After-Sales ermöglichen planbare Wertschöpfung für den Anlagenbetreiber.
INFOS | KONTAKT
ASIS GmbH
Kiem-Pauli-Strasse 3
D-84036 Landshut
T +49 (0)871 27676-0
www.asis-gmbh.de
mail@asis-gmbh.de
Branchentreffpunkt für Medizintechnikunternehmen
9. und 10. September
www.medtech-expo.ch
Die Fachmesse für Industrieautomation
10. und 11. September
www.automation-wetzlar.de
Weltleitmesse für Fügen, Trennen, Beschichten
15. bis 19. September
www.schweissen-schneiden.com