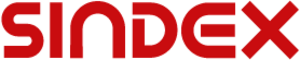
Sindex, Bern
Treffpunkt der Schweizer Technologiebranche
2. bis 4. September
www.sindex.ch
Die Schneidkantenverrundung von Zerspanwerkzeugen beeinflusst massgeblich den Werkzeugverschleiss und kann durch eine angepasste Geometrie die Werkzeugstandzeit verdoppeln. Das Institut für Fertigungstechnik und Werkzeugmaschinen (IFW) der Universität Hannover erforscht bereits seit mehreren Jahren die Wechselwirkung der Schneidkante mit den weiteren Zerspanungsgrössen. Dabei konnte festgestellt werden, dass nur eine an den vorliegenden Zerspanungsprozess angepasste Verrundung Vorteile bringt. Aus diesem Grund ist die Entwicklung einer Methode zur prozess- und materialangepassten Schneidkantenauslegung das übergeordnete Ziel.
Bereits 1876 stellte Prof. Hermann Fischer (TH Hannover) fest, dass «die in der Werkstatt verwendete Schneide stets mehr oder weniger abgerundet ist» und diese Verrundung den «Widerstand der Schneide in Arbeitsrichtung» erhöht [1]. Auch über 140 Jahre später bietet die Verrundung der Schneidkante von Zerspanwerkzeugen, die gezielte Einstellung der sogenannten Schneidkantenmikrogeometrie, noch erhebliches Potenzial für die Industrie. Die Geometrie eines Zerspanwerkzeugs setzt sich aus der Werkzeugmakro- und der Werkzeugmikrogeometrie zusammen. Die Werkzeugmakrogeometrie umfasst bei Fräswerkzeugen das Durchmesser-Längen-Verhältnis, die Schneidkeilgeometrie bezüglich Span- und Freiwinkel, die Zähnezahl, den Drallwinkel sowie die Form und Grösse der Spanräume. Demgegenüber beschreibt die Werkzeugmikrogeometrie die Form der Schneidkante [2]. Die Werkzeugmikrogeometrie oder auch Schneidkantenmikrogeometrie beschreibt den Übergang zwischen der Span- und Freifläche des Schneidkeils, der vereinfacht als Kreisbogen angesehen werden kann. Die Schneidkantenmikrogeometrie besitzt einen signifikanten Einfluss auf das Verschleissverhalten von Zerspanwerkzeugen. So konnte eine Standzeitsteigerung von bis zu 100 Prozent gegenüber schleifscharfen Werkzeugen bei nahezu allen geometrisch bestimmten Zerspanprozessen aufgezeigt werden [3 bis 6]. Eine gezielte Schneidkantenpräparation kann mittels Bürsten, Strahlen, Schleifen oder der Laserbearbeitung erfolgen. Dabei kann die Grösse und Geometrie der Schneidkante an den Zerspanprozess angepasst werden. Die Verrundungsgrösse sowie die Symmetrie kann nach der von Denkena et al. entwickelten K-Methode mithilfe der Schneidkantensegmente Sa und Sg beschrieben werden (Bild 1) [7]. Das Schneidkantensegment Sa ist die Länge von der ideal scharfen Schneidengeometrie bis zum Ablösepunkt der Verrundung auf der Freifläche. Sg ist die Länge bis zum Ablösepunkt auf der Spanfläche [8].
Stets eine Möglichkeit zur Produktivitätssteigerung in der Fertigung
IFW Hannover befasst sich bereits seit mehreren Jahren mit der Erforschung der Schneidkantenverrundung von Zerspanwerkzeugen. Angefangen mit der Beschreibung und Charakterisierung [7 und 8] bis zur Aufnahme des Einsatzverhalten und dem gezielten Einsatz von angepassten Schneidkantenmikrogeometrien [3 bis 6]. Eine verrundete Schneidkante beeinflusst die Stau- und Trennvorgänge während des Zerspanprozesses und hat somit Auswirkungen auf den Spanbildungsprozess. Daraus resultieren abweichende thermische und mechanische Belastungen der Schneidkante, die schliesslich das Einsatzverhalten der Werkzeuge bestimmen. Ein hohes Potenzial konnte bei der Zerspanung von Stahlwerkstoffen mit Hartmetallwerkzeugen aufgezeigt werden [6], da dort massgeblich mechanische Belastungen zum Versagen der Werkzeuge führen. Mithilfe grösserer Verrundungen können die Lasten entlang der Werkzeug-Werkstück Kontaktzone besser verteilt werden, wodurch der Schneidkeil stabilisiert und das Auftreten von Schneidkantenausbrüchen vermieden wird. Gleichzeitig zeigen die Untersuchung, dass bei grosser Schneidkantenverrundung die Tendenz zu Kolk- und Freiflächenverschleiss steigt wodurch die erzielbaren Standzeiten und Oberflächengüten reduziert werden. Durch Erforschung aller Einflussgrossen, die das thermomechanische Lastkollektiv an der Schneide beeinflussen, kann der Übergang zwischen der bruchanfälligen, zu gering verrundeten Schneidkante und der stabilen Verrundung in Abhängigkeit des Zerspanprozesses identifiziert werden. Ziel dabei ist, den industriellen Anwendungspartner Möglichkeiten zu bieten, die Schneidkantenverrundung mithilfe von Auslegungsmethoden an den vorliegenden Zerspanprozess anzupassen, ohne zeit- und kostenintensive Versuche durchzuführen. Dies reduziert den Entwicklungs- und Präparationsaufwand und liefert gleichzeitig optimierte Werkzeuge. Seit den Untersuchungen von Bergmann [6, 9] ist eine Methode zur werkstoffspezifische Auslegung der Schneidkantenverrundung vorhanden. Mithilfe der Methode kann in Abhängigkeit des zu zerspanenden Werkstoffs die optimale Verrundung bestimmt werden [6]. Die Schneidkantenstabilität wird jedoch nicht nur durch die Geometrie der Verrundung beeinflusst, sondern auch massgeblich durch die Eigenschaften des Hartmetalls. Die mechanische und thermische Festigkeit des Schneidstoffs geben die Belastungsgrenzen des Werkzeuges vor. Daher wird in einem aktuellen Projekt der Einfluss unterschiedlicher Hartmetalleigenschaften untersucht, um die Methode weiterzuentwickeln und zu erweitern.
