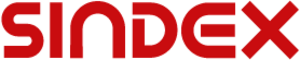
Sindex, Bern
Treffpunkt der Schweizer Technologiebranche
2. bis 4. September
www.sindex.ch
Bilder: Stefan Schneller, ETH Zürich
Nach einem Schlaganfall wieder greifen lernen: Ein Exoskelett von Forschern der ETHZ unterstützt Patienten in der Rehabilitationsphase und im Alltag. Für die optimale Kraftübertragung sorgen Fingerglieder aus Hochleistungskunststoff, die das Kölner Unternehmen igus mit dem 3D-Drucker fertigt.
Alle zwei Minuten erleidet ein Mensch in Deutschland einen Schlaganfall, so die Deutsche Schlaganfall-Gesellschaft. Dafür meist verantwortlich: ein Gefässverschluss oder eine Blutung im Gehirn. Oft entstehen halbseitige Lähmungen oder Bewegungsstörungen. Um diese Folgen in den Griff zu bekommen, trainieren Physiotherapeuten mit Patienten Bewegungen des Alltags – etwa das Greifen einer Tasse Kaffee. Für Kranke oft mühevoll und frustrierend, wissen auch Forscher der Eidgenössischen Technischen Hochschule Zürich (ETHZ). Sie entwickeln deshalb eine Unterstützung: ein Hand-Exoskelett namens RELab tenoexo. Es besteht aus drei Komponenten – einem Handmodul, einem Rucksack und einem Sensorarmband.
Exoskelett deckt 80 Prozent der täglichen Aktivitäten ab
Der Patient zieht das Armband an, fixiert das Handmodul mit Lederriemen an den Fingern und setzt den Rucksack auf, in dem sich Motoren, Batterien, ein Minicomputer und Steuerelektronik befinden. Setzt der Patient die Hand zu einer Bewegung an, leitet das Armband elektromyografische (EMG) Signale an den Computer weiter. Der Rechner erkennt anhand dieser Daten, dass der Mensch eine Greifbewegung beabsichtigt. Um ihm dabei mehr Kraft zu geben, kommen DC-Motoren zum Einsatz. Sie strecken und beugen die Blattfedern der Exoskelett-Finger mit Bowdenzügen – das sind Seilzüge, die auch Kräfte in der Gangschaltung eines Fahrrads übertragen. «Pro Finger bringt das Exoskelett eine Kraft von sechs Newton auf», sagt Jan Dittli, Forscher am ETHZ-Departement Gesundheitswissenschaften und Technologie. «Die drei implementierten Griffe reichen aus, um Objekte bis zirka 500 g zu heben – wie zum Beispiel eine 0,5-l-Wasserflasche.» Das Exoskelett, das bislang in Pilotprojekten in der Rehabilitation zum Einsatz kommt, könnte also in Zukunft ein Alltagsbegleiter werden. «Es gibt weltweit über 50 Millionen Menschen mit einer eingeschränkten Handfunktion, meist bedingt durch Schlaganfälle und Rückenmarkverletzungen. Ihnen könnte unser System zu mehr Eigenständigkeit verhelfen.»
Klassischer 3D-Drucker stösst an Grenzen
Ein Prototyp kommt nicht über Nacht. Die Forscher haben einen langen Weg zurückgelegt. Dabei behilflich war ihnen Jumpei Arata. Der japanische Professor von der Kyushu University hat das Fingerdesign entwickelt. Dafür hat er drei dünne Blattfedern aus rostfreiem Stahl übereinandergelegt und über vier Kunststoffglieder verbunden. Der Bowdenzug ist an der mittleren Feder befestigt. Bewegt ich die mittlere Feder nach vorne, schliessen sich die Finger, zieht sie zurück, öffnet sich die Hand.
Die Blattfedern herzustellen war vergleichsweise einfach. Schwieriger hingegen: Die Herstellung der Fingergelenke. Für die Produktion von Kunststoffbauteilen kommt in der ETHZ ein 3D-Drucker zum Einsatz. Er arbeitet mit dem sogenannten Fused Deposed Modelling (FDM) Verfahren, bei dem Arcylnitril-Butadien-Styrol (ABS) aus der Druckdüse fliesst. Für den Handrücken des Exoskeletts hat der 3D-Druck funktioniert. Doch bei den Fingergelenken? Da ist der Drucker an seine Grenzen gestossen. Zum einen war die Auflösung des Geräts nicht hoch genug, um die Struktur der Fingerglieder zu realisieren. Das Element hält nicht nur die Blattfedern zusammen, sondern verfügt auch über einen filigranen Schliessmechanismus für den Lederriemen. Die Schnalle, in die der Riemen eingefädelt ist, ist kaum breiter als ein Millimeter. Zum anderen war ABS als Druckmaterial ungeeignet. «Die Reibung zwischen den Gelenken und den Blattfedern wäre bei diesem Material zu hoch gewesen», sagt Jan Dittli. «Dadurch wäre uns bei der Bewegung der Finger zu viel Energie verlorengegangen.»
