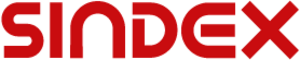
Sindex, Bern
Treffpunkt der Schweizer Technologiebranche
2. bis 4. September
www.sindex.ch
Bild: Archiv
Die Digitalisierung sämtlicher Geschäfts- und Produktionsprozesse schafft die Möglichkeit, Betrieb und Instandhaltung effizienter zu gestalten und völlig neue Geschäftsmodelle zu entwickeln. Ein wichtiges Mittel dazu ist das IIoT als Drehscheibe für die benötigten reichhaltigen Informationen. Für den Einstieg in die Digitalisierung müssen Unternehmen ihre Anlagen häufig mit zusätzlicher Sensorik in und zwischen den Maschinen nachrüsten.
Die Industrie befindet sich auf dem Weg durch die vierte industrielle Revolution. Deren wichtigste Voraussetzung ist die Digitalisierung sämtlicher Geschäfts- und Produktionsprozesse. Sie schafft die Möglichkeit, Betrieb und Instandhaltung effizienter zu gestalten und darüber hinaus völlig neue Geschäftsmodelle zu entwickeln.
Unternehmen setzen auf IoT
Vorrangig die Produktionsindustrie, ebenfalls aber auch die Logistikbranche und die Betreiber von Ver- und Entsorgungsanlagen, sind sich der Bedeutung des IIoT (Industrial Internet of Things) als Drehscheibe für die benötigten reichhaltigen Informationen bewusst. Die Mehrheit der Entscheider hat IIoT als Enabler der digitalen Transformation bereits erkannt. Das zeigt eine vom IT-Marktforschungsunternehmen IDC durchgeführte Studie [1] zum Umsetzungsgrad von IoT im industriellen Sektor. Demnach planten zum Zeitpunkt der Befragung Mitte 2019 drei Viertel der Industrieunternehmen in Deutschland, zeitnah IIoT-Projekte umzusetzen.
Implementierung tut Not
Allerdings haben laut der IDC-Befragung viele Unternehmen noch mit Schwierigkeiten bei der Umsetzung zu kämpfen. Zu diesen gehören Sicherheitsbedenken in Bezug auf Daten- und Netzwerksicherheit ebenso wie eine Unsicherheit in der Auswahl der passenden Plattformen und Verfahren, die sich weiterhin sehr dynamisch entwickeln.
Die meisten KMU verfügen nicht über die Fachkräfte auf den verschiedenen Fachgebieten und Ebenen von der Cloud bis zum Sensor, um IIoT-Projekte mit eigenen Kräften erfolgreich umzusetzen. Deren Implementierung weist eine sehr hohe Komplexität auf und sollte schrittweise erfolgen, um Kosten und Risiko beherrschbar zu halten.
Digitalisierung braucht Daten
In eine IIoT-Strategie sind in aller Regel bestehende Maschinen und Anlagen einzubeziehen. Diese sind aufgrund ihres Alters meist noch nicht in der Lage, die für eine sinnbringende Digitalisierung des Unternehmens benötigten Informationen zu liefern. Sie müssen daher an die neuen Anforderungen angepasst und vor allem mit zusätzlichen Sensoren als Augen und Ohren der informationshungrigen Industrie 4.0 ausgestattet werden.
Anlagenbetreiber können aus dieser informationstechnischen Aufrüstung ihrer Produktionsmittel vielfältige betriebliche Nutzen ziehen. Je reichhaltiger die gewonnenen Daten, desto leichter fällt es, Nachweispflichten zu erfüllen oder die Ursachen von Qualitätsproblemen nachzuverfolgen und in Folge zu beseitigen. Messdatenunterstützte Einstellvorgänge verringern unproduktive Nebenzeiten. Das Wissen um die genaue Ursache ungeplanter Stillstände ermöglicht eine zielgerichtete Instandhaltung und erhöht damit die Anlagenverfügbarkeit. Gleiches gilt für die zustandsabhängige vorausschauende Wartung.
Detaillierte Informationen über einzelne Schritte oder Aspekte im Herstellungsprozess erlauben die maschinenübergreifende Automatisierung des gesamten Herstellungsprozesses. All dies trägt dazu bei, die Gesamtanlageneffizienz und damit die Wettbewerbsfähigkeit zu verbessern. Darüber hinaus ermöglicht es Produktherstellern, schneller auf veränderliche Marktanforderungen zu reagieren und so ihre Krisenfestigkeit zu erhöhen.
