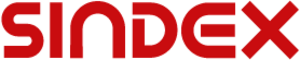
Sindex, Bern
Treffpunkt der Schweizer Technologiebranche
2. bis 4. September
www.sindex.ch
Bilder: Horn/Sauermann
Die Herausforderungen bei der spanenden Bearbeitung von Composites sind die individuellen Eigenschaften der hochbelastbaren Fasern aus Kohlenstoff-, Aramid- oder Glasfasern, die mit Elastomeren, thermoplastischen oder duroplastischen Kunststoffen gebunden werden. Extrem harte und abrasive Fasern sind kombiniert mit weicheren und vor allem wärmeempfindlichen Kunststoffen.
Je nach Lage der Fasern haben Composites isotropische oder anisotropische Eigenschaften. Dazu kommt die grosse Vielfalt an Werkstoffen, bedingt durch die unterschiedliche Ausrichtung von Fasergelegen, unterschiedlichen prozentualen Anteile der Kunststoffe und oft die Kombination mit Metallblechen. Die Anforderungen an die Zerspanung sind saubere und ausrissfreie Flächen ohne Faserüberstände oder Delaminationen. Für die Werkzeugschneide ergeben sich damit widersprüchliche Anforderungen: ein leichter, kühler Schnitt bei sehr stabilen Schneidkanten, eine lange Werkzeugstandzeit und glatte Werkzeugoberflächen, die ein Anhaften des Werkstoffs verhindern.
«Bei der Auslegung von Werkzeugen für die Composite-Bearbeitung gilt es, die verschiedenen Möglichkeiten der Werkzeuggestaltung optimal zu kombinieren: Achskreuzwinkel der Schneiden an den Decklagen für Kompressionsschnitte, Schnittunterteilungen zur Reduzierung des Schnittdrucks, Anritzen der Deckfasern mit Vorschneidern und abgestimmte Span- und Freiwinkeln sind nur einige Parameter, mit denen das optimale Werkzeug definiert werden kann.» analysiert Markus Kannwischer, Geschäftsleiter Technik der Paul Horn GmbH in Tübingen. Sind die makrogeometrischen Parameter bestimmt, kann die Auswahl des entsprechenden Schneidstoffs getroffen werden. Je nach Makrogeometrie fallen bestimmte Möglichkeiten weg: Bei sehr kleinen Werkzeugen bieten Vollhartmetallwerkzeuge deutlich mehr Gestaltungsmöglichkeiten als beispielsweise PKD- oder CVD-bestückte Fräser. Das Substrat sollte eine gewisse Zähigkeit aufweisen, um die dynamischen Schnittkräfte beim Durchtrennen der Fasern gut aufnehmen zu können. Zur Verbesserung der Standzeit werden diese Werkzeuge dann oft diamantbeschichtet. Damit kann eine zähe Schneide mit einer sehr harten Randschicht (Härtewert 10’000 HV05) bei gleichzeitig guter Schärfe erzeugt werden. Dies gewährleistet Prozesssicherheit und eine gute Standmenge. Das Aufimpfen der Diamantkörner funktioniert aber nur, wenn der Kobaltgehalt im Hartmetall nicht zu hoch ist.
Unterschied PKD zu CVD
Bei PKD werden einzelne harte Diamantkörner mit zähem Kobalt oder anderen Elementen gebunden. Der Verbund ist elektrisch leitfähig und kann mittels Erodieren bearbeitet und in Form gebracht werden. CVD besteht ausschliesslich aus Diamant und wird überwiegend gelasert oder geschliffen. Daher ist die Härte von CVD viel höher als die von PKD. Umgekehrt ist allerdings die Zähigkeit und damit der Schutz vor Ausbrüchen bei PKD höher als bei CVD. Da PKD aus einzelnen Diamantkörnern erzeugt wird, lassen sich die Eigenschaften des PKD mittels unterschiedlicher Korngrössen in einer Schneide feiner auf die einzelne Anwendung abstimmen. Damit ist das Parameterfenster bei dem CVD funktioniert deutlich kleiner, als bei PKD. Wenn aber die richtigen Parameter getroffen wurden, ist die Standzeit bei CVD-Werkzeugen wesentlich höher als bei Werkzeugen mit PKD-Bestückung.
Getestete Werkzeuglösungen
Bei Zerspanungstests steht an erster Stelle die Sicherheit: Ergänzend zu den üblichen Sicherheitsvorkehrungen bei Zerspanungstests sind die Aspekte der Staubabsaugung zu beachten. Arbeitsplatzgrenzwerte (AGW) sind hier einzuhalten. «Bei Zerspanungstests in unserem Versuchszentrum arbeiten wir mit speziellen Absaugeinrichtungen. Zum Einsatz kommen alle Messsysteme wie Schnittkraftmessung, Hochgeschwindigkeitskamera und Messsysteme für die Oberflächenmessung. Oft handelt es sich bei Kundenwerkstücken um flächige Teile, die eine entsprechende Spannvorrichtung voraussetzen. Dann führen wir die Funktionstests zunächst bei uns im Haus durch und die finalen Standzeittests erfolgen zusammen mit den Kunden auf deren Maschinen. Bei Grundlagenuntersuchungen und weiterführenden Versuchsreihen arbeiten wir mit Instituten zusammen. Die Beurteilung des Ergebnisses erfolgt immer durch den Kunden, da die Anforderungen an eine Schnittkante oder eine gefräste Oberfläche unterschiedlich bewertet werden», so Markus Kannwischer.