3D-Druckservice fertigt Fingergelenke aus Hochleistungskunststoff
Die Forscher haben sich deshalb auf die Suche nach einer Alternative gemacht. Fündig wurden sie bei igus, ein Kölner Unternehmen, das seit Jahrzehnten Bauteile aus Hochleistungskunststoff für die Industrie entwickelt, und seit 2014 auch einen 3D-Druckservice anbietet. In den Werkhallen des Unternehmens stehen Highend-3D-Drucker, die das Selektive Lasersintern (SLS) beherrschen. Dabei breitet ein Beschichter eine hauchdünne Pulverschicht auf einer Bauplattform aus. Ein Laser verschmilzt das Pulver an den Stellen, die dem digitalen Bauplan in der Computer-Aided-Design (CAD) Datei entsprechen. Anschliessend senkt sich die Bauplattform um eine Schichtstärke ab und der Prozess beginnt von vorn. Schicht für Schicht entstehen die Fingerglieder. «Die Genauigkeit ist dabei hoch genug, um die filigrane Struktur des Gelenks problemlos zu realisieren», erklärt Tom Krause, Leiter Additive Fertigung bei igus.
Anders als beim FDM-Druck sind beim Lasersintern keine Stützstrukturen notwendig – diese Funktion übernimmt das lose Pulver, das nicht aufgeschmolzen ist. Und der Verzicht auf Stützstrukturen bedeutet weniger Nacharbeit. Die Fingergelenke lassen sich also direkt einsetzen. Und auch das Problem der Materialfindung konnte igus lösen. Das Unternehmen hat für das Lasersintern eigens zwei Werkstoffe entwickelt: iglidur I6 und iglidur I3 sind tribologisch optimierte Kunststoffe, speziell entwickelt für bewegte Anwendungen. So liegt die Verschleissfestigkeit bei iglidur I3 bis zu 30 Mal höher im Vergleich zu regulären SLS Material. iglidur I6 zeichnet sich ebenfalls neben der hohen Verschleissfestigkeit zudem durch hohe Zähigkeit aus. Im hauseigenen Testlabor konnte in Versuchen mit 3D-gedruckten Schneckenrädern bislang kein anderer Kunststoff die Lebensdauer von iglidur I6 schlagen. Der Kunststoff ist beispielsweise robuster als klassisches Polyoxymetylen (POM). Um das zu beweisen, haben Ingenieure Zahnräder mit 12 Upm laufen lassen und mit 5 Nm belastet. Ein gefrästes Zahnrad aus POM war nach 321’000 Umdrehungen verschlissen und nach 621’000 gebrochen. Das 3D-gedruckte Zahnrad aus iglidur I6 war hingegen auch nach einer Million Umdrehungen noch voll funktionstüchtig. Die Abnutzung war kaum messbar.
Handmodul wiegt nur 148 g
Durch die geringe Reibung des Hochleistungskunststoffs geht nun beim Beugen der Finger weniger Kraft verloren. Gleichzeitig ist der Kunststoff trotz seiner Robustheit leicht. Ein wichtiger Vorteil für die Forscher, die bei der Entwicklung des Exoskeletts Gewicht sparen möchten. Das Handmodul bringt nur 148 g auf die Waage, der Rucksack lediglich 720 g. «Viele Exoskelette, die in der Rehabilitation zum Einsatz kommen, sind derzeit nicht tragbar. Unsere Lösung hingegen ist leicht und kompakt genug, um sich auch im Alltag zu bewähren und kann somit den Therapiebereich erweitern», sagt Jan Dittli. Dabei lässt sie sich an Patienten anpassen – wie ein Massanzug. «Wir haben einen Algorithmus entwickelt, um das digitale Modell des Exoskeletts mit wenigen Klicks an die Handgrösse des Patienten anzupassen.» Anschliessend schicken die Forscher das digitale Modell in einer STEP-Datei zu igus. Innerhalb weniger Stunden fertigt der 3D-Drucker die Fingergelenke. Keine Selbstverständlichkeit. «Klassische Fertigungstechnologien wie der Spritzguss stossen bei der Herstellung von Unikaten oder niedriger Auflagen an die Grenzen der Wirtschaftlichkeit», sagt Krause. «Aufgrund der zeitaufwendigen Herstellung von Gussformen rentiert sich der Spritzguss in der Regel erst bei Grossserien.» Zudem geniessen Konstrukteure beim 3D-Druck eine hohe Designfreiheit. Anders als bei klassischen Verfahren wie dem Drehen oder Fräsen spielt die Komplexität der Geometrie keine Rolle.
Exoskelett mit Gedanken steuern
RELab tenoexo befindet sich derzeit in der Testphase. Die Forscher haben das Exoskelett mit fünf Patienten in einer Schweizer Reha-Klinik getestet. «Die meisten Testpersonen waren begeistert, da sie mithilfe des Exoskeletts schnelle Ergebnisse erzielt haben», sagt Jan Dittli, der auch schon Modelle für Kinderhände entwickelt hat, die derzeit im Kinderspital in Zürich im Einsatz sind. Und was bringt die Zukunft? Das Exoskelett könnte auf das Sensorarmband verzichten und stattdessen die Aktivität von Hirnregionen messen. Es könnte sich dann mit Gedanken steuern lassen. «Das ist allerdings noch Zukunftsmusik.»
INFOS | KONTAKT
igus® Schweiz GmbH
Winkelstrasse 5
CH-4622 Egerkingen
T +41 (0)62 388 97 97
www.igus.ch
info@igus.ch
Branchentreffpunkt für Medizintechnikunternehmen
9. und 10. September
www.medtech-expo.ch
Die Fachmesse für Industrieautomation
10. und 11. September
www.automation-wetzlar.de
Weltleitmesse für Fügen, Trennen, Beschichten
15. bis 19. September
www.schweissen-schneiden.com