Das Hartmetall macht den Unterschied: Untersuchungen zum Schneidstoffeinfluss
Zur Aufnahme des Werkzeugverschleissverhaltens in Abhängigkeit der Hartmetalleigenschaften sowie des Zusammenwirkens mit der Schneidkantenmikrogeometrie sind experimentelle Drehuntersuchungen durchgeführt worden. In Orthogonaleinstechoperationen auf einer Gildemeister CTX520 Linear Drehmaschine wurden vier unterschiedliche Hartmetalle bei der Bearbeitung von 42CrMo4-QT eingesetzt. Während der Untersuchungen ist der Eckenradius der Wendeschneidplatten nicht im Eingriff befindlich, sodass der Werkzeugverschleiss einfacher mithilfe
eines Digitalmikroskops ausgewertet werden kann. Alle Untersuchungen sind mit einem konstanten Vorschub f = 0,1 mm, einer konstanten Stegbreite b = 2 mm und einer konstanten Schnittgeschwindigkeit vc = 180 m/min durchgeführt worden. Der Spanwinkel ist mit g = -6° ebenso wie der Freiwinkel mit a = 6° in allen Untersuchungen unverändert. Als Hartmetallwerkzeuge sind vom Fraunhofer IKTS Dresden eigens angefertigte Substrate eingesetzt worden, die eine bestimmte thermische beziehungsweise mechanische Eigenschaft besitzen. Als Zielwerte für die Hartmetalleigenschaften wurden eine niedrige und hohe Härte von zirka 1400 HV10 und 1900 HV10 sowie eine niedrige und hohe Wärmeleitfähigkeit von zirka 40 und 80 W/mK festgelegt. Die Hartmetallzusammensetzungen und WC-Korngrössen wurden so gewählt, dass die vier Kombinationen aus niedriger/hoher Härte und niedriger/hoher Wärmeleitfähigkeit erreicht werden konnten. Die Werkzeuge sind anschliessend am IFW Hannover geschliffen und mittels Bürsten verrundet worden. Dabei ist eine breite Variation der Verrundungsgrössen erzeugt worden, um deren Auswirkungen auf das Einsatzverhalten aufnehmen zu können.
Das eingesetzte Hartmetallsubstrat beeinflusst trotz Beschichtung massgeblich den Werkzeugverschleiss. Besonders bei PVD-Beschichtung mit geringen Schichtdicken sind diese bereits nach wenigen Einsatzminuten im Bereich der Schneidkante nicht mehr vorhanden, wodurch das Hartmetallsubstrat für das Einsatzverhalten verantwortlich ist. Der Freiflächenverschleiss im kontinuierlichen Schnitt wird massgeblich durch die Hartmetalleigenschaften und die Schneidkantenmikrogeometrie beeinflusst. So steigt bereits nach einem Schnittweg von lc = 200 m die maximale Verschleissmarkenbreite VBmax von 25 µm (Sa = Sg = 30 µm) auf 55 µm (Sa = Sg = 55 µm) bei dem Substrat «LL», dem Hartmetall mit geringer Wärmeleitfähigkeit und Härte. Der höhere Freiflächenverschleiss ist eine Folge der höheren Schneidkantenbogenlänge la, die in direktem Kontakt mit der Werkstückoberfläche steht [3, 4]. Werden die gleichen Schneidkantenverrundungen bei einem Substrat mit vergleichbarer Wärmeleitfähigkeit aber höherer Härte eingesetzt steigt VBmax nur von 22 auf 38 µm an. Die Beziehung zwischen dem Freiflächenverschleiss und der Schneidkantenmikrogeometrie ist für alle verwendeten Hartmetalle in Bild 2 zu sehen. Der Effekt einer zunehmenden Verschleissmarkenbreite mit höherem la tritt bei jedem Hartmetall auf. Dennoch ist der Einfluss der Hartmetalleigenschaften in den unterschiedlichen Steigungen dieses Zusammenhangs zu erkennen. Eine hohe Härte von durchschnittlich 1.920 HV10 (Sorten «HH» und «HL») führt zu einem durchschnittlichen Verschleissanstieg von 74 Prozent, während die niedrigere Härte von 1.385 HV10 (Sorten «LH» und «LL») eine steilere Steigung mit einem entsprechend höheren Anstieg von 107 Prozent aufweist. Hartmetalle mit höherer Härte haben eine höhere Abriebfestigkeit, was zu einer direkten Reduzierung des Flankenverschleisses führt [10]. Ausserdem ist bei der