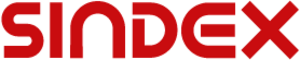
Sindex, Bern
Treffpunkt der Schweizer Technologiebranche
2. bis 4. September
www.sindex.ch
Modernen Zerspanungsprozessen liegen nach wie vor Hardware-Komponenten wie CNC-Werkzeugmaschinen, Zerspanungswerkzeuge, Werkstückspannsysteme und unerlässliche Peripherieelemente wie unter anderem Materialflusseinrichtungen und Kühlschmierstoffe zugrunde. Der Wandel von mechanischen zu mechatronischen Basis-Bausteinen inklusive Software-Tools ist in der Praxis längst vollzogen und schreitet mit zunehmender Digitalisierung weiter voran. Zu nennen wären hier beispielsweise die Vernetzung von CAD-/CAM-Lösungen, verstärkter Einsatz von Technologie-Datenbanken, Werkzeugmanagement, Qualitäts- und Prozesssicherheit sowie höhere produktive Laufzeiten und maximale Systemverfügbarkeit bis hin zur Realisierung der papierlosen, stückzahlflexiblen Teilefertigung.
Während sich der eigentliche Zerspanungsvorgang durch mechanisches Abtragen im Grunde genommen nicht verändert hat, ist der Gesamtprozesses heute wegen vieler zu berücksichtigender Parameter von einer hohen Komplexität gekennzeichnet. Und hier kommt nun die Künstliche Intelligenz ins Spiel. Denn sie bietet die Chance, durch Einbeziehung aller prozessrelevanten Tools und Daten sowie schneller Auswertung sämtlicher Informationen die Zerspanung mehr als nur zu perfektionieren. Die maschinenbau-Redaktion befragte dazu Giari Fiorucci, Geschäftsführer des Digitalisier-Unternehmens c-Com.
Vom abstrakten Begriff Künstliche Intelligenz zur zerspanungstechnischen Realität – wo sehen Sie konkrete Ansatzpunkte zur Nutzung von KI?
Prinzipiell könnte man mit KI natürlich überall ansetzen, also vom Auftragseingang bis zur Lieferung der Produkte. Was konkret die zerspanende Fertigung angeht, gibt es zunächst das kurzfristig wirkende Thema der Problemlösung für ganz bestimmte Bereiche.
Hier setzt eine KI-Lösung genau da an, wo die Unternehmen aktuellen Unterstützungsbedarf haben. Meist ist es ist sehr aufwendig und kostenintensiv, ein individuelles Problem im Produktionsprozess zu analysieren und abzustellen. KI kann hier einen signifikanten Beitrag leisten.
Ein zweiter Ansatzpunkt ist das Thema Prozessoptimierung – sowohl was die Performance von Werkzeugen angeht als auch umfassend gedacht die Steigerung der OEE (Gesamtanlageneffizienz) einer Fertigung. Mithilfe von KI lassen sich Trends in einer Fertigung erkennen, mögliche Folgen ableiten und entsprechende Massnahmen definieren, um eine bestimmte Richtung einzuschlagen.
Heute werden in den meisten Fällen nur einzelne Elemente des Gesamtprozesses betrachtet. Dieser Fakt ist schlussendlich auch der Grund, warum Problemlösungen oder Effizienzsteigerungen oft nicht den gewünschten Effekt bringen. Ein Beispiel dafür ist Predictive Maintenance, die vorausschauende Wartung von Maschinen. Die gibt es schon seit längerem, sie hat sich aber nie wirklich durchgesetzt. Denn die Performance von Maschinen wird durch viele externe Einflussfaktoren beeinflusst, die man nicht über eine Wartung steuern kann. Um Muster oder Anomalien zu identifizieren und vorherzusehen, muss man mehrere Inputs der gesamten Zerspanungskette berücksichtigen. Dabei reden wir aber über eine Menge an Daten, die Menschen alleine inzwischen nicht mehr handeln können. Unterstützende Softwarelösungen wie KI sind meiner Meinung nach inzwischen unabdingbar.
Ist KI hier also mehr als nur optimiertes Werkzeugmanagement?
Definitiv! Mit KI ist es möglich, Werkzeugmanagement auf eine neue Ebene zu bringen. Auch heute noch beschränkt sich in der Praxis Werkzeugmanagement hauptsächlich auf die Logistik. Es gibt natürlich Anbieter wie MAPAL, die über ein Tool Management auch Werkzeug- und Prozessoptimierungen offerieren. Das erfolgt aber manuell, auf Basis des Kopfwissens von Tool Managern oder Anwendungstechnikern, und stellt einen entsprechend hohen Aufwand dar. Bündelt man die Informationen in einem KI-System, ist ein deutlicher Produktivitätsschub möglich. Selbstverständlich weiterhin und immer in Verbindung mit qualifizierten Fachkräften.