«Die Konvergenz herzustellen zwischen der Informations- und Kommunikationstechnik (IKT) und den Operativen Technologien (OT), ist eine logische, zukunftsgerichtete Aufgabe von Automatisierungsunternehmen», erklärt Tobias Thelemann, Produktmanager mechanische Bauelemente und Automatisierungstechnik beim Elektronik-Distributor reichelt elektronik. «Diese haben Erfahrung damit, Maschinen und Anlagenteile zu individuellen Gesamtanlagen mit hoher betrieblicher Effizienz zu formen und können mit dem Schritt zur IIoT ihre Kompetenzen erweitern.»
Sensorik für die Industrie 4.0
«Damit IIoT-Anwendungen einen hohen Mehrwert generieren, müssen diese möglichst viele, teilweise sehr unterschiedliche Daten wertschöpfend weiterverarbeiten», lautet eine Schlussfolgerung in der IIoT-Studie von IDC. Deshalb ist es wichtig, auch bestehende Anlagen mittels Sensorik zu reichhaltigen Informationsquellen auszubauen.
Das Mittel zur Gewinnung der benötigten Informationen sind Sensoren und Messaufnehmer. Sie liefern den darüber liegenden Systemen Informationen über physikalische Kenngrössen und Anlagenzustände als Entscheidungsgrundlagen für Steuerung und Regelung sowie Anlagenbetrieb und Instandhaltung.
Der Einsatzzweck bestimmt die Messgrösse
Das Angebot an Sensoren für das Detektieren und Messen aller physikalischen Parameter von Position, Neigung, Winkel und Distanz über Strom, Energie, Druck und Temperatur bis Füllstand und Durchfluss ist gross, beinahe unüberblickbar. Dazu kommen Systeme der digitalen Bildverarbeitung, etwa LIDAR-Sensoren für die optische Abstands- und Geschwindigkeitsmessung.
«Die Kunst liegt in der Auswahl des passenden Gerätes für die jeweilige Aufgabe», erläutert Tobias Thelemann. «Das betrifft in erster Linie die Bestimmung der Kenngrösse, deren Änderung die erforderlichen Schlüsse zulässt.»
So kann man etwa von der erhöhten Stromaufnahme in einer Motorzuleitung oder einer zu hohen Temperatur auf eine mechanische Schwergängigkeit infolge von Abnützung oder mangelnder Schmierung schliessen. Vibrationen lassen Rückschlüsse auf Verschleisserscheinungen zu, Veränderungen im Durchflussverhalten von Betriebsstoffen legen deren Austausch nahe. Solche Informationen ermöglichen zielgerichtete und daher zeitsparende Überprüfungen und Eingriffe durch das Wartungspersonal. Zudem lässt sich durch eine automatische Anpassung der Bearbeitungsparameter in vielen Fällen der produktive Betrieb der Anlage bis zum Wartungseingriff fortsetzen.
Auch dort, wo die Sensorik durch die Bestimmung von Lage, Weg oder relativen Positionen beweglicher Maschinenteile zur Verbesserung der Anlageneffizienz beiträgt, ist die Wahl der passenden Messgrösse erfolgsentscheidend. Bei der Füllstandsmessung beispielsweise hängt es in erster Linie vom Material der Behälterfüllung ab, welchem der zahlreichen Messprinzipien der Vorzug zu geben ist. «Welches Messverfahren – und damit welche Sensorgrundtype – für die Bestimmung des Anlagenzustandes am zielführendsten ist, kann immer nur im Einzelfall beurteilt werden», bestätigt Tobias Thelemann.
Der Umgebung angepasst
Weitere Kriterien zur Auswahl zusätzlicher Sensoren für das IIoT gibt die oft raue Einsatzumgebung vor, in der diese jahrelang zuverlässig ihre Funktion erfüllen sollen, und das möglichst ohne viel Wartung. Generell kommen für Fertigungsstrassen und Industrieanlagen nur industrietaugliche, robuste Ausführungen in Frage, deren Bauform sich für die Montage am Ort des Geschehens eignet. Auch das Messverfahren muss zu den Umgebungsbedingungen passen, es darf nicht durch die Anlagerung von Staub und Schmutz, Öl oder Feuchtigkeit beeinträchtigt werden.
