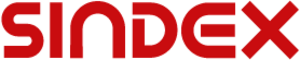
Sindex, Bern
Treffpunkt der Schweizer Technologiebranche
2. bis 4. September
www.sindex.ch
Bilder Fronius International GmbH
Wie wir alle wissen, entsteht beim Schweissen gesundheitsschädlicher Schweissrauch. Möchte man die Belastung von Schweisserinnen und Schweissern reduzieren und gleichzeitig die Arbeitssicherheit verbessern, sind nicht nur Prozessvarianten und Absaugtechnik von grosser Bedeutung. Auch Prozessparameter spielen im Hinblick auf die Emissionsrate eine bedeutende Rolle: Drahtvorschubgeschwindigkeit, Lichtbogenlänge und Korrekturparameter beeinflussen das Ausmass der Schadstoffe entscheidend. Die Aachener Gesellschaft für Forschungs- und Fügetechnik (FEF) nahm gemeinsam mit Fronius International verschiedene Parametereinstellungen unter die Lupe.
Wie aus dem FEF-Abschlussbericht der Schweissrauchuntersuchungen vom 13.10.21 hervorgeht, war der Impulslichtbogen jener Prozess, der im Vergleich mit dem Low-Spatter-Control-Lichtbogen (LSC) und dem Standardlichtbogen – alle von Fronius – den vorteilhaftesten Werkstoffübergang und die geringste Schweissrauchemissionsrate (FER = Fume Emission Rate) verursachte.
In einer weiteren Versuchsreihe wurde eruiert, wie sich verschiedene Brenneranstellungen, Drahtvorschubgeschwindigkeiten und Lichtbogenlängenkorrekturen auf die Emissionsrate auswirken. Geschweisst wurde mit einem PMC-Impulslichtbogen und der TPS 500i von Fronius.
FER beim Schweissen von Auftragraupen
Grundsätzlich kann festgestellt werden, dass die Schweissrauchemission bei 5 m/min Drahtvorschub und neutraler Brenneranstellung am geringsten ist, wobei auffällt, dass bei einer Drahtvorschubgeschwindigkeit von 11 m/min weniger Ausstoss entsteht als bei 8 m/min. Bei schleppender Brennerführung fallen die Emissionen bei allen Drahtvorschubgeschwindigkeiten eine Spur niedriger aus als bei stechender.
Optimieren Schweisserinnen und Schweisser den Lichtbogen mithilfe der Lichtbogenlängenkorrektur (im Versuch bei neutraler Brennerstellung), kann die Schweissrauchemission bei allen Drahtvorschubgeschwindigkeiten deutlich reduziert werden. Anders als bei nicht optimiertem Lichtbogen ist hier der Schweissrauchausstoss bei 8 m/min mit 0,9 mg/s etwas geringer als bei 11 m/min mit 1,1 mg/s (Bild 1).
Vergleich der Spannungsverläufe bei einem Drahtvorschub von 5 m/min
Offensichtlich korreliert die Schweissrauchemissionsrate mit der Anzahl der Kurzschlüsse. Eine hohe Anzahl führt zu einer signifikant höheren FER. Die Studie sieht dies im Werkstoffübergang begründet. Kurzschlusserscheinungen verursachen Prozessstörungen, die Metalldampf und Metallspritzer zur Folge haben. Möchte man die Emissionen auf ein Minimum senken, empfiehlt sich eine Prozesseinstellung, die Lichtbogenlänge und Kurzschlussreduktion auf einen Nenner bringt – also den Lichtbogen nicht zu lang und nicht zu kurz hält. Mit leicht ansteigender mittlerer Spannung werden beide, Kurzschlusserscheinungen und Emission, reduziert (Bild 2).
Die Schweissprozesse bei 8 und 11 m/min verhalten sich hinsichtlich der Zusammenhänge zwischen mittlerer Spannung, Kurzschlusserscheinungen und Schweissrauchemission analog zum Prozess bei 5 m/min.
FER beim Schweissen von Kehlnähten
Beim Impulsschweissen mit Drahtvorschubgeschwindigkeiten von 5 und 8 m/min kommt es mit 0,55 mg/s beziehungsweise 0,7 mg/s zu deutlich kleineren Emissionsraten als mit einem Drahtvorschub von 11 m/s. Hier beträgt der Ausstoss 1,7 mg/s, also im Vergleich zur Drahtförderung von 5 m/min sogar mehr als das Dreifache. Grund dafür ist analog zu den Auftragraupen die geringere Anzahl an Kurzschlusserscheinungen, wobei auch hier die schleppende Brennerführung zu geringeren Ausstössen führt – bei einer Drahtvorschubgeschwindigkeit von 11 m/min sogar zu einer beträchtlich geringeren Emissionsrate (Bild 3). Hier ist der Ausstoss sogar geringer als bei neutraler Brenneranstellung.Insgesamt sind die Schweissrauchemissionen auf niedrigerem Niveau als bei den Auftragraupen. Der jeweils niedrigste Wert der Drahtvorschubgeschwindigkeiten ist mit den Emissionen der optimierten Prozesse (Bild 1, grüne Balken), mit denen die Auftragraupen geschweisst wurden, vergleichbar.