Welche Detail-Prozesse und deren Parameter-Optimierungen könnten mittels KI integrativ abgebildet beziehungsweise für mehr Prozesssicherheit und Produktivität genutzt werden? Und wie sieht das in der Praxis aus?
Ich nenne Ihnen ein konkretes Beispiel aus dem Werkzeugbereich. Viele Unternehmen hinterlegen beispielsweise konkrete Standzeiten im System, um auf Nummer sicher zu gehen und einem Werkstückausfall vorzubeugen. Sie verlieren aber dadurch einiges an Performance. Schaut man sich die Bauteilqualität und das Verschleissstadium des Werkzeugs konkret an und bringt dies in Korrelation, kann man die Standzeit des Werkzeugs optimieren.
Genau dieses Thema setzen wir aktuell mit einem Kunden um. Hier erstellen wir aus der konkreten Bauteilqualität und dem Verschleisszustand des Werkzeugs ein sogenanntes Tool-Life-Stretch Programm. Am Anfang ist natürlich der Aufwand, den die Mitarbeiter leisten müssen, um die KI zu «teachen», sehr hoch. Denn hier kommen Informationen aus dem Messraum, aus der Maschine und der Verschleissanalyse des Werkzeugs zusammen. Bei der Verschleisserkennung und -definition setzen wir bei c-Com ja bereits KI ein. Aber bis wir hier ein komplettes System haben, wird es noch einige Zeit dauern. Doch: die ersten Ansätze sind da und werden von uns aktiv verfolgt.
Das grösste Potenzial steckt aber sicher in der bereits erwähnten OEE-Steigerung und damit der erhöhten Maschinenverfügbarkeit. Mit standardisierten Qualitätsmessungen können wir erkennen, wie sich bestimmte KPIs entwickeln. Wenn deren Entwicklung in Richtung Ausschuss führt, bietet sich mithilfe von KI die Möglichkeit, das sehr früh zu unterbinden. Und wir erhalten weniger Ausschussteilen und weniger ungeplante Maschinenstillstände.
Das Thema KI in der zerspanenden Fertigung steht sicherlich überall erst am Anfang. Wir dürfen uns nicht der Illusion hingeben, dass ein KI-System bei einem Unternehmen ad hoc eingeführt werden kann. Davor sind viele Hausaufgaben zu erledigen. Die grösste Herausforderung stellen die Connectivity (IOT) der diversen Systeme und Anlagen sowie die Daten dar, die in sehr grosser Menge zunächst einmal erfasst werden müssen. Und diese Daten müssen zentral in einem System vorliegen, nicht wie aktuell gängig, an vielen verschiedenen Orten. Bei diesem Initialaufwand kann ein Dienstleister den Kunden unterstützen. Aber der Kunde muss bereit sein, die Datensammlung und -zentralisierung aktiv anzugehen. Auch IT-seitig ist eine unternehmerische Lösung notwendig. Hier sehe ich aktuell deutlichen Nachholbedarf, und zwar fast überall auf der Welt.
Bezogen auf CNC-Steuerungen und deren Software – welche Voraussetzungen und Schnittstellen sind hier erforderlich?
Natürlich haben Maschinen unterschiedliche Steuerungen, die angezapft werden müssen. Eine Standardsprache ist sinnvoll und wird ja auch kommen (OPC UA). Aber es ist auch heute schon möglich, die notwendigen Informationen zu erhalten. Vor allem bei etwas älteren Maschinen gestaltet sich das vielleicht aufwendiger, ist aber an sich kein Problem. Es braucht gegebenenfalls eine zusätzliche Hardware beziehungsweise Sensorik, aber dafür gibt es am Markt bereits Lösungen.
Wenn sich KI auf alle prozessrelevanten Bereiche erstreckt – wie lassen sich so verschiedene Prozessdaten aus solchen Komponenten wie Maschine, Werkzeuge, Spanntechnik, Messsysteme usw. in Echtzeit unter einen Hut bringen?
