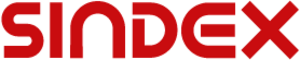
Sindex, Bern
Treffpunkt der Schweizer Technologiebranche
2. bis 4. September
www.sindex.ch
Bild: Christoph Schneeberger
Nachhaltiges Hightech-Material ist teuer. Das könnte sich bald ändern. Christoph Schneeberger entwickelt in seinem ETH Pioneer Fellowship ein Verfahren, mit dem sich faserverstärkte Kunststoffe effizienter herstellen lassen.
Leichtgewichte sind ökologischer – das gilt zumindest für Autos oder Flugzeuge. Denn je schwerer sie sind, desto mehr Energie verbrauchen sie. Beim Bau setzen Hersteller darum vermehrt auf leichte und dennoch stabile Materialien. Faserverstärkte Kunststoffe erfüllen diese Anforderungen ideal: Millionen von hauchdünnen Fasern sorgen für Belastbarkeit, der Kunststoff dazwischen für ein geringes Gewicht. Einziger Nachteil: Das Material ist sehr teuer.
Christoph Schneeberger hat während seines Doktorats am Departement Maschinenbau und Verfahrenstechnik der ETH Zürich einen Prozess entwickelt, der das umweltfreundliche Leichtbau-Material für Hersteller noch attraktiver machen könnte – indem es günstiger wird. «Mein Ziel ist, dass in 20 oder
30 Jahren auch ein vergleichsweise preiswertes Auto aus nachhaltigen Materialien gebaut ist», sagt Christoph Schneeberger zu seiner Motivation.
Hybridfasern leichtgemacht
Die Produktion von faserverstärkten Kunststoffen ist heute aufwändig und kostspielig. Das liegt daran, dass der Kunststoff unter hohem Zeit- und Energieaufwand in ein zuvor gewobenes Fasertextil gepresst wird. Christoph Schneeberger und sein Team wollen dieses Imprägnier-Verfahren überflüssig machen. Und zwar, indem sie die beiden Werkstoffe bereits viel früher im Prozess miteinander kombinieren: bei der Herstellung der Faser. «Mit unserem Ansatz bringen wir den Kunststoff auf die Faser, noch während diese gespinnt wird», erklärt Christoph Schneeberger das Konzept seiner Hybridfasern. Die wissenschaftlichen Grundlagen entwickelte Christoph Schneeberger während seines Doktorats an der ETH. Dass die Methode grundsätzlich funktioniert, konnte er anhand eines Prototyps mit einer einzigen Glasfaser zeigen. Erste Tests weisen darauf hin, dass sich das neuartige Material effizient verarbeiten lässt – vergleichbar mit Organoblechen, die zu den aktuell innovativen Alternativen der Industrie gehören. Diese Eigenschaft könnte man aber viel günstiger erreichen. «Produzieren wir dereinst in grossen Mengen, werden wir nah an die Kosten für die Rohmaterialien kommen», sagt Christoph Schneeberger.
Mit Geduld und Strategie
Nun entwickelt er die Technologie im Rahmen eines ETH Pioneer Fellowships weiter – unterstützt von ETH-Professor Paolo Ermanni sowie der Doktorandin Nicole Aegerter. Letztere untersucht im Rahmen ihrer Promotion unter anderem, welche Mechanismen wirken, wenn man mehrere Fasern gleichzeitig spinnt. Das Ziel ist die Produktion zu skalieren. «Bis Ende des Jahres möchten wir ein halbes Kilo Hybridfasern pro Stunde spinnen», so Christoph Schneeberger.
Von einer Massenproduktion, wie sie etwa für die Luftfahrt- oder Autoindustrie nötig wäre, ist das Trio natürlich noch weit entfernt. «Wir müssen einen Schritt nach dem anderen machen», sagt Christoph Schneeberger. Seine Ambition aber ist klar: Er will das neuartige Leichtbau-Material auf den Markt bringen. Den Fahrplan hat er schon im Kopf: Nächstes Jahr möchte er mit seinem Team ein Startup gründen und Kapital einsammeln. «Dieses werden wir unter anderem benötigen, um neue Infrastruktur für die Produktion zu bauen.» Der Plan ist, zunächst auf Anwendungen zu fokussieren, die mit kleineren Mengen des Verbundwerkstoffs auskommen: etwa Sportgeräte oder Spezialanfertigungen für Autos oder Flugzeuge. So könne man zeigen, dass die Methode hält, was sie verspricht, sagt Christoph Schneeberger. Später wolle man sich als Produzent auch in grösseren Märkten durchsetzen. Einen Namen und eine Webseite hat das Projekt bereits: Antefil Composite Tech.
Rezyklierbare Rotorblätter
Christoph Schneebergers Verfahren könnte aber auch noch für einen anderen Zweck von grossem Nutzen sein. Nämlich um grosse Bauteile, die zurzeit nicht wiederverwertbar sind, nachhaltiger zu machen. Beispiele sind Silos, Gastanks oder Blätter von Windturbinen. Diese werden traditionellerweise aus Glasfasern in Verbund mit sogenannten Duroplasten hergestellt. Es handelt sich dabei um Kunststoffe, die nicht schmelzen und daher nicht recycelbar sind. Als Folge werden etwa Windturbinenblätter nach Ablauf ihrer Lebensdauer gelagert oder umweltschädlich in Deponien entsorgt.
Mit Christoph Schneebergers Verfahren könnte man die Blätter stattdessen aus Thermoplasten fertigen – also aus Kunststoffen, die schmelz- und verformbar sind. Mit diesen Eigenschaften liessen sich Windturbinenblätter wiederverwerten, analog zu PET-Flaschen. Bislang scheitert die Herstellung von recycelbaren Blättern vor allem am Imprägnier-Prozess. Denn es gibt schlicht keine Methode, die für derart grosse Bauteile genügend Druck aufbaut, um die Thermoplasten in die Fasern zu pressen. Antefils Ansatz kommt ohne diesen Prozess aus und macht damit den Weg frei für nachhaltig produzierte Faserverbundstrukturen in beliebiger Grösse.
ZUM AUTOR
Andreas Eberhard
ETH Zürich
Hochschulkommunikation
Rämistrasse 101
CH-8092 Zürich
T +41 (0)44 632 11 11
www.ethz.ch
Branchentreffpunkt für Medizintechnikunternehmen
9. und 10. September
www.medtech-expo.ch
Die Fachmesse für Industrieautomation
10. und 11. September
www.automation-wetzlar.de
Weltleitmesse für Fügen, Trennen, Beschichten
15. bis 19. September
www.schweissen-schneiden.com