Die Schweissrauchemissionsraten der stechenden und schleppenden Brenneranstellung ähneln sich bei einer Drahtvorschubgeschwindigkeit von 8 m/min in den absoluten Werten – wie auch bei den Auftragraupen – sehr stark. Dagegen tritt beim stechenden Schweissprozess bei 11 m/min mit rund 2,8 mg/s eine signifikant höhere FER zutage.
Vergleich der Spannungsverläufe bei einem Drahtvorschub von 11 m/min
Im Versuch der FEF wurde das Verhältnis zwischen Emissionsrate und mittlerer Spannung bei 11 m/min Drahtvorschubgeschwindigkeit genauer betrachtet: Bei drei Messwerten ergibt sich ein Minimum bei 1,36 mg/s (optimiert mit Lichtbogenlängenkorrektur -1,5 V). Dort befindet sich der Arbeitspunkt, bei dem sporadisch Kurzschlusserscheinungen auftreten, der Lichtbogen aber nicht unnötig lang ist. Der Prozess ohne Lichtbogenlängenkorrektur erzeugt aufgrund des längeren Lichtbogens und der höheren Prozessleistung mehr Emissionen (1,72 mg/s). Steigt die Anzahl der Kurzschlusserscheinungen mit sinkender mittlerer Spannung an (Lichtbogenlängenkorrektur –2,5 V), so steigt auch die Schweissrauchemission (1,6 mg/s) (Bild 4).
Fazit
Schweissrauchoptimierte Prozesse tragen viel zur Emissionsreduktion bei. Schweisserinnen und Schweisser haben es selbst in der Hand: Mit der gezielten Auswahl von Schweissprozess, Drahtvorschubgeschwindigkeit und Lichtbogenlänge kann der Schweissrauch entscheidend reduziert werden.
Zusammenfassend lässt sich sagen: Grundsätzlich ist die Schweissrauchemissionsrate von der Abschmelz- beziehungsweise Prozessleistung abhängig, wobei der Werkstoffübergang entscheidend ist. Ist ein Lichtbogen sowohl zu kurz als auch zu lang, führt das zu höheren Kurzschlussraten und somit zu mehr Schweissrauchemissionen. Optimiert man dagegen den Schweissprozess mithilfe der Lichtbogenlängenkorrektur und verwendet zusätzlich einen Absaugbrenner wie zum Beispiel den Fronius MTW 500i Exento in Kombination mit einer Fronius Exento-HighVac-Absaugung, können bis zu 99 Prozent des Schweissrauchs abgesaugt werden.
Leistungsstarke und punktgenaue Absaugung
Absaugschweissbrenner verhindern das Ausbreiten des Schweissrauchs genau dort, wo er entsteht: unmittelbar beim Schmelzbad. Sie schützen nicht nur die Schweissfachkräfte während der Fügearbeiten, sondern auch alle anderen Personen, die sich in der Werkstückumgebung befinden.
Weil eine komplexe Bauart nicht zulasten der Gesundheit und Produktivität von Schweisserinnen und Schweissern gehen darf, hat Fronius bei der Entwicklung der Absaugschweissbrenner ein besonderes Augenmerk auf Ergonomie gelegt: Sie liegen beim Fügen perfekt in der Hand, während eine LED-Lampe das Schweissen in dunkler Umgebung erleichtert und bei der Qualitätskontrolle unterstützt.
Exento-Absaugschweissbrenner erfüllen die Anforderungen der Norm DIN EN ISO 21904-1 Arbeits- und Gesundheitsschutz beim Schweissen und bei verwandten Verfahren. Mehr Infos zu den Fronius-Absaugbrennern finden mittel Link.
MSG-Schweissparameter
Schweisszusatz: verkupferte Drahtelektrode EN ISO 14341-A: G 3Si1, Ø 1,2 mm
Grundwerkstoff: unlegierter Baustahl S235JR, t = 8 mm
Drahtvorschubgeschwindigkeit 5, 8 und 11 m/min
Schutzgas CORGON® DIN EN ISO 14175: M21-ArC-18, 12l/min
Prozessvarianten PMC-Impuls
Spannungskorrektur und Dynamik Spannungskorrektur 0, Dynamik 0
Schweissposition Auftragraupen PA, Kehlnähte PB
Brenneranstellung neutral, 10° stechend, 10° schleppend
Stromkontaktrohrabstand 15 mm
Schweissgeschwindigkeit 37 cm/min
Mechanisierungsgrad: Vollmechanisiert mit Linearfahrwerk
INFOS | KONTAKT
Fronius Schweiz AG
Oberglatterstrasse 11
CH-8153 Rümlang
T +41 (0)44 817 99 44
www.fronius.ch
sales.switzerland@fronius.com
Branchentreffpunkt für Medizintechnikunternehmen
9. und 10. September
www.medtech-expo.ch
Die Fachmesse für Industrieautomation
10. und 11. September
www.automation-wetzlar.de
Weltleitmesse für Fügen, Trennen, Beschichten
15. bis 19. September
www.schweissen-schneiden.com