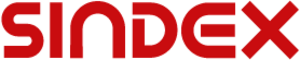
Sindex, Bern
Treffpunkt der Schweizer Technologiebranche
2. bis 4. September
www.sindex.ch
Bild: foto-setzinger.de
Wer sich im Landkreis Tuttlingen, dem Zentrum der Medizintechnik mit der Herstellung von orthopädischen Instrumenten, Knochenschrauben und Implantaten, erfolgreich behaupten will, muss besondere Leistungen erbringen. Die Hipp medical AG hat sich in diesem anspruchsvollen Umfeld schnell zu einem leistungsfähigen Partner und technologischen Vorreiter entwickelt.
Permanente Innovationen und der Mut zu Neuem zeichnen die Hipp Technology Group aus. 1993 von Markus Hipp in der elterlichen Garage gegründet, stieg Hipp Präzisionstechnik schnell zur festen Grösse in der Präzisionsfertigung auf. Um das Angebot auf die Medizintechnik auszurichten, wurde 2008 die Hipp medical AG gegründet, die sich auf schneidende Werkzeuge wie Knochenbohrer, Instrumente und Implantate für den Dentalbereich konzentriert.
Spezifisch nach Kundenwunsch
Sämtliche Implantate und orthopädischen Instrumente werden spezifisch nach Kundenwunsch mit einer sehr hohen Fertigungstiefe und extremer Präzision hergestellt. Dabei sieht sich das Unternehmen in erster Linie als strategischer Partner seiner Kunden. Es begleitet sie von der Idee, über die laufende Entwicklung mit Tests und Laboruntersuchungen bis hin zur Fertigung. Knochenbohrer, Gewindeschneider, Schanzschrauben und Bohrdrähte sind exakt abgestimmt auf die auftretenden Bruchkräfte, das Drehmoment und die Wärmeentwicklung. Entscheidend dabei ist die Ausführung der Schneiden. Mittels feinster Sensorik werden die bestmöglichen Geometrien an den Bohrwerkzeugen getestet. Zerspant werden ausschliesslich Titan und medizinischer Edelstahl. In den letzten fünf Jahren wurden so über 6000 verschiedene Produkte in Losgrössen zwischen 1 und 1000 Teilen produziert.
Hochmoderne Fertigungstechnologie
Da die Fertigungskapazitäten am Standort Kolbingen nicht mehr ausreichten, wurde 2022 das neue Werk in Renquishausen bezogen. Der Begriff «Fabrik der Zukunft» trifft hier wirklich zu. Der Betrieb übertrifft viele Kliniken in Ambiente und Sauberkeit, die Abläufe sind bis ins Detail optimiert, und der hochmoderne, vollautomatisierte Maschinenpark gewährleistet eine Fertigungstechnologie mit 100 Prozent Qualitätskontrolle. Zusätzlich sind im Gebäude die Konstruktionsabteilung, die Reinraumproduktion, die automatisierte Messtechnik sowie die Baugruppenmontage untergebracht.
Ralf Gfrörer, Head of Machining bei Hipp medical, nutzt die neueste Generation von CNC-Mehrspindel- und Langdrehautomaten, vollautomatisierten Fräszentren sowie Erodier- und Schleifmaschinen. Beim Umzug wurde auch das Fluidmanagement genau analysiert. Hipp medical verwendet zur Kühlung und Schmierung aller Maschinen ausschliesslich Schleiföl. Sinnvoll, da vollkommene Keimfreiheit und Sauberkeit ein Muss sind. Das Wasser in Kühlschmierstoffemulsionen birgt die Gefahr, dass sich Bakterien und Pilze bilden können.
Diese wiederum können an den Werkstücken anhaften, was intensive Reinigungsprozesse erfordert. Ein weiterer Aspekt ist die Nachhaltigkeit: Das Schneidöl wird immer wieder aufbereitet und wurde sogar beim Umzug von Kolbingen nach Renquishausen mitgenommen. Dabei kam die Idee auf, das Nachfüllen, Kontrollieren, Filtern und Aufbereiten zu automatisieren – Hipp medical wandte sich an Motorex, den langjährigen Partner im Bereich Schneidöl.
Automatisierte Schneidölüberwachung und -steuerung
Motorex hat vor drei Jahren mit FLUIDLYNX ein System entwickelt, das wasserlösliche Kühlschmierstoffe automatisch überwacht und steuert. Dieses System hat sich hervorragend bewährt und ist vielfach im Einsatz. Daraufhin entwickelten die Technologen die FLUIDLYNX NEATOIL BOX [1] für Schneidöl, an die bis zu zwölf Maschinen angeschlossen werden können. Hipp medical war der erste Kunde in Deutschland, der dieses System einsetzte. Vor einem Jahr wurden sechs vollautomatisierte Fanuc Robodrill Fräszentren an die NEATOIL BOX angeschlossen. Die Box, ausgestattet mit zahlreichen Sensoren, steuert die Maschinen in programmierbaren Bypass-Zyklen an. Das Öl wird mit einer Unterdruckpumpe in die Box gesogen und auf 3 µm gefiltert. Gleichzeitig misst die Box Temperatur, Viskosität, Menge, Partikelzustand und Füllstand. Bei Bedarf wird automatisch Öl zugeführt. Das System arbeitet sehr zuverlässig und ist nahezu wartungsfrei; es reicht, den Feinstfilter alle zwei Monate zu reinigen und die Ölfässer bei Bedarf auszutauschen.
Nachhaltiger und wirtschaftlicher
Ralf Gfrörer sieht nach einem Jahr zahlreiche Vorteile im System: «In unserer Zerspanung zirkulieren 12’000 bis 14’000 l Schneidöl. Die Box verlängert die Standzeit des Öls, reduziert Entsorgungskosten und verbessert unser Spänemanagement. Unsere Mitarbeitenden werden von «lästigen» Aufgaben befreit und können sich auf Wesentliches konzentrieren.» Früher entschieden Bauchgefühl und Erfahrung über die Qualität des Schneidöls, jetzt zeigt das Dashboard alle relevanten Informationen wie Füllstand, Temperatur und Partikelbeschaffenheit jeder Maschine an. Künftig sollen diese Daten auch per App verfügbar sein. Motorex-Servicetechniker können bereits jetzt aus der Ferne auf die Box zugreifen und zum Beispiel Softwareupdates aufspielen. Mit der FLUIDLYNX NEATOIL BOX konnte ein weiterer Massstab in der Metallzerspanung gesetzt werden.
INFOS | KONTAKT
MOTOREX-BUCHER GROUP
Bern-Zürich-Strasse 31
CH-4901 Langenthal
T +41 (0)62 919 75 75
www.motorex.com
info@motorex.com
Branchentreffpunkt für Medizintechnikunternehmen
9. und 10. September
www.medtech-expo.ch
Die Fachmesse für Industrieautomation
10. und 11. September
www.automation-wetzlar.de
Weltleitmesse für Fügen, Trennen, Beschichten
15. bis 19. September
www.schweissen-schneiden.com