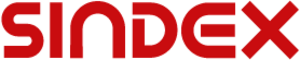
Sindex, Bern
Treffpunkt der Schweizer Technologiebranche
2. bis 4. September
www.sindex.ch
Bilder: KSF
In Zusammenarbeit mit dem KSF wurde bei Maier Werkzeugmaschinen GmbH & Co. KG ein hybrides Langdreh- und Laserbearbeitungszentrum mit integriertem Faserlaser entwickelt, das die klassische Zerspanung (Drehen, Bohren, Fräsen, Schleifen) mit einer Laserbearbeitung ergänzt.
Durch dieses Zusammenspiel bieten sich komplett neue Bearbeitungsmöglichkeiten, wie zum Beispiel die Herstellung von komplexen Konturen und Hinterschnitten, Mikrostrukturierung von Oberflächen, Laserbearbeitung mit einer Schnitttiefe von 10 mm, Laserpolieren, Aufbringen von Laserstrukturen und Optimierung des Spanbruchverhaltens.
Durch den in der Produktion ständig steigende Kostendruck und der Trend zu kleineren Fertigungslosgrössen beziehungsweise steigender Variantenanzahl bei gleichzeitig erhöhten Qualitätsansprüchen sind Maschinen erforderlich, in denen sowohl die Massen- als auch eine Einzelteil- beziehungsweise Variantenfertigung kostengünstig möglich ist. Durch die Fertigung in einer Aufspannung lassen sich Bearbeitungsaufmasse, Genauigkeit, Neben-, Transport- und Rüstzeiten reduzieren. Hinzu kommen steigende Anforderungen bezüglich mechanischer Festigkeit und/oder chemischer Beständigkeit der Werkstoffe. Dies führt vermehrt zum Einsatz hochfester Werkstoffe, wie zum Beispiel Titanlegierungen, die sich nur erschwert bearbeiten lassen.
Geringe Nebenzeiten, kein Werkzeugverschleiss
Durch ihre vielfältigen Anwendungsmöglichkeiten ist die Lasertechnologie prädestiniert für die Hybridverarbeitung in Kombination mit der spanenden Bearbeitung. Durch die Laserbearbeitung können zum Beispiel sehr hohe Materialabtragsraten erzielt und komplexe Konturen und Hinterschnitte realisiert werden. Es entstehen geringe Nebenzeiten, gleichzeitig tritt kein Werkzeugverschleiss auf. Durch die hybride Laserbearbeitung ergeben sich ungeahnte Möglichkeiten, die zusammen mit dem Kompetenzzentrum für Spanende Fertigung (KSF) an der Hochschule Furtwangen in einem geförderten ZIM-Projekt untersucht wurden.
So konnten beispielsweise in kleinste Drehteile (Ø 2,5 mm, Kupferlegierung) Schlitze mit 100 µm Breite hoch produktiv und mit minimalem Materialaufwurf beziehungsweise thermischen Schädigung eingebracht werden (Bild 1).
Neben der reinen Laserbearbeitung, die die Drehteilbearbeitung durch zusätzliche Bearbeitungsmöglichkeiten ergänzt, wurde ein kombinierter Laser-Dreh-Prozess untersucht, bei dem das Brechen von Spänen im Vordergrund stand. Hohe Materialabtragsraten bei Drehprozessen führen im Allgemeinen zu einer grossen Menge an Spänen, die in kurzer Zeit produziert werden. Die erzeugten Späne sind vor allem dann problematisch, wenn sie lang und gekräuselt (wie zum Beispiel Band-, Wirr- und Flachwendelspäne) sind. Beim Drehen von hochlegierten Stählen, wie zum Beispiel rostfreien Stählen, können die durchgehenden Späne die Werkstückoberfläche berühren oder sich in den Werkzeugen und Werkzeughaltern verfangen, was Kratzer auf der fertig bearbeiteten Oberfläche verursacht, die Standzeit der Werkzeuge beeinträchtigt, die Form- und Massgenauigkeit der Teile negativ beeinflussen kann, oder in einigen Fällen sogar die Maschine zum Stillstand bringt.
Die Drehbearbeitung austenitischer Stähle führt oft zur Erzeugung von Wirr- beziehungsweise Flachwendelspänen (langer, durchgehender Späne).
In der Industrie und Forschung wurden die verschiedensten Spanbrechverfahren eingesetzt, um die langen Späne zu verkürzen. Die gebräuchlichste Methode ist die Erzeugung spezieller Taschen auf der Spanfläche von Wendeschneidplatten, über die Späne verformt werden können, aber auch die Anpassung der Prozessparameter, Kühlmittel-Zufuhrsysteme oder das Hinzufügen von Schwingungen zum Prozess wurden beziehungsweise werden als Spanbruchverfahren eingesetzt und untersucht. In diesem Beitrag wird eine neuartige Methode vorgestellt, die neben dem positiven Einfluss auf den Spanbruch auch höhere Materialabtragsraten, geringere Zerspankräfte und bessere Rauigkeiten bewirken kann.
Der Laserkopf wird über der rotierenden Werkstückoberfläche positioniert. Während der Laserbearbeitung fliesst ein koaxiales Stickstoffgas durch die Düse, die die Schmelze ausbläst. Durch die gleichzeitige Axialbewegung des Werkstücks wird eine Spirale auf der Werkstückoberfläche erzeugt (Bild 2).
Kraftwert fast halbiert
Die Nuttiefe kann in Abhängigkeit von den gewählten Laserparametern und der Stahlpositionierung beeinflusst werden. Die Tiefe der Laserrillen wurden deutlich unter der endgültigen Schnitttiefe gehalten, damit keine Beeinflussung des Werkstückmaterials durch die eingebrachte Wärme erfolgt.