kleinsten untersuchten Schneidkantenbogenlänge ein Unterschied im g-Achsenabschnitt für VBmax zwischen Hartmetallen gleicher Härte, aber unterschiedlicher Wärmeleitfähigkeit sichtbar. Die Sorten «HL» und «HH» die gleiche Steigung, aber der Gesamtverschleissbetrag der Sorte «HH» mit der höheren Wärmeleitfähigkeit ist etwas höher (zirka 10 Prozent). Die höhere Wärmeleitfähigkeit verbessert den Wärmefluss in das Werkzeug, was zu niedrigeren Temperaturen in der Kontaktzone führt. Die niedrigeren Temperaturen wiederum führen zu einer geringeren Entfestigung des Werkstücks und damit zu einem höheren Verschleiss des Werkzeugs. Ein ähnlicher Effekt tritt auf wenn die Wärmeleitfähigkeit des zu zerspanenden Werkstoffs variiert. So steigt die Temperatur und der Werkzeugverschleiss bei der Bearbeitung von TiAl6V4 im Vergleich zu C45 an [10].
Die Hartmetalleigenschaften und Schneidkantenverrundung stehen aber auch in Wechselwirkung bezüglich der Schneidkantenstabilität. Bild 3 zeigt rasterelektronenmikroskopische Aufnahmen von zwei Substraten mit vergleichbarer Härte aber hoher Wärmeleitfähigkeit «LH» beziehungsweise geringer Wärmeleitfähigkeit «LL». Sofern an beiden Hartmetallwerkzeugen lediglich eine Verrundung von Sa = Sg = 30 µm angebracht wird, weist das Hartmetall mit geringere Wärmeleitfähigkeit («LL») vereinzelte Schneidkantenausbrüche auf. Wird die Wärmeleitfähigkeit gesteigert («LH») und die entstehende Prozesswärme besser abgeführt, reicht diese Verrundung bereits zur Stabilisierung der Schneidkante aus. Dann tritt an dem Werkzeug lediglich abrasiver Freiflächenverschleiss sowie Kolkverschleiss auf. Wird die Verrundung bei beiden Substraten auf Sa = Sg = 100 µm gesteigert, so werden die Prozesskräfte besser entlang des Kontaktbereichs verteilt und auch das Substrat «LL» weist eine stabile Schneidkante auf. Dementsprechend ist bei dem Substrat «LH» eine Vergrösserung der Schneidkantenverrundung nicht zielführend.
Entsprechend darf die Schneidkantenverrundung nicht nur an die Prozessstellgrössen und den Werkstoff angepasst werden [5 bis 8], sondern die Eigenschaften des Schneidstoffes müssen ebenfalls berücksichtigt werden. Nur dadurch kann eine vollständige Ausschöpfung des Werkzeugpotenzials gewährleistet und eine maximale Leistungsfähigkeit erzielt werden. Aus diesen Einsatzuntersuchungen kann dementsprechend die erforderliche Schneidkantenverrundung in Abhängigkeit des eingesetzten Hartmetalls abgeleitet werden. Der nächste Schritt ist der Abgleich des Einsatzverhaltens mit den vorliegenden Belastungen und Hartmetalleigenschaften, um die Zusammenhänge zu quantifizieren und in der Methode von Bergmann zu implementieren. Dies wird weiterhin im Rahmen eines von der DFG geförderten Projekts am IFW Hannover bis Ende des Jahres untersucht und anschliessend zur Verfügung gestellt. Mithilfe dieser Methode können dann substrat- und werkstoffspezifisch die optimalen Schneidkantenmikrogeometrien identifiziert werden.
Danksagung
Die Autoren danken der Deutschen Forschungsgesellschaft (DFG) für die finanzielle Förderung innerhalb des Projekts «DE447/150-1».
ZU DEN AUTOREN
Von Berend Denkena, Alexander Krödel und Tobias Picker
IFW
Institut für Fertigungstechnik
und Werkzeugmaschinen
Leibniz Universität Hannover
An der Universität 2
D-30823 Garbsen
T +49 (0)511 762 4299
www.ifw.uni-hannover.de
picker@ifw.uni-hannover.de
Branchentreffpunkt für Medizintechnikunternehmen
9. und 10. September
www.medtech-expo.ch
Die Fachmesse für Industrieautomation
10. und 11. September
www.automation-wetzlar.de
Weltleitmesse für Fügen, Trennen, Beschichten
15. bis 19. September
www.schweissen-schneiden.com