Entwicklung der Einsatzmöglichkeiten
Über alle Branchen hinweg wird der Anteil an Composites weiter ansteigen. Studien sagen hier ein jährliches Wachstum von 10 bis 15 Prozent voraus. Allerdings wird der Einsatz von Composites in den Branchen unterschiedlich beurteilt. Im Bereich Aerospace sind bereits hohe Mengen an CFK-Werkstoffen verbaut und ihr Anteil steigt auch künftig weiter an. Selbst in den Triebwerken werden zukünftig Fanschaufeln mit Anteilen an Carbon und Gehäuse aus Composites zum Einsatz kommen. Im Bereich der PKW ist ein flächiger Einsatz aktuell eher weniger wahrscheinlich, da die heissumgeformten Stahlwerkstoffe hier deutlich aufgeholt haben. Bei den Nutzfahrzeugen und Wohnmobilen kommen allerdings vermehrt flächige GFK-Bauteile zum Tragen. Ein hochinteressanter Bereich sind die Carbon-Betone, die eine Reihe entscheidender Vorteile bieten: dünnere Bauweise, günstigere Montagearbeiten und die Vermeidung von Korrosion. Langzeitstudien zur Haltbarkeit gibt es allerdings noch nicht viele. Können die Kosten von Carbon-Beton weiter reduziert werden, erschliesst sich hier ein riesiger Markt.
Im Bereich der Zerspanungswerkzeuge ist der grösste Markt die Herstellung von Bohrungen. «Wir bei HORN konzentrieren uns hauptsächlich auf das Besäumen und das Erzeugen von Taschen und Durchbrüchen, also die Herstellung von Fräswerkzeugen.» führt Markus Kannwischer aus. Im Bereich der Diamantschichten für VHM-Werkzeuge sorgen neue Multilayer-Diamantschichten für hohe Verschleissfestigkeit bei gleichzeitiger Schärfe der Schneide. Der Einsatz von zäheren Hartmetallen bei gleichzeitiger guter Schichthaftung erweitert das Einsatzgebiet der diamantbeschichteten Vollhartmetallwerkzeuge. Im Bereich der CVD-Schneiden ist das Wissen um die richtigen Einsatzparameter in den letzten Jahren deutlich gewachsen, sodass auch hier riesige Leistungssprünge erzielt werden konnten. Zusammen mit der neuesten Lasertechnik zur Herstellung präziser und scharfer Schneiden konnte der Einsatzbereich von CVD deutlich erweitert werden.
Beispiel Deutsche Technoplast
Ein Beispiel hierfür ist eine Schalt/Klemmnocke zum Flaschentransport einer Getränkeabfüllanlage der deutschen Technoplast aus Wörth an der Donau. 18 unterschiedliche Varianten dieser Schaltnocke in unterschiedlichen Längen werden in Stückzahlen von etwa 250’000 pro Jahr gespritzt und spanend bearbeitet. Der Werkstoff ist Polyetheretherketon (PEEK) mit 30 bis 50 Prozent Kohlefaseranteil. Ein mechanisch und thermisch hochbelastbarer Kunststoff, welcher sich bei der spanenden Bearbeitung sehr abrasiv auf die Werkzeugschneide auswirkt. Die unterschiedlichen Schaltnocken in linker oder rechter Ausführung haben etwa in der Mitte je nach Grösse eine Lagerfläche mit Ø 20, 24 oder 30 mm in der Toleranz e8. Gelagert werden die Schaltnocken in einem Bauteil aus lebensmittelgeeignetem rostfreiem Stahl. 60-fach in Reihe angeordnet tragen sie in der Abfüllmaschine das Gewicht von gefüllten Glasflaschen. Jede dieser Schaltnocken hält in einer berechneten Standzeit von vier Jahren 20 Millionen Lastspiele aus.
Der zuständige Horn-Aussendienstmitarbeiter empfahl als Alternative zu PKD eine CCGT-Schneidplatte mit aufgelöteter CVD-Diamant-Schneide für den schon bisher verwendeten Normhalter mit Standardschnittstelle. Diese CVD-Diamant-Schneide hat einen positiven Schnittwinkel und einen Schneidenradius von 0,4 mm. Der Einsatz dieses neuen Schneidstoffs verbesserte sofort die Standmenge von 750 bis 1000 Teilen auf prozesssichere 3000 Teile mit besserer gleichbleibender Oberflächenqualität über die gesamte Standmenge.
INFOS | KONTAKT
Dihawag AG
Zürichstrasse 15
CH-2504 Biel
T +41 (0)32 344 60 60
www.dihawag.ch
info@dihawag.ch
Branchentreffpunkt für Medizintechnikunternehmen
9. und 10. September
www.medtech-expo.ch
Die Fachmesse für Industrieautomation
10. und 11. September
www.automation-wetzlar.de
Weltleitmesse für Fügen, Trennen, Beschichten
15. bis 19. September
www.schweissen-schneiden.com