Es wurden zwei Stahlsorten untersucht: DIN 1.4571 (austenitischer rostfreier Stahl X6CrNiMoTi17-12-2) und DIN 1.7139 (Kohlenstoffstahl – 16MnCrS5). Beim Drehen ohne Laserbearbeitung entstanden bei allen untersuchten Parametern und beiden Stahlsorten lange, kontinuierliche Flachwendelspäne. Beim Drehen der lasergerillten Oberflächen wurden deutlich kürzere Späne erzeugt. Bild 3 zeigt exemplarisch die erzeugten Späne bei einer Schnitttiefe von 0,75 mm, der Laserrillentiefe von 0,5 mm und einem Abstand der Laserrillen (dLR) von 4 bis 20 mm.
In der Untersuchung wurden weiterhin die spezifischen Schnittkräfte untersucht. Bild 3 zeigt die spezifischen Schnittkräfte für beide Stahlsorten mit und ohne Laserrillen. Durch das Lasern von Rillen wurden die Schnittkräfte insgesamt reduziert. Die deutlichste Reduzierung konnte beim Drehen des rostfreien Stahls 1.4571 bei einer Spiralsteigung von 4 mm gemessen werden, bei der sich der Kraftwert fast halbierte (Bild 4 links oben). Mit zunehmender Schnitttiefe sinken die spezifischen Schnittkräfte (links unten). Die Auswirkung der Laserbearbeitung auf die Verringerung der Schnittkräfte ist bei geringer Schnitttiefe deutlich zu sehen. Die vergleichenden Versuche wurden auf sechs unterschiedlichen Werkstücken durchgeführt. Dabei wurden die Vergleichsmessungen jeweils auf demselben Werkstück vorgenommen: einmal ohne und einmal mit Laserrillen, damit die Kräfte und Rauheiten aussagekräftig verglichen werden konnten.
Keine Vibrationen
Die Laserrillen am Umfang des Werkstücks verringern das Risiko von selbsterregtem Rattern und erzwungenen Vibrationen, da der Schneidprozess wiederholt unterbrochen wird. Die Unterbrechung entsteht durch einen zyklischen dynamischen Aufprall zwischen dem Schneidwerkzeug und den Laserrillen auf dem Werkstück, wodurch sich die Resonanzfrequenz ändert und die Gefahr des Auftretens des selbsterregten Ratterns deutlich verringert wird. Die Versuche zeigten, dass der durch das Laserrillen verursachte unterbrochene Schnitt selbst keine Vibrationen hervorruft.
Die Oberflächenrauheit nimmt mit zunehmender Schnitttiefe zu (Bild 4 rechts unten). Beim konventionellen Drehen ist zu erwarten, dass sich die Oberflächenrauheit mit zunehmender Schnitttiefe tendenziell verschlechtert. Trotz dieses allgemeinen Trends kann das Vorhandensein der Lasernuten die Ra-Werte bei höheren Schnitttiefen proportional verbessern.
Die grössere Reibung und daher eine höhere Prozesstemperatur zwischen den langen Spänen und der Werkzeugspanfläche sind möglicherweise auf die Bildung von Aufbauschneiden zurückzuführen. Bild 5 zeigt die Schnittkanten für ap = 0,75 mm mit und ohne Laserrille. Bei den Drehversuchen mit Laserrillen wurde aufgrund der kürzeren Späne und Schnittlänge zwischen Material und Schneidkante und des unterbrochenen Schnitts fast keine Aufbauschneide festgestellt. Als negativ zu erwähnen ist, dass die Laserrille bei einem Abstand der Laserrillen von dLR = 4 mm zu einer stärken Oxidation der Freifläche der Wendeschneidplatte führt.
Zusammenfassung
Der in eine Langdrehmaschine integrierte Laser wurde zur Erzeugung definierter spiralförmiger Rillen am Umfang der Werkstücke eingesetzt. Dadurch liessen sich lange, kontinuierliche Späne effektiv verkürzen. Weiterhin konnten durch Einbringen der Rillen die Zerspankräfte beim Drehen und die Oberflächenrauheit deutlich reduziert werden.
Die hybride Langdreh-Laserbearbeitung bietet ein grosses Potenzial mit vielen Anwendungsmöglichkeiten zur effektiven Bearbeitung von Langdreh-Werkstücken. Neben hohen Abtragsraten bei Konturbearbeitungsoptionen lassen sich beispielsweise auch Rillen zum Spanbruch in langspanende Werkstoffe einbringen und höhere Produktivität beim Drehen erreichen.
Danksagung
Die Autoren bedanken sich für die finanzielle Unterstützung durch das Bundesministerium für Wirtschaft und Energie (aufgrund eines Beschlusses des Deutschen Bundestages). Das Projekt wurde mit Unterstützung der Arbeitsgemeinschaft industrieller Forschungsvereinigungen (AiF) im Rahmen des ZIM-Projekts Nr. ZF4575002SY8 durchgeführt.
ZU DEN AUTOREN
M.Sc. Esmaeil Ghadiri Zahrani, Prof. Dr.-Ing. Bahman Azarhoushang und Dr.-Ing. Heike Kitzig-Frank
Kompetenzzentrum für Spanende Fertigung (KSF)
Hochschule Furtwangen
Jakob-Kienzle-Strasse 17
D-78054 Villingen-Schwenningen
T +49 (0)7720 307-0
www.hs-furtwangen.de
esmaeil.ghadiri@hs-furtwangen.de
Branchentreffpunkt für Medizintechnikunternehmen
9. und 10. September
www.medtech-expo.ch
Die Fachmesse für Industrieautomation
10. und 11. September
www.automation-wetzlar.de
Weltleitmesse für Fügen, Trennen, Beschichten
15. bis 19. September
www.schweissen-schneiden.com