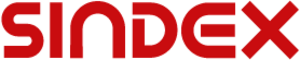
Sindex, Bern
Treffpunkt der Schweizer Technologiebranche
2. bis 4. September
www.sindex.ch
In der Vergangenheit hat sich ein zunehmender Bedarf an innenkonturierten Bauteilen für ganz unterschiedliche Anwendungsgebiete entwickelt, wobei massgeblich die Ziele der Belastungsoptimierung und Gewichtsreduktion verfolgt werden. Die Innenkonturen können hierbei durch verschiedene Bearbeitungsverfahren hergestellt werden.
In der spanenden Fertigung kommen für die Bohrungskonturierung vorwiegend herkömmliche beziehungsweise schwingungsgedämpfte Bohrstangen bis zu einem Länge-zu-Durchmesser-Verhältnis von l/D = 14 zum Einsatz. Sind grössere l/D-Verhältnisse gefordert, können leistengeführte Werkzeuge eingesetzt werden. Bei diesen Werkzeugen handelt es sich vorwiegend um spezielle Auskammerwerkzeuge, welche Bohrungswände mittels eines ausfahrbaren Schneidelementes axial konturieren können [1]. Darüber hinaus ist durch gestiegene Bauteil- und Funktionsanforderungen ein weiterer Bedarf an neuen Möglichkeiten zur komplexen Bohrungskonturierung entstanden. In diesem Zusammenhang hat die Firma BGTB GmbH aus Dortmund in Kooperation mit dem Institut für Spanende Fertigung (ISF) der Technischen Universität Dortmund zwei neuartige Werkzeugsysteme entwickelt, welche die fertigungstechnischen Möglichkeiten der Bohrungskonturierung grundlegend erweitern und neue Potenziale schaffen.
Ganzheitliche Bohrungsinnenbearbeitung
Tiefe Bohrungen mit grossem Bohrungsdurchmesser können mit dem BTA-Tiefbohrverfahren hergestellt werden. Hierbei erzeugt ein leistengeführter BTA-Bohrkopf eine zylindrische Bohrungswand und einen in Abhängigkeit von der Schneidenanordnung definierten Bohrungsgrund [2]. Bei vielen Bauteilen weisen eine an das BTA-Tiefbohren angeschlossene Konturierung sowie Oberflächennachbehandlung der Bohrungswand und des -grundes grosses Potenzial auf. Hydraulikzylinder und Flugzeuglandebeine sind hierfür konkrete Anwendungsbeispiele. Für diesen Zweck wurde ein neuartiges Auskammerwerkzeugsystem entwickelt, welches die Führungsbohrung sowohl spanend konturieren als auch walzend nachbearbeiten kann. Diese dreiteilige Prozesskette aus Vollbohren, Auskammern und mechanischer Nachbearbeitung sowie das zugehörige Werkzeugsystem werden in Bild 1 dargestellt. Die Versuche wurden vollständig auf der institutseigenen Tiefbohrmaschine Giana GGB 560 am Institut für Spanende Fertigung der TU Dortmund durchgeführt.
Im ersten Prozessschritt wird mittels des BTA-Vollbohrverfahrens eine Grundbohrung, auch Führungsbohrung genannt, in das Werkstück eingebracht. Der eingesetzte Vollbohrkopf besitzt Ø von d = 153 mm und verfügt über sieben Schneiden, welche über den Querschnitt verteilt sind. Diese Wendeschneidplatten sind in unterschiedlichen Lagen angeordnet, um ein stabiles Kräftegleichgewicht zu erreichen. Gleichzeitig resultiert aus dieser Werkzeuggestalt ein profilierter Bohrungsgrund. Zudem ergeben sich über den Radius von der Aussenschneide bis zur Werkzeugmitte abfallende Schnittgeschwindigkeiten, welche den Spanbildungsprozess und die Oberflächenbeschaffenheit beeinflussen. Weisslichtmikroskopische Messungen zeigen, dass die Rauheit zur Bohrungsmitte hin mit abnehmender Schnittgeschwindigkeit aufgrund der zunehmenden Reib- und Quetschvorgänge zunimmt.