Der Temperaturbereich der Sensoren sollte dem zu erwartenden Einsatzszenario entsprechend gewählt werden, ebenso die Schutzklasse. «Für die Lebensmittel- oder Pharmaproduktion empfiehlt sich zum Beispiel die Schutzklasse IP69k, die eine regelmässige Hochdruckreinigung übersteht», nennt Tobias Thelemann ein Beispiel. «Für den Betrieb in explosionsgefährdeten Umgebungen sind Sensoren in ATEX-Ausführung erforderlich.»
Konnektivität entscheidet
Entscheidend für die Eignung von Sensoren zum Aufbau von IIoT-Systemen sind deren Schnittstellen zu übergeordneten Systemen. In manchen Fällen ist es sinnvoll, Sensoren an den bestehenden Steuerungssystemen vorbei direkt mit der IT kommunizieren zu lassen. «Dafür gibt es viele Möglichkeiten, etwa das globale Funknetzwerk Sigfox oder das Long Range Wide Area Network (LoRaWAN), die mit hoher Datensicherheit und einen geringen Energiebedarf punkten», kommentiert Tobias Thelemann. «Auch der kommende Mobilfunkstandard 5G soll unter anderem für diese Aufgabenstellung genutzt werden.»
Selbst in anspruchsvollen IIoT-Projekten werden die meisten Sensoren jedoch nicht direkt mit den obersten Schichten der Lösung verbunden, die im Rechenzentrum oder in der Cloud arbeiten. Ihre Daten und Signale sind auch für lokale Steuerungs-, Regelungs- und Visualisierungssysteme relevant. Zudem lässt sich durch das Zwischenschalten einer Ebene mit Steuerungen oder Edge Computern die Menge der zu transportierenden und in darüberliegenden Systemen zu verarbeitenden Daten reduzieren. Das bringt ein erhebliches Einsparungspotenzial.
Deshalb sollten die Konnektivitätseigenschaften der Sensoren für IIoT-Upgrades bestehender Anlagen einerseits zum Datenaufkommen des jeweiligen Sensors passen und andererseits zur bestehenden Systeminfrastruktur in der Anlage. Viele Sensoren sind mit Schnittstellen zu den gängigen Feldbus- und Industrial-Ethernet-Systemen verfügbar. Oft genügt aber auch eine serielle Schnittstelle, etwa RS232 oder USB, und auch die klassisch-einfache analoge Anschaltung über eine 4 bis 20 mA Stromschleife hat noch keineswegs ausgedient.
Alles aus einer Hand
Weil die vorhandenen Maschinensteuerungen meist keine freien Kapazitäten aufweisen, müssen Hersteller von IIoT-Lösungen oft eine lokale Vorverarbeitungsebene einziehen. Sie benötigen dazu neben allen Arten von Sensoren auch die passenden I/O-Systeme, Steuerungssysteme und Edge-Computer einschliesslich der benötigten Cloudanbindungen ebenso wie die erforderliche Netzwerktechnik.
«IIoT-Projekte sind sehr individuell, für ihre Ersteller zählen die kurzfristige Verfügbarkeit und langfristige Wiederbeschaffungsmöglichkeit der Komponenten und Geräte, die sie in Kleinststückzahlen bis hinunter zu Einzelstücken verbauen», weiss Tobias Thelemann. «Nicht nur zur Sicherstellung der Kompatibilität sollten sie daher auf einen Partner setzen, der diese Kriterien erfüllen kann.»
INFOS | KONTAKT
reichelt elektronik GmbH & Co. KG
Elektronikring 1
D-26452 Sande
T +49 (0)4422 955-333
www.reichelt.de
info@reichelt.de
Branchentreffpunkt für Medizintechnikunternehmen
9. und 10. September
www.medtech-expo.ch
Die Fachmesse für Industrieautomation
10. und 11. September
www.automation-wetzlar.de
Weltleitmesse für Fügen, Trennen, Beschichten
15. bis 19. September
www.schweissen-schneiden.com