Wie schon erwähnt, die Krux ist die schiere Menge an Daten, die bei so einem Projekt tagtäglich anfällt. Wir haben aktuell ein Projekt mit nur drei angebundenen Maschinen. Und wir reden hier schon von mehreren Gigabytes Daten pro Tag. Bei einer kompletten Fertigungslinie oder einer ganzen Halle kommen Terabytes zusammen, für die eine entsprechende IT-Infrastruktur vor Ort vorhanden sein muss. Eine Cloudlösung ist in Echtzeit eher nicht praktikabel. Man braucht viel Edge Computing – also Intelligenz in der Nähe der Maschine beziehungsweise in einzelnen Komponenten, die die Datenmenge vorarbeitet und sinnvoll komprimiert.
Welche Vorarbeiten muss zum Beispiel ein Zerspanungstechnik-Dienstleister erbringen, um KI nutzenbringend einsetzen zu können?
Es muss ein Use Case, ein konkreter Vorteil für den Kunden da sein. Seit mehreren Jahren gibt es umfassende, allgemeine Lösungsangebote. Hier müssen die Kunden initial extreme Datenmengen liefern, um dann zu sehen, wo sich Effizienzsteigerungen realisieren lassen. In der Praxis wird das – logischerweise – nicht sehr gut angenommen, da der Streuverlust bis zu einem konkreten Nutzen viel zu gross ist. Zusätz-lich muss man wegkommen von diesem Pilotcharakter einer KI-Lösung, bei dem die Kunden mit dem Dienstleister das Produkt fertig entwickeln.
Vielmehr muss der Dienstleister ein klares Problem adressieren und lösen. Nur dann machen die Kunden mit. Auch wir bewegen uns klar da hin. Und tatsächlich gibt es insgesamt noch nicht viele dieser Use Case-basierten Lösungen.
Brauchen die Praktiker vor Ort wie Technologen/Programmierer/Maschinenbediener dafür besondere Qualifikationen?
Nein. Wir wollen ja mit KI den Menschen nicht ersetzen, sondern ihn nutzerfreundlich bei seinen Entscheidungen unterstützen. Im Gegenteil kann es sogar dazu führen, dass für bestimmte Tätigkeiten weniger qualifiziertes Personal benötigt wird.
Gibt es in der Zerspanungstechnik bereits einsatzfähige Lösungen für KI-Anwendungen?
Viele Unternehmen und Dienstleister beschäftigen sich aktiv mit dem Thema, aber tatsächlich sind diese Projekte alle – meines Wissens – noch in einem Pilotstadium.
Bitte nennen Sie uns konkrete KI-Lösungen und sind das dann Vor-Ort-Installationen oder sind sie als Software aus der Cloud verfügbar?
Was c-Com angeht, haben wir für die Themen Verschleisserkennung und Prozessoptimierung konkrete Lösungen, die wir auf der EMO präsentieren werden. Diese bieten wir sowohl aus der Cloud als auch zur On-premise-Installation an. Ausschlaggebend an der Stelle ist die spezifische Anwendung genauso die IT Policy des Kunden.
Und noch zum Schluss: Welche Erwartungen haben Sie im 2021?
Für die c-Com bin ich sehr zuversichtlich für 2021, denn unser Geschäft hat sich erfreulicherweise sehr positiv entwickelt. Da hat uns Corona einerseits sehr geholfen. Denn viele Unternehmen hatten die Zeit und auch den Druck, sich mit Digitalisierung zu beschäftigen. Andererseits gibt es auch negative Implikationen, da wir nicht vor Ort bei den Kunden sein konnten und können. Eine rein virtuell «moderierte» Installation eines Systems dauert viel länger. Auch fehlt der reale Einblick in Prozesse und Abläufe vor Ort beim Kunden, was eigentlich unerlässlich ist.
Wir entwickeln 2021 unser bestehendes Angebot weiter, das aus drei Säulen besteht: DTM – Digital Tool Management, LCM – Life Cycle Management und MAS – Machining Analytics Solutions. Speziell die ersten beiden Säulen sind sehr gut im Markt implementiert, und das über Europa hinaus. Zusätzlich werden wir im Bereich KI zusammen mit Partnern zur EMO sehr interessante Produkte präsentieren. Insgesamt ergibt sich ein sehr positiver Ausblick.
Herr Fiorucci, vielen Dank für die interessanten Ausführungen.
INFOS | KONTAKT
c-Com GmbH
Heinkelstrasse 11
D-73431 Aalen
T +49 (0)7361 5853 001
www.c-com.net
mail@c-com.net
Branchentreffpunkt für Medizintechnikunternehmen
9. und 10. September
www.medtech-expo.ch
Die Fachmesse für Industrieautomation
10. und 11. September
www.automation-wetzlar.de
Weltleitmesse für Fügen, Trennen, Beschichten
15. bis 19. September
www.schweissen-schneiden.com