Im Anschluss an den Bohrprozess wird das neuartige Werkzeugsystem eingesetzt, welches ebenfalls einen Durchmesser von d = 153 mm aufweist und sich mit drei Führungsleisten an der Bohrungswand abstützt. Neben den Führungsleisten werden drei Dämpfungsleisten verwendet, um die Ausbildung von Schwingungen zu reduzieren. Der Werkzeugkopf verfügt über eine drehbar gelagerte Schneidkassette, welche durch eine zusätzliche NC-Achse angesteuert wird. Mittels einer Drehbewegung des Wendeschneidplattenhalters sowie einer rotatorischen Werkstück- und translatorischen Werkzeugbewegung können sowohl der Bohrungsgrund als auch die Bohrungswand nahezu beliebig in einer Aufspannung bearbeitet werden. Durch eine entsprechende NC-Programmierung ergeben sich folglich vielfältige Möglichkeiten der Bohrungskonturierung. Diese umfassen unter anderem das erstmalige Auskammern im Bohrungsgrund sowie gezielte Übergänge zwischen Bohrungsgrund und -wand. Mit dem Werkzeugsystem können Schnittgeschwindigkeiten, Vorschübe und Schnitttiefen flexibel gewählt und angepasst werden, um konstante und hohe Oberflächengüten zu erzielen. Eine bis zu einem Maximalwert frei wählbare Drehzahl ermöglicht ein über einen weiten Bereich konstantes Schnittgeschwindigkeitsniveau. Die resultierende hohe sowie gleichmässige Oberflächenqualität aller bearbeiteten Bereiche wurde dabei mittels der konfokalen Weisslichtmikroskopie bestätigt. Im Rahmen der Versuche wurden Bauteile verschiedener Einsatz- und Vergütungsstähle (C45, 42CrMo4+QT, 16MnCr5) verwendet, um komplexe Konturen in tiefgebohrten Grundbohrungen erzeugen zu können.
Neben der Bohrungsinnenbearbeitung ermöglicht das System eine Oberflächennachbearbeitung. Die Schneidkassette kann gegen eine Walzkassette getauscht werden, die ein angepasstes Festwalzwerkzeug der Fa. Ecoroll AG Werkzeugtechnik trägt. In dieser Weise kann die Prozesskette sowohl um das Glatt- als auch um das Festwalzen ergänzt werden. In den Versuchen wurde eine zuvor konturierte Bohrung im Bohrungsgrund und an der Bohrungswand vollständig mit einem Walzdruck von p = 400 bar gewalzt. Dies führt zu einer deutlichen Steigerung der Oberflächengüte und einer Erhöhung der Randzonenhärte. Bild 2 stellt beispielhafte Konturen der drei Prozessschritte mit der ermittelten Rauheit dar.
Herstellung tiefer nicht kreisförmiger Bohrungen
Über die fertigungstechnischen Möglichkeiten herkömmlicher Auskammerverfahren hinaus besteht in der Industrie die Nachfrage nach innovativen Bearbeitungsverfahren für nicht rotationssymmetrische Innenkonturen. Beispielhafte Bauteile finden sich in der Erdöl- und Gasförderung in Form von Statoren für Moineau-Motoren sowie in der Verfahrenstechnik für strömungsleitende Rohre [3]. Um derartige Bauteile herzustellen und das klassische Auskammern um eine Dimension erweitern zu können, wurde ein weiteres neuartiges Werkzeugsystem entwickelt. Wie in Bild 3 skizziert, wurden die spezifischen Komponenten ebenfalls in den Aufbau einer Tiefbohrmaschine integriert, auf welcher im vorherigen Prozessschritt die notwendige, präzise Führungsbohrung in das Bauteil eingebracht werden kann. Die Aussenstange des Bohrgestänges trägt den leistengeführten Bohrkopf und wird in der Werkzeugspindel gespannt. Die Anbindung des Schieberantriebs erfolgt an einer Konsole auf der Rückseite des Spindelschlittens der Tiefbohrmaschine. Mittels einer eigens entwickelten Mechanik greift eine Abtastrolle die Kontur einer montierten Kurvenschablone ab. Die hierbei entstehende Bewegung kann in eine oszillierende Rotationsbewegung umgewandelt und in die Pendelstange weitergeleitet werden. Diese Stange ist mit einem Exzenter im Werkzeug verbunden und kann durch die Rotationsbewegung den im Bohrkopf integrierten Schieber radial ein- und ausstellen. Somit fährt die Schneide pro Umdrehung in Abhängigkeit von der zu erzeugenden Profilkontur mehrmals periodisch aus und ein. Es handelt sich um ein ziehendes Verfahren, bei dem sich das Werkzeug durch die integrierten Führungsleisten in einer Vorbohrung abstützt.
Die Schneidbewegung hebt sich bei diesem Verfahren deutlich von allen bisherigen Verfahren der Innenbearbeitung ab. Durch das Ausstellen der Schneide wird neben dem axialen Bohrvorschub ein weiterer Vorschub in radialer Richtung realisiert, der abhängig vom Profil zu sich ändernden Schnitttiefen führt (Bild 4). Das mehrmalige Aus- und Einfahren der Schneide führt zu einer extremen dynamischen Beanspruchung der Schneidkante. Darüber hinaus bedingt die radiale Ausstellbewegung eine Änderung der Schnittgeschwindigkeit. Durch die Überlagerung einer rotatorischen und einer translatorischen Bewegung variiert die Schnittgeschwindigkeit in Betrag und Orientierung. Die Veränderung der Beträge und der Orientierung der Kräfte bewirkt, dass die resultierende Zerspankraft während einer Umdrehung in verschiedenen Winkeln an der Schneide angreift. Folglich ergibt sich eine hochdynamische Belastung der Schneide, wobei die stetigen Richtungswechsel zu einem Wechsel aus Zug- und Druckbeanspruchung führen. Darüber hinaus gestalten sich bei diesem Verfahren Spanbruch und -abfuhr aufgrund eines variierenden Werkzeugneigungswinkels als technisch anspruchsvoll.
Trotz der vielfältigen Herausforderungen konnten auf der institutseigenen Tiefbohrmaschine verschiedene nicht kreisförmige Innenkonturen in Bauteile unterschiedlicher Materialien erfolgreich eingebracht werden. Dabei erfordert die hohe Schneidplattenbelastung bei längeren Bauteilen einen Werkzeugwechsel im Prozess. Hierfür wurde eine Wiederanschnittsstrategie entwickelt, bei der der Prozess gestoppt und ein Werkzeugwechsel durchgeführt wird. Im Anschluss kann das Profil in einer definierten Position wieder angeschnitten werden. Auf diese Weise ist es gelungen, ein Bauteil des Vergütungsstahl 42CrMo4+QT über eine Länge von l = 2400 mm bei einem Durchmesser von d = 46…57 mm auszukammern.
Die Autoren bedanken sich beim Bundesministerium für Wirtschaft und Energie (BMWi) für die Förderung des Forschungsvorhabens (ZIM-Projekt) «Entwicklung von Kombinationswerkzeugen zum Spanen und Walzen von Oberflächen in Bauteilen mit komplexen Innenkonturen (SWO-BIK)» und des Forschungsvorhabens (ZIM-Projekt) «Entwicklung eines Verfahrens zur Herstellung tiefer Bohrungen mit nicht kreisförmigen Querschnitten (AK-UR)». Ein grosser Dank gilt der BGTB GmbH aus Dortmund für die erfolgreiche Zusammenarbeit in den Forschungsprojekten.
ZU DEN AUTOREN
Timo Rinschede M.Sc.,
Nils Felinks M.Sc. und
Prof. Dr.-Ing. Prof. h.c. Dirk Biermann
Institut für Spanende Fertigung
Technische Universität Dortmund
Baroper Strasse 303
D-44227 Dortmund
Dr.-Ing. Moritz Fuss und
Dr.-Ing. Maximilian Metzger
Beratende Gesellschaft für Tiefbohr- und Zerspanungstechnik (BGTB) GmbH
Dorstfelder Hellweg 60
D-44149 Dortmund
Branchentreffpunkt für Medizintechnikunternehmen
9. und 10. September
www.medtech-expo.ch
Die Fachmesse für Industrieautomation
10. und 11. September
www.automation-wetzlar.de
Weltleitmesse für Fügen, Trennen, Beschichten
15. bis 19. September
www.schweissen-